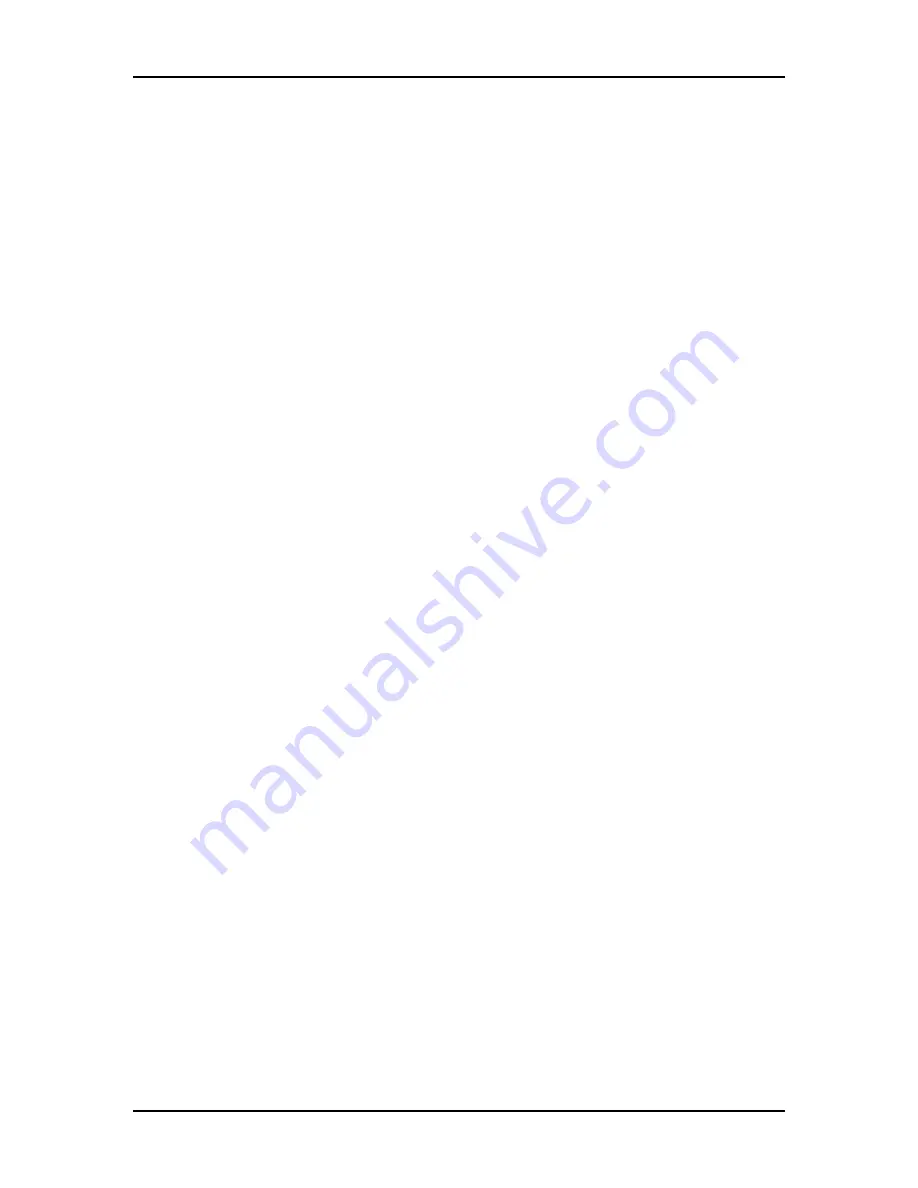
STT 25 – STT 6400
3
Sterling Material Processing retains all rights to change the information in these operating
instructions at any time without notice.
We assume no liability for any errors or direct or indirect damage resulting in context with these
operating instructions.
Copying, translation or publication in any form except for personal use of purchaser requires
approval from Sterling Material Processing.
All rights reserved.