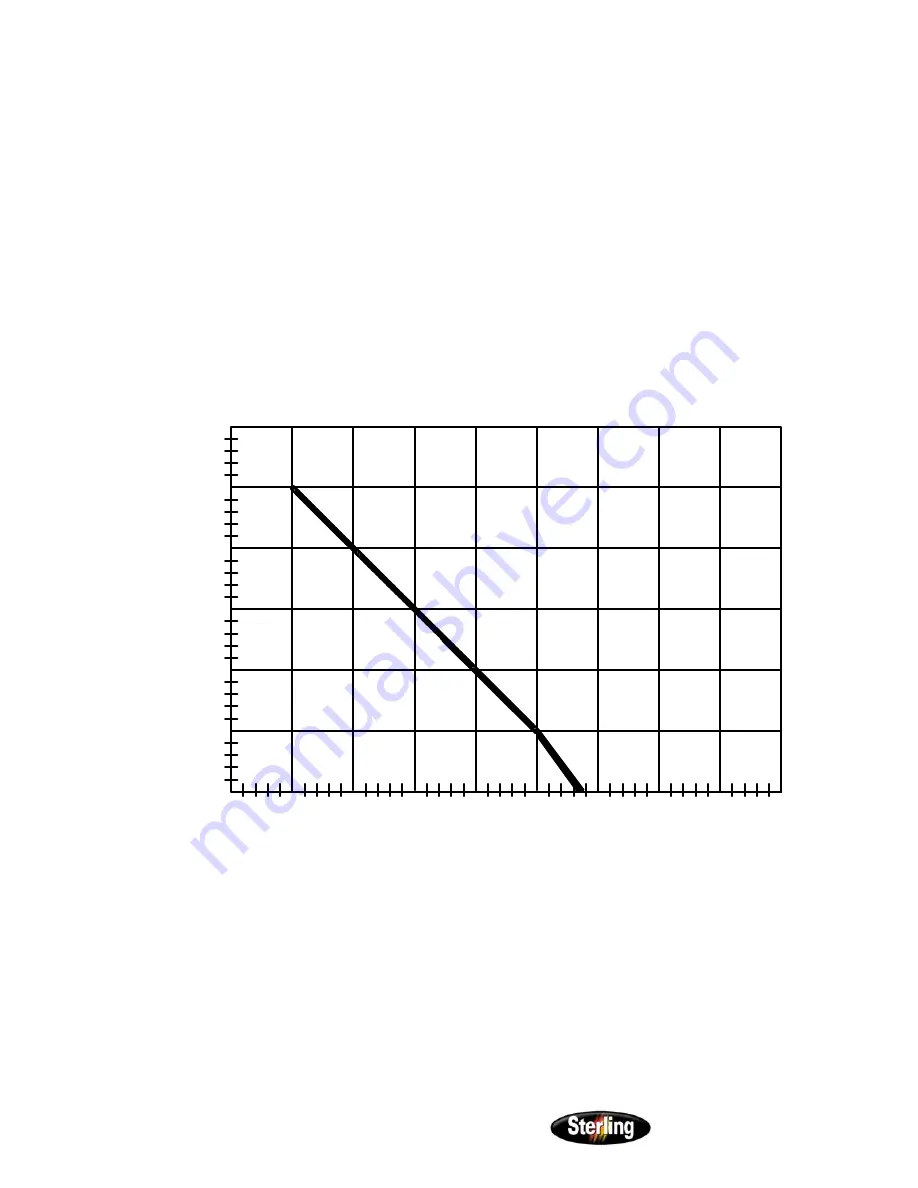
Page 16
SMC Series Chillers
;
A corrosion inhibitor suitable for the materials in the system should be added to the
glycol/water solution.
;
If straight water use is desired, contact the Sterling, Inc. Engineering Department.
;
The six gallon (23 liter) reservoir is
not
designed to withstand water pressure above
5 psi (34 kPa).
;
The fill opening and vent line must be vented to the atmosphere for proper
operation.
Figure 6: Ethylene Glycol Curve
Ethylene Glycol Required
Normal Operating Range between 30°F - 70°F
for Evaporator Freeze Protection
Chilled Water
Operating Temperature °F
(Set Point)
10%
20%
30%
35°
25°
45°
55°
0%
65°
Ethylene
Percent
Glycol
by
Volume
Summary of Contents for 30F to 65F
Page 12: ...Page 12 SMC Series Chillers Figure 4 SMC Cast Iron Centrifugal Pump Curve 1 3 hp 0 249 kW ...
Page 20: ...Page 20 SMC Series Chillers Figure 8 SMC Component Identification ...
Page 36: ...Page 36 SMC Series Chillers Notes ...
Page 40: ...Page 40 SMC Series Chillers Notes ...
Page 41: ...SMC Series Chillers Page 41 Notes ...
Page 42: ...Page 42 SMC Series Chillers Notes Technical Assistance ...