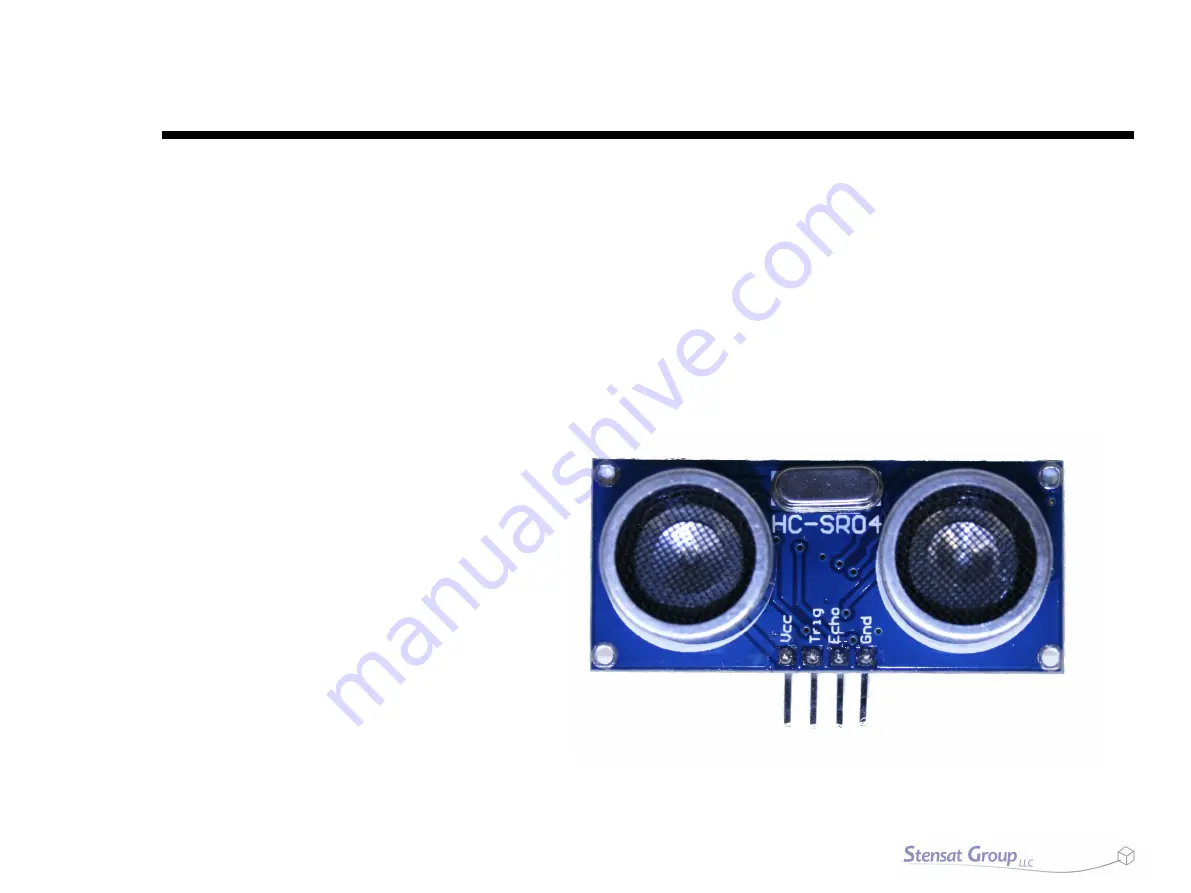
65
Sensing the Environment
●
To detect things in the environment for purpose of collision avoidance, an
ultrasonic range sensor will be added to the robot.
●
This sensor sends out a burst of audio signal at 40 Khz and detects the
echo.
●
The processor needs to measure the time it takes for the echo to return.
●
This sensor has four pins
●
Ground
●
5 Volt power input
●
Trigger
●
Echo
Summary of Contents for Sten-Bot Robot Kit
Page 1: ...Sten Bot Robot Kit Stensat Group LLC Copyright 2013 ...
Page 5: ...5 Tools Needed Philips screw driver 1 4 inch nut driver Jeweler blade screw driver ...
Page 30: ...30 Wiring Diagram for LED LED Resistor Long lead ...
Page 33: ...33 LED Connected to Port 3 Digital Pin D3 ...
Page 48: ...48 Motor Controller Wiring Diagram ...
Page 50: ...50 Wiring Diagram for Motors Left Motor Right Motor ...