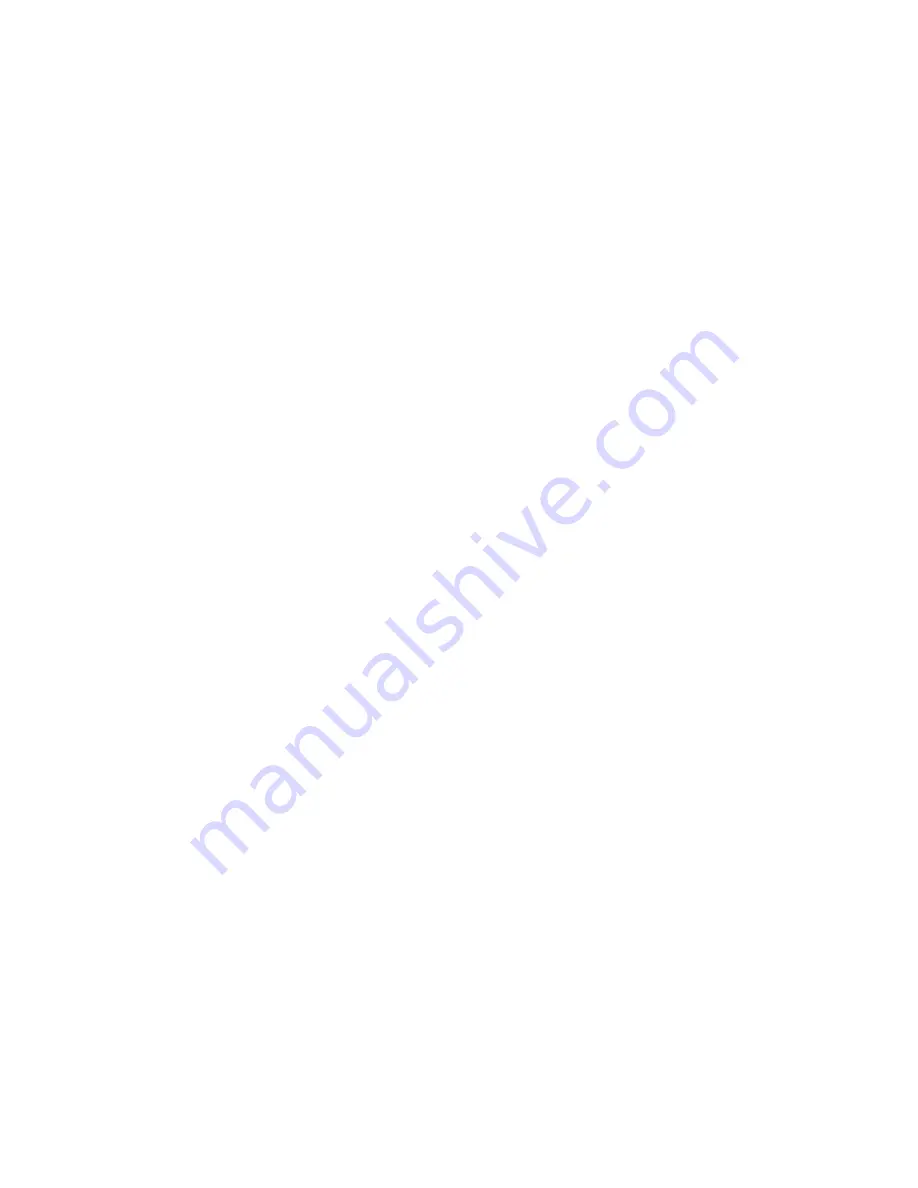
– 10 –
SECTION VII - TROUBLE SHOOTING
continued
Causes for hold conditions in the INITIATE sequence:
1. AC line dropout detection.
2. AC line noise that can prevent a sufficient reading
of the line voltage inputs.
3. Low line voltage brownouts.
The INITIATE sequence also delays the burner motor
starter from being energized and de-energized from an
intermittent AC line input or control input.
Standby
The RM7895A,B,C,D/EC7895A,C; RM7896A,B,C,D is
ready to start an operating sequence when the operat-
ing control input determines a call for heat is present.
The burner switch, limits, operating limit control and all
microcomputer-monitored circuits must be in the
correct state for the relay module to continue into the
PREPURGE sequence.
Normal Start-Up Prepurge
The RM7895A,B,C,D/EC7895A,C; RM7896A,B,C,D
Relay Module provides PREPURGE timing selectable
from two seconds to thirty minutes with power applied
and the operating control indicating a call for heat.
1. The Airflow Interlock, burner switch, Run/Test
switch and all microcomputer-monitored circuits
must also be in the correct operating state.
2. The motor output, terminal 4, is powered to start
the PREPURGE sequence.
3. The Airflow Interlock input closes ten seconds into
PREPURGE or within the specified purge card
timing; otherwise, a recycle to the beginning of
PREPURGE or lockout occurs, depending on how
the Airflow Switch selectable jumper (JR3) is
configured.
Ignition Trials
1. Pilot Flame Establishing Period (PFEP):
a. When the PFEP begins:
(1) The pilot valve and ignition transformer,
terminals 8 and 10, are energized. The
RM7895A,B, EC7895A, and RM7896A,B
have an intermittent pilot valve, terminal 8.
The EC7895C, RM7895C,D, and
RM7896C,D have an interrupted pilot valve,
terminal 8.
(2) Flame must be proven by the end of the ten
second PFEP (four seconds if Configuration
Jumper JR1 is clipped) to allow the
sequence to continue. If a flame is not
proven by the end of PFEP, a safety shut-
down occurs.
b. With flame proven, the ignition, terminal 10, is
de-energized.
2. `Main Flame Establishing Period (MFEP):
a. After Ignition Trials, and with the presence of
flame, the main fuel valve, terminal 9, is pow-
ered. If a flameout occurs, the relay module
locks out or recycles (depending on status of
jumper JR2) within 0.8 or 3 seconds, depending
on the Flame Failure Response Time (FFRT) of
the amplifier.
b. The RM7895C,D/EC7895C, and RM7896C,D
have a ten second MFEP. After the Ignition
Trials and with the presence of flame, the main
fuel valve, terminal 9, is powered. If a flameout
occurs, the relay module locks out within 0.8 or
3 seconds, depending on the amplifier FFRT.
Run
1. The RM7895C,D, EC7895C, RM7896C,D has a
delayed main valve that is energized once the
RUN period is entered.
2. The relay module is now in RUN and remains in
RUN until the controller input, terminal 6, opens,
indicating that the demand is satisfied or a limit has
opened.
Post Purge (RM7896A,B,C,D Only)
After demand is satisfied or a limit opens,
de-energizing terminal 6, the Ignition/Pilot valve,
main valve and delayed main valve, terminals 8, 9 and
21, are de-energized. The blower motor, terminal 4,
remains powered for 15 seconds. Run/Test Switch
(RM7895C,D/EC7895C; RM7896C,D only)
The Run/Test Switch is located on the top side of the
relay module, see Fig. 5. The Run/Test Switch allows
the burner sequence to be altered as follows:
1. In the measured PREPURGE sequence, the Run/
Test Switch, placed in the TEST position, causes
the PREPURGE timing to stop.
2. In the Pilot Flame Establishing Period, the Run/
Test Switch, placed in the TEST position, stops the
timer during the first eight seconds of a ten-second
PFEP selection or during the first three seconds of
a four-second PFEP selection. It also allows for
pilot turn-down test and other burner adjustments.
This activates a fifteen-second flameout timer that
permits pilot flame adjustment without nuisance
safety shutdowns. The Run/Test Switch is ignored
during PFEP for the C and D relay modules if
terminals 8 and 9 or 9 and 21 are jumpered.
IMPORTANT: When the relay module is switched to
the TEST mode, it stops and holds at the next Run/
Test Switch point in the operating sequence. Make
sure that the Run/Test Switch is in the RUN position
before leaving the installation.
Summary of Contents for SDFI
Page 20: ...20 TROUBLESHOOTING GUIDE P 001004 P 001003...
Page 35: ...35...