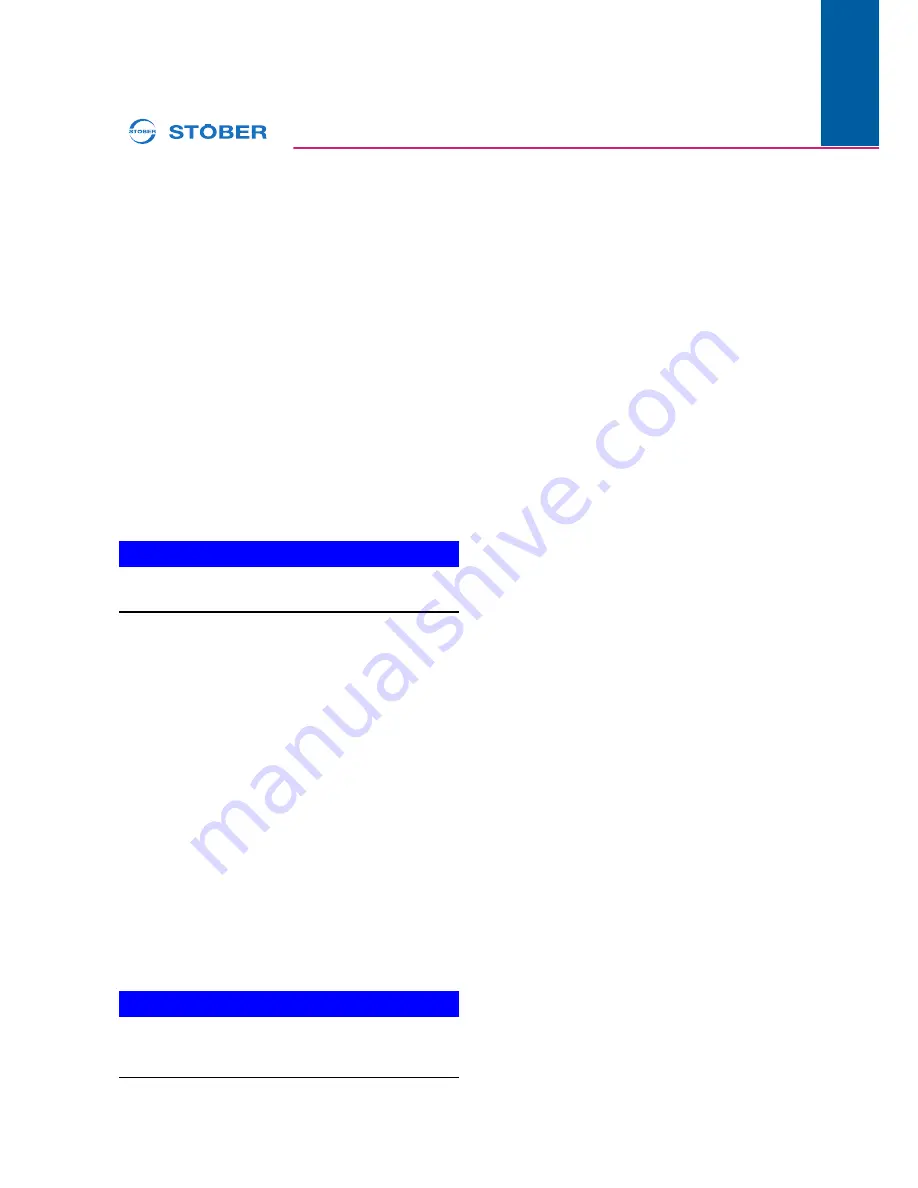
Operating manual
Explosion-protected gear units C/F/K/S
3
01/2019
WE KEEP THINGS MOVING
ID 443028_en.01
en
www.stober.com
5.2 Installation of gear unit
Mount the gear unit on an even, vibration-reducing and tor-
sion resistant substructure. Use screws of strength class 10.9
to fasten the gear unit via the pitch circle diameter. Use
screws of strength class 8.8 for all other fastening types.
Observe the following for assembly:
•
The housing feet and attachment area may not be braced
against each other.
•
The permitted shear and axial forces may not be exceed-
ed.
•
Screws for filling and draining the lubricant as well as
available ventilation valves must be freely accessible.
•
Earthing the gear unit housing via metal components of
the system must be ensured.
Gear units/geared motor with solid shaft; installation of
power transmission elements:
The output shaft is equipped with a centering thread accord-
ing to DIN 332, Sheet 2, which is provided both for fitting and
for axial mounting of transmission elements (gear, chain
wheel, pulley, coupling hub) by means of a central screw.
Shaft ends with a diameter up to 55 have tolerance ISO k6,
those larger than 55 have tolerance ISO m6. The fitting keys
correspond to DIN 6885, Sheet 1.
NOTICE
Damage to the bearing race.
Avoid all impacts to the output shafts.
Gear units/geared motor with hollow shaft and fitting key
connection:
a) Shaft-mounted gear units are mounted on the drive shaft of
the machine to be driven. The reactive torque must be sup-
ported either by flange-mounting of the gear unit or a torque
bracket. If flange-mounted, the flange connection point on the
machine must not exceed a right-angle deviation to the shaft
axis of 0,03/100 mm (danger of distortion of bearings, exces-
sive bending strain on the machine shaft).For gear units with
a hollow shaft, always make sure that the machine shaft is
aligned with the hollow shaft of the gear unit (max. deviation
≤ 0.03 mm).b) The hollow shaft bore is designed according to
tolerance ISO H7 and the keyway according to DIN 6885
Sheet 1. The machine shaft must be ISO k6! The machine
shaft must have a centering thread according to DIN 332,
Sheet 2. The integrated fitting/push-off disk is provided for ax-
ial mounting of the gear unit by means of a central screw.
Fitting the gear unit onto the machine shaft:
- Coat machine shaft with mounting grease
- Coat hollow shaft spiral groove and keyway with mounting
grease
- Fit gear unit by means of central screw.
Do not use ham-
mer!
NOTICE
Rust on of the gear unit.
Never mount the gear unit without lubrication, since it will
rust on and cannot be removed for repairs.
Disassembly:
Press the gear unit off by means of the push-
off disk and matching push-off screw. Support machine shaft
to keep it centered! If the shaft is stuck, we recommend apply-
ing rust penetrating oil to the shaft ends in the key seat for an
extended period.
Gear units/geared motor with hollow shaft and shrink
disk:
The information under a) applies here as well and must be ob-
served! The description of the shrink disk connection and the
installation and safety instructions can be found in the TECH-
NICAL INFORMATION SHEET “Installation instructions for
hollow shaft with shrink disk”.
5.3 Ventilation
Gear units of sizes C0 - C5, F1 - F6 and K1 - K4 are closed
on all sides and are not vented. In contrast, gear units of sizes
C6 - C10, K5 - K10, S0 - S4 are vented as standard, whereby
the position of the vent valve depends on the installation po-
sition.
The vent valves are sealed with a transport lock to prevent lu-
bricant escaping. Remove the transport lock after assembling
the gear unit.
6
Commissioning
6.1 Prior to commissioning
Check the following before commissioning:
•
Is it ensured that the gear unit is adequately vented and
no external heat input (e.g. Via a coupling) is present?
The cooling air may not exceed a temperature of 40° C.
•
Is the transport lock of the vent valves removed?
•
For gear units with hollow shaft and shrink disk: were the
clamping bolts tightened to the specified torque? Is the
cover of the shrink disk properly mounted?
•
Does the attached motor cover the full flange surface of
the motor adapter for gear units with motor adapters so
that IP65 protection class is provided?
•
For gear units with motor adapter ME: is the clamp cou-
pling tightened to the specified torque? Is the plug prop-
erly mounted?
•
If ring screws were dismantled, are the holes sealed with
appropriate plugs?
•
Is it ensured that no gear unit overload relating to the per-
mitted torque can occur due to the mounted motor? (The
permitted torque can be found in the order confirmation.)
•
When operating the attached motor at a drive controller:
is the drive controller parameterized so that a gear unit
overload is prevented?