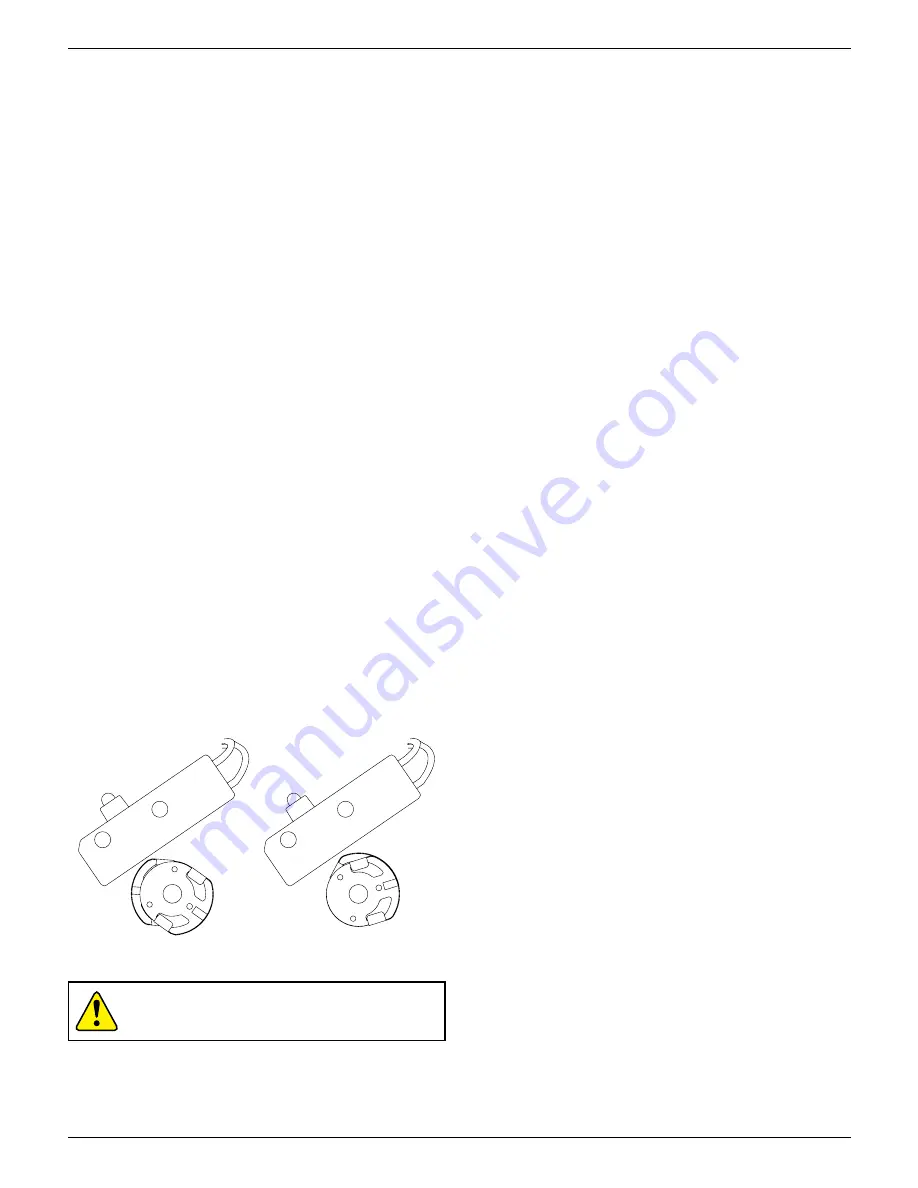
StoneL publication 105406revA
7 QZ 70 en
Quartz |
13
4.1.3
SST solid state proximity senors (X) continued
Touch & Tune switch setting
All adjustments assume you are looking down on the top of the
sensors. The edge of the cam metal strip will be at the edge of the
sensor target when activation occurs. When the cam is released be
sure it slides fully onto the spline. One spline tooth setting is 4 1/2°.
For normally open function (Fig. 1)
1. With the valve in the closed position and if the valve turns
counterclockwise to open, set both cams so that the metal
activation strips are 180° from each other with the bottom cam set
in the middle of the sensor target.
2. Lift the bottom cam and turn counterclockwise until the red LED
goes out then clockwise again until the red LED is lit. (Reverse the
direction of the cam if the valve opens clockwise.)
3. Move the valve to the opposite position (open), push down on
the top cam and rotate counterclockwise until the green LED is lit.
(Reverse the direction of the cam if the valve opens clockwise.)
For the normally open operation, both LEDs will be off during the
actuation period. If the optional green CLOSED visual indicator is used,
the colors would be reversed in steps 1 and 2.
For normally closed function (Fig. 2)
1. With the valve in the closed position, set both cams so that the
metal activation strips are aligned with each other and set in the
middle of the sensor targets.
2. If the valve turns counterclockwise to open, pull up on the bottom
cam and rotate clockwise until the red LED goes out. (If the valve
turns clockwise to open, rotate bottom cam counterclockwise
until it goes out.)
3. Operate the valve to the opposite position (open). Push down on
the top cam. If the green LED is off, rotate top cam clockwise until
it is lit. When the green LED is lit, turn cam counterclockwise until
the green LED goes off.
For the normally closed operation, both the red and green LEDs will
be illuminated during the actuation period. The red LED is off in the
closed position and the green LED is off in the open position. If the
optional green CLOSED visual indicator is used the colors would be
reversed in steps 1 and 2.
Fig. 1 cam set for normally
open sensor function
Fig. 2 cam set for normally
closed sensor function
Caution:
To prevent ignition of hazardous atmospheres,
replace cover before energizing the electrical circuits. Keep
cover tightly closed within operation.