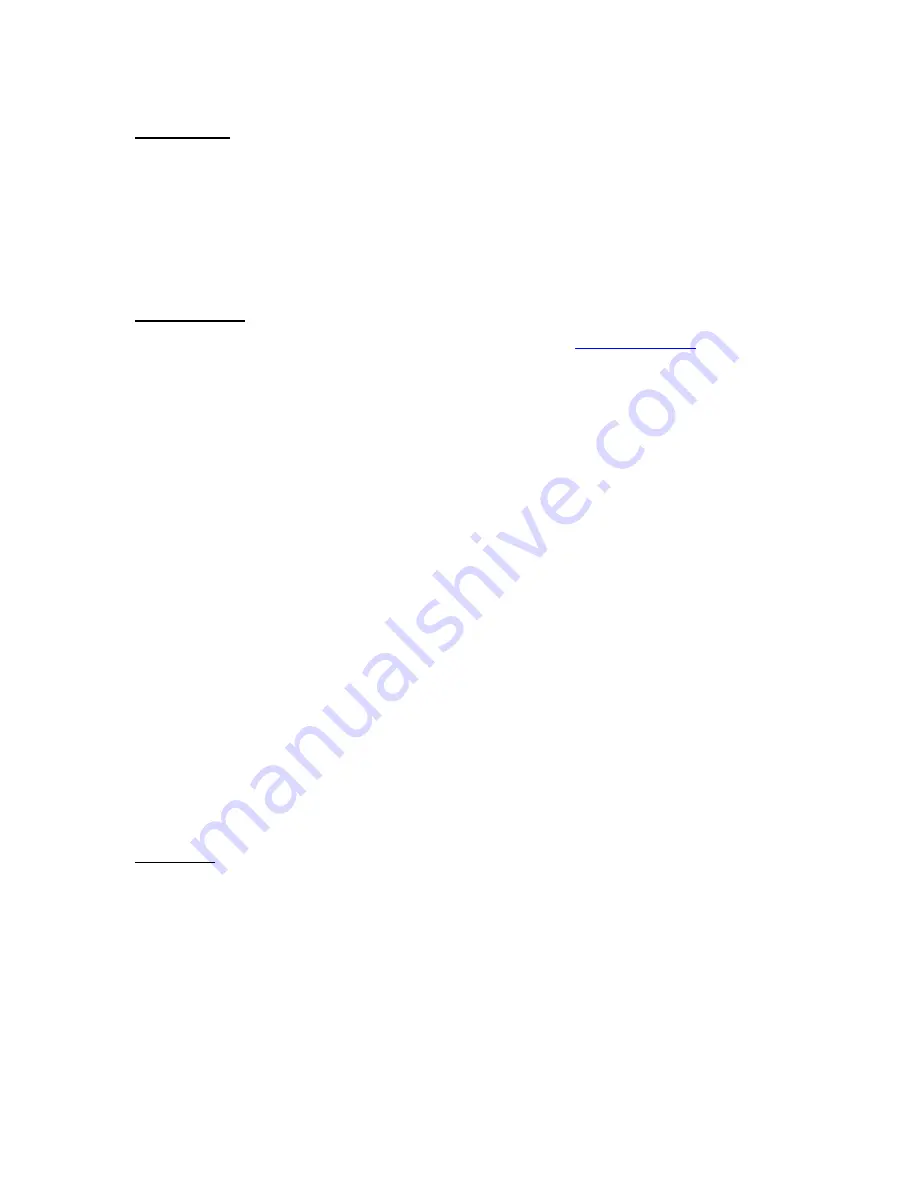
Canopy/Cowl
1.
Trim canopy along scribe line on the molded part.
2.
Trim cowl along scribe line on the molded part.
3.
If you are using a GWS type motor mount you may elect to trim a small hole in the underside of the cowl to
direct more cooling air across the motor and accommodate gearboxes with cooling fins.
4.
Test fit both to fuselage – the fit of the cowl is very precise – some light sanding of the fuselage may be required
to achieve a perfect fit.
Painting Tip: Lay up multiple thin coats of paint, allowing ample time to dry, on the cowl to avoid melting of the part by the
aggressive solvents in your paint.
Final Assembly
Final sand and trim the entire model with AeroFILM Lite – available from
, or equivalent.
Cut CA hinge material into small strips as detailed on the plan sheet.
Determine hinge points for control surfaces then pre-slot elevator, rudder, and wing assemblies at hinge points
to accept CA hinges.
Partially slide horizontal stabilizer into fuselage. Then, insert the elevator joiner. Center the stabilizer and
secure with thin CA.
Fit CA hinges to elevator to horizontal stabilizer - secure with thin CA. Insert 1/16” ply control horn into
horizontal stabilizer on the same side that your push / pull linkage and elevator servo reside – secure with
liberal amounts of thin CA.
The vertical stabilizer keys into the aft section of the turtle deck and the groove in the aft end of the fuselage.
Carefully key the vertical stabilizer into place and secure with thin CA. Trim covering away from bottom of
model to fit the lower Strake/Tail Wheel bracket to fuselage using the provided notches and groove.
Fit CA hinges to rudder and vertical stabilizer – secure with thin CA. Insert 1/16” ply control horn into rudder
and secure with thin CA.
Test fit main gear – simply friction fit to the channel in the wing – sand the edges of gear spade if necessary to
facilitate the fit. Sand only the edges DO NOT significantly thin the plywood on the gear spade.
Harden the wing, locating dowel holes in part F3 with thin CA – work in a dowel, remove, then re-harden, fit a
dowel again and remove. Next cut these dowels to length, sand the leading edge round, and insert into holes
provided in completed center section wing assembly
THE DOWELS SHOULD NEST INTO THE LANDING
GEAR BLOCK BUT NOT PREVENT THE INSTALL OR REMOVAL OF THE LANDING GEAR. TEST FIT
EVERYTHING BEFORE SECURING THE DOWELS WITH THIN CA
– secure with thin CA.
Test fit wing to fuselage. Once satisfied, remove the wing and harden the fuselage reception holes for the last
time with thin CA.
The wing secures by means of the two dowels at the Leading edge and two retaining nylon bolts at the trailing
edge. You should have already installed your blind nuts when assembling the fuselage.
Fit CA hinges to ailerons and wing – secure with thin CA.
Slip the 1/32” ply aileron control horn into the appropriate position on the aileron (see plan sheet for details).
Secure with a dab of thin CA.
Secure cowl and canopy with a small piece of clear tape on either side of the cowl and trim tape around the
canopy (don’t forget the pilot!)
Battery Hatch: Run a length of clear tape along the inside and outside of the hatch opposite the magnetic latch.
Finish model with tail wheel, main wheel, and wheel pants.
Cooling air flow: One final recommendation is to remove a section of covering from the underside aft section of
the fuselage to facilitate good cooling air flow over the electronics. Our preferred method for opening up a
cooling vent is to remove covering from the laser cut lightening hole in-between the rudder pull-pull exits on the
underside of the fuselage.
Radio Gear
Install servos in the appropriate positions. The suggested locations for all setups are as follows: Elevator
servo mounts in the tail and requires a 12” extension to reach the receiver. Rudder servo installs inside
fuselage and is connected to the rudder using the Dubro pull/pull linkage (not provided) The optional external
mounting of the rudder simplifies your rudder pull/pull at the expense of style.
Remember when setting up your pull / pull system – use the holes in the 1/16” ply control horns that best match
the holes used in the servo horns.
Using plan sheet as a guide make up two aileron push rods. Connect aileron linkage to servo using your
preferred mounting method – I suggest using Dubro Mini E/Z Connectors DUB846 and Micro EZ Links.
Apply adhesive back Velcro (not included) to battery tray. Mount battery with Velcro to BT1 battery tray. The
supplied Velcro tie wrap is intended to augment the adhesive back mounting system – not substitute it.
Mount receiver with Double Sided Tape or Velcro inside the fuselage to one side or the other just above former
F7 (be certain it is clear of your pull/pull linkage).
© 2004 Stevens AeroModel.
Page 22 of 31