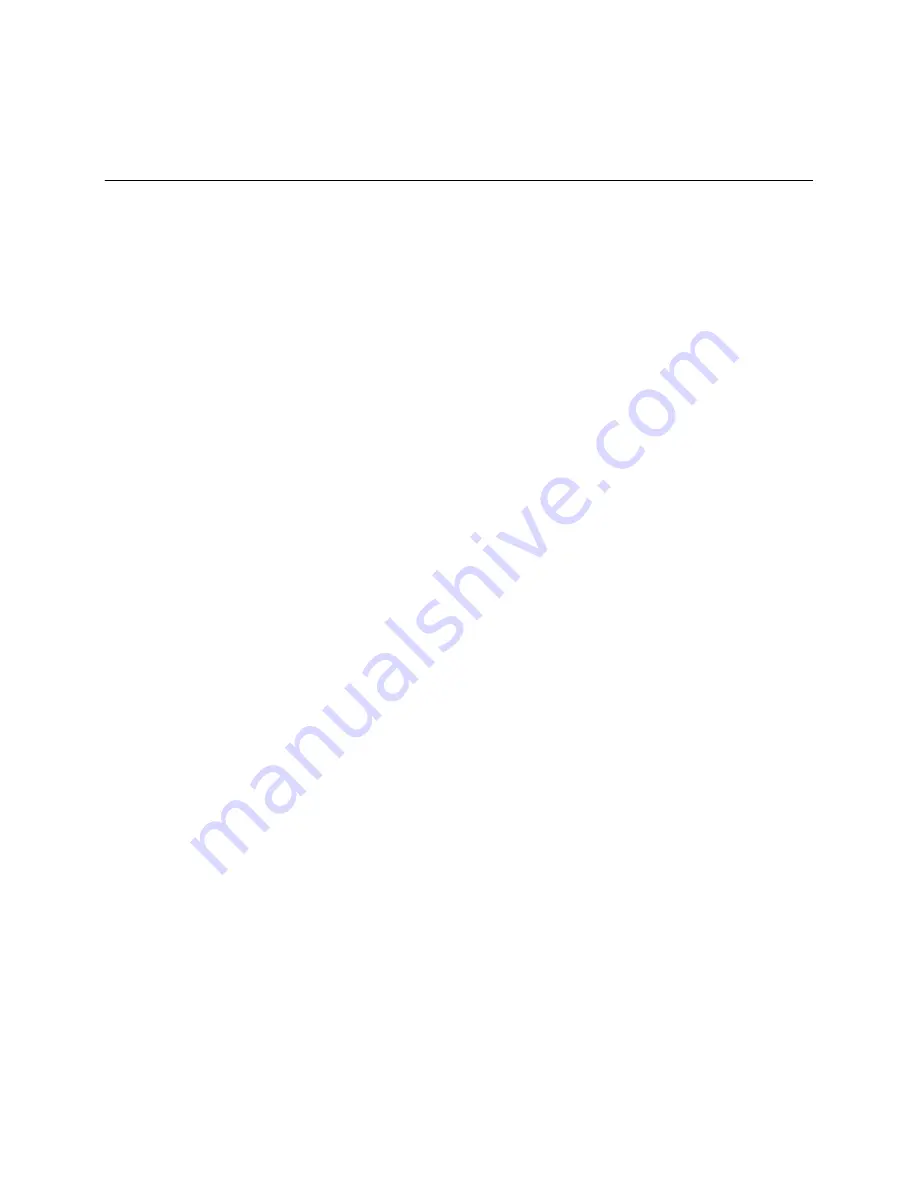
Contents
2
Gas condensing boiler R40
Models and output ................................................................................................. 4
Application possibilities.......................................................................................... 4
Value propositions ................................................................................................. 4
Description ............................................................................................................ 4
Technical description
Technical data ....................................................................................................... 5
Dimensions ............................................................................................................ 6
Declaration of conformity ...................................................................................... 7
Standard boiler ..................................................................................................... 8
Boiler transport ...................................................................................................... 8
Boiler installation ................................................................................................... 8
Norms and regulations
Norms .................................................................................................................... 9
Maintenance ........................................................................................................ 10
Fuel ..................................................................................................................... 10
Combustion air .................................................................................................... 10
Water quality ....................................................................................................... 10
Noise protection .................................................................................................. 11
Antifreeze ............................................................................................................ 11
Flue gas system
Requirements and regulations ............................................................................. 12
Materials .............................................................................................................. 12
Flue gas data ....................................................................................................... 12
Dimensioning single ............................................................................................ 13
Dimensioning cascade ........................................................................................ 14
Neutralisation
General................................................................................................................ 15
Neutralisation systems ........................................................................................ 15
Hydraulic connection
Hydraulic resistance ............................................................................................ 16
∆
T-measurement ................................................................................................. 16
∆
p-measurement ................................................................................................. 16
Hydraulic connection into a system .................................................................... 17
Single .................................................................................................................. 17
Cascade .............................................................................................................. 18
Controls
Basic controls and connections ........................................................................... 19
Control by building managemant system............................................................. 19
Boiler enable signal ............................................................................................. 19
Temperature or capacity setpoint ........................................................................ 19
OK/Alarm output signal ....................................................................................... 20
Heating zone control ........................................................................................... 20
Cascade control .................................................................................................. 20