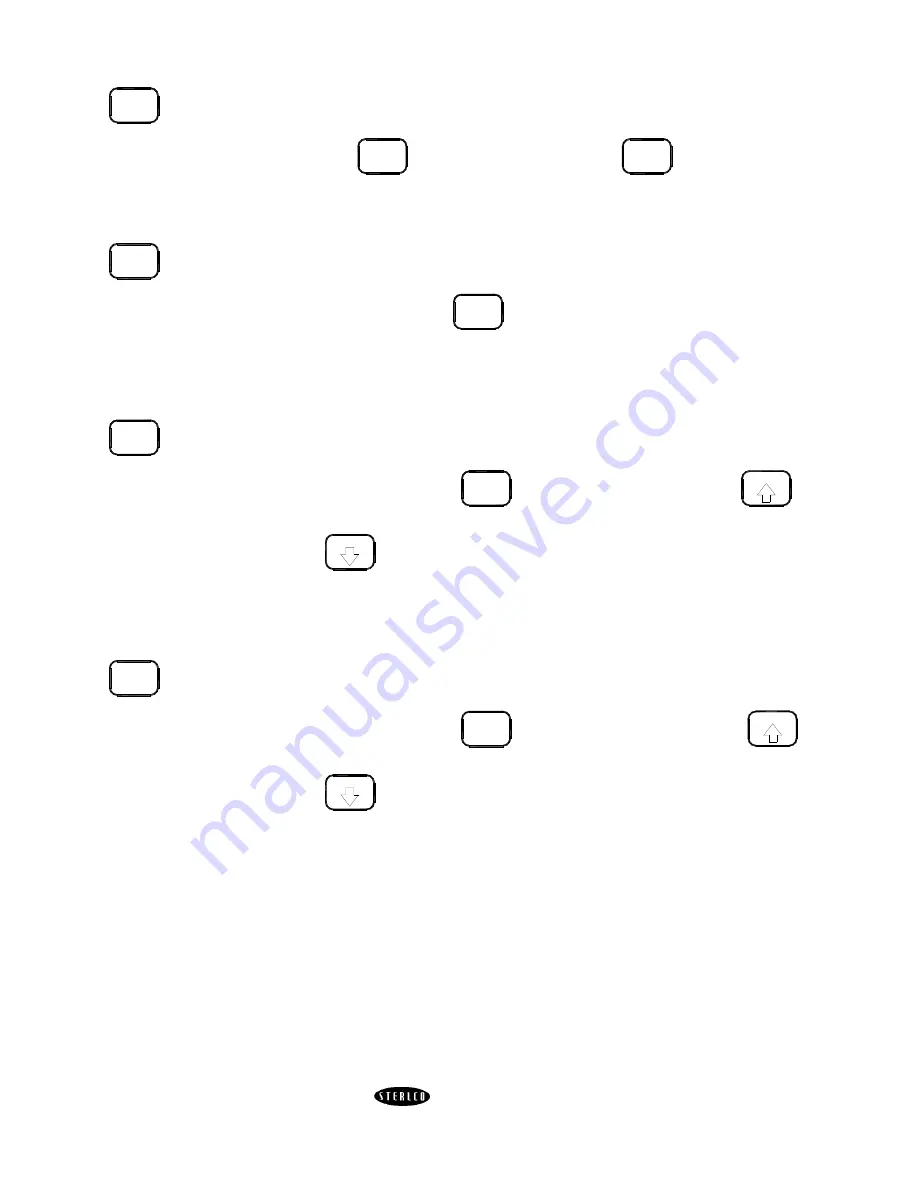
Page 38
6017 Series Hot Oil Large Temperature Control Units
ENTER
ENTER Key
The
ENTER
ENTER
key is used with the
INDEX
INDEX
key menu
to store the value or the item that was changed. If this key is not
pressed, the previously-stored value or item is retained.
INDEX
INDEX Key
Each press of the
INDEX
INDEX
key advances the screen to the
next menu item. Refer to your Sterling/Sterlco M2B Temperature
Control Owner’s Manual for a list of functions available using this
key.
HI
ALARM
HI ALARM Key
Press and hold the
HI
ALARM
HI ALARM
key, then press the
UP
UP Arrow
key to increase the alarm high limit value or press the
DOWN
DOWN Arrow
key to decrease the alarm high limit value
on the
SET POINT
LED screen. Refer to your Sterling/Sterlco
M2B Temperature Control Owner’s Manual for a list of functions
available using this key.
ALARM
LO
LO ALARM Key
Press and hold the
ALARM
LO
LO ALARM
key, then press the
UP
UP Arrow
key to increase the alarm low limit value or press the
DOWN
DOWN Arrow
key to decrease the alarm low limit value on
the
SET POINT
LED screen. Refer to your Sterling/Sterlco M2B
Temperature Control Owner’s Manual for a list of functions
available using this key.
Summary of Contents for 6017 Series
Page 29: ...Page 28 6017 Series Hot Oil Large Temperature Control Units Notes ...
Page 34: ...6017 Series Hot Oil Large Temperature Control Units Page 33 Notes ...
Page 46: ...6017 Series Hot Oil Large Temperature Control Units Page 45 Notes ...
Page 52: ...6017 Series Hot Oil Large Temperature Control Units Page 51 ...
Page 55: ...Page 54 6017 Series Hot Oil Large Temperature Control Units Service Notes ...
Page 56: ...6017 Series Hot Oil Large Temperature Control Units Page 55 Service Notes ...
Page 57: ...Page 56 6017 Series Hot Oil Large Temperature Control Units Service Notes ...