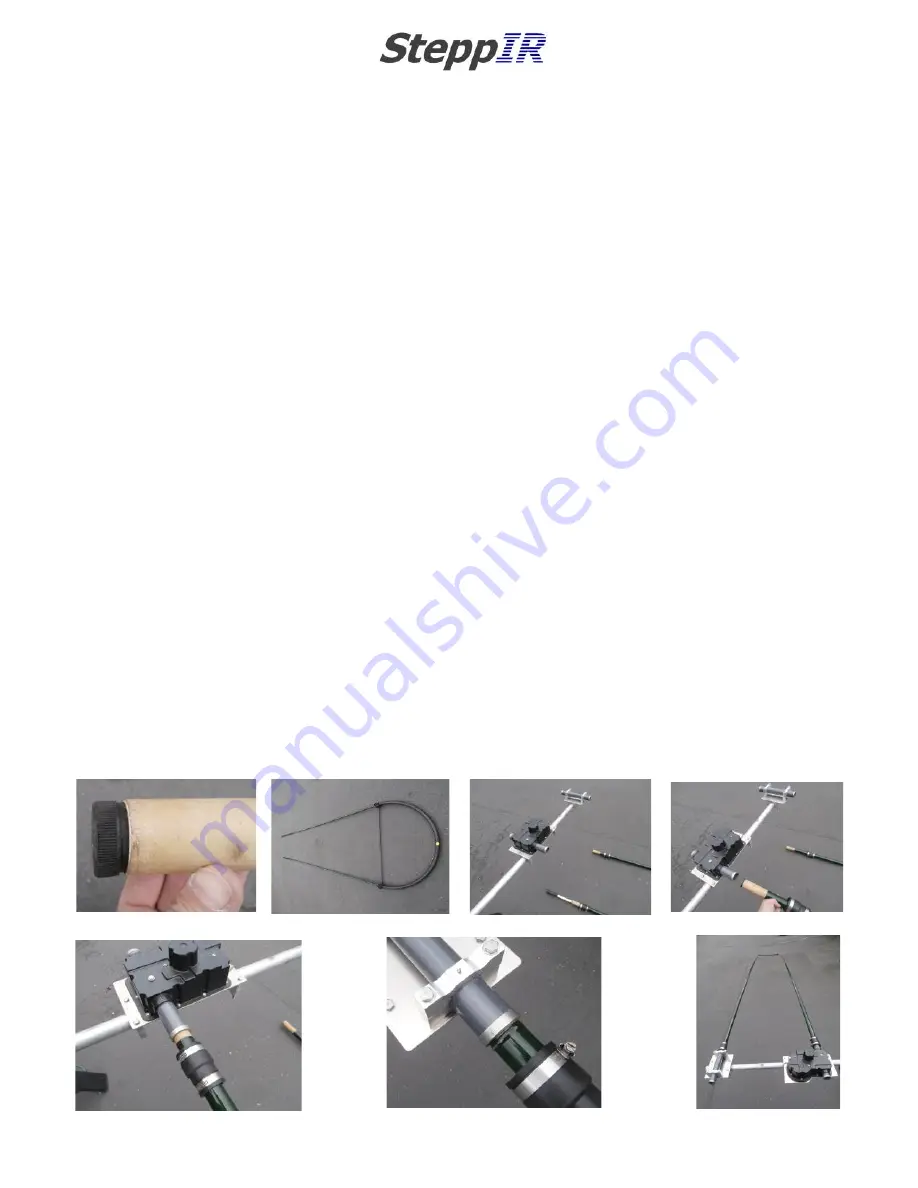
Tech Support:
www.steppir.com/support
Tel: 425.891.6134
Page 62
CHAPTER SEVEN
SECTION 7.1
ATTACH THE ELEMENTS TO THE EHU’s (continued)
SECURING THE ELEMENT SUPPORT TUBE (EST) TO THE EHU (continued)
When attaching the telescoping fiberglass poles to each of the EHU’s, special care must be taken to ensure
that the rubber plugs that are in the base section of each pole are removed before placing the telescoping
poles onto the EHU.
Failure to remove these plugs will result in catastrophic failure of the EHU
.
Figure 7.11
shows how the plug is in place for shipping purposes.
Each end of the DB18 boom has a 40/30 loop for use on 40m and 30m. These loops were prepared earlier in
Chapter Six and should look like the one shown in
figure 7.12
. Be sure to put your quick disconnect boot (PN
10-1006-22) onto the pole before inserting into the EHU.
The CPVC inner guide tube is inserted into the EHU side of the loop assembly as shown in
figure 7.13
. The
guide tube is not required for the non-EHU side of the loop. The non-EHU side of the loop is commonly re-
ferred to as the “return tube”. Insert the guide tube so that the edge of the diverter cone is flush with the
base of the telescoping pole as shown in
figure 7.14
. Slide the pole base and guide tube into the EHU tube
until it bottoms out firmly as shown in
figure 7.15
. There may a small portion of unpainted pole protruding.
This is OK as it is shielded from the sun by the quick disconnect boot.
Align the telescoping pole on the return tube side of the loop. Insert the end firmly into the return tube as
shown in
figure 7.16
. There is a raised area called a locking ring that is molded onto the base section of each
of the telescoping poles. These are there so that the quick disconnect boot cannot “slide” off in the event of
high winds. This raised portion of the base section will rest up against the return tube as shown in
figure 7.16
.
Before tightening the quick disconnect boots, twist the base sections of the telescoping poles until the loop
portion of the element is as level as possible, as shown in
figure 7.17.
Chapter Eight show this leveling pro-
cess in greater detail, specifically
figures 8.29, 8.30 and 8.31
in
Chapter Eight, Section 8.2
. Tighten the quick
disconnect boots firmly. Wait 20 minutes and tighten again—the flexible material will tend to cold flow initially.
It is also a good idea to do a final tightening of all the quick disconnect boots and all fasteners as a last step
before mounting the antenna onto the mast. Repeat above steps for the other half of the loop.
The installation pictures below represent the Reflector element. Repeat the above steps for the Director ele-
ment. They are exactly the same with the exception of the orientation of the EHU and return tube.
FIG. 7.17
FIG. 7.16
FIG. 7.15
FIG. 7.11
FIG. 7.14
FIG. 7.13
FIG. 7.12