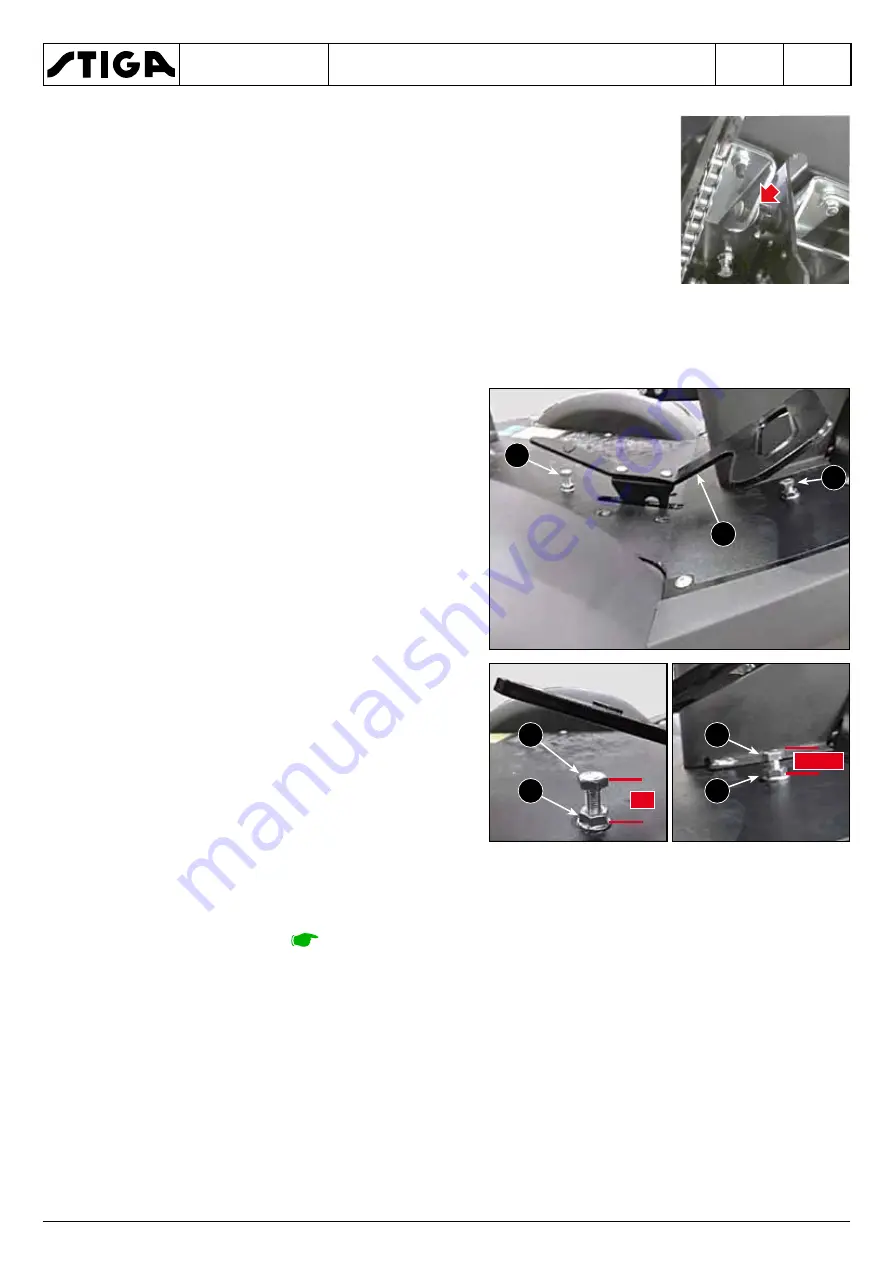
WORKSHOP MANUAL
PARK
Chapter
7 - WHEELS - TRANSMISSION - BRAKE
EDITION
2020
PAGE
81 /
124
When assembling, perform the steps described above in reverse order,
taking care to:
– Insert the cable starting from the front, with the arrow stamped on the
cable facing the front of the machine.
– restore the clamps (8).
7.5.2 Speed adjustment
The stroke of the pedal (1) of the traction deter-
mines the achievement of the foreseen speeds
and is limited by a limit screw (2) in forward way
and a similar one (3) for reversing.
– For the forward adjustment: loosen the lock nut
(4) and adjust the projection of the screw head
(2) to a height of 19 mm.
– To adjust in reverse: loosen the lock nut (5) and
adjust the projection of the head of the screw
(3) to a value “A” of:
14 mm for Park 4WD
27 mm for Park 2WD
Fully tighten the lock nuts (4) and (5) after adjust-
ment.
If the expected results are not found, it is necessary to check that the cable positioning measure-
ments are those indicated in the drawing and, if necessary, restore the correct measurement by
acting on the front joint.
[
3
2
1
2
19 mm
4
3
A
5