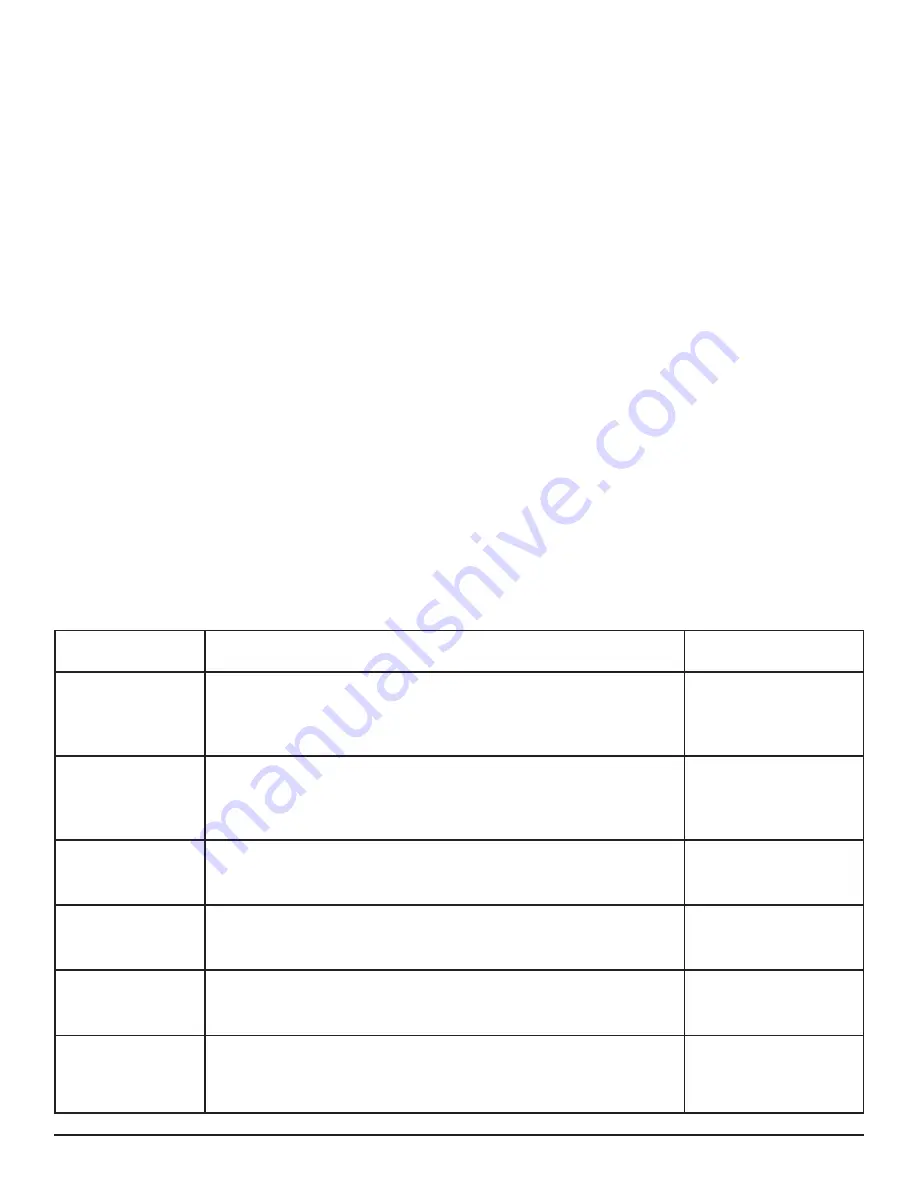
T
herm
e
lecT
h
ydronic
S
afeTy
i
nformaTion
SAFETY PRECAUTIONS
1. Fully assemble the system and load ceramic heat storage brick prior to energizing the system.
2. Pressure relief valve must be installed prior to operation of the system.
3.
Use or storage of explosive or flammable gases or liquids within close proximity of the system presents
a hazard.
4.
Clearance requirements are critical to safe operation of the system. Follow all requirements specified
in this manual (page 3.03).
5. Keep the top of system clear.
6. Ensure openings for ventilation to the heat sink are clear and unobstructed.
7. Use caution when working around the heating system as inlet and outlet piping can be very hot.
8. De-energize all branch circuits before servicing. This heating system may be connected to more than
one branch circuit.
9.
Installation of and/or service to this heating system should be performed by a qualified technician
in accordance with information contained herein and with national, state, and local codes and
requirements.
10. Repeated error codes on the system display (pages A.10 – A.12) indicate a need for service by a
qualified technician.
11. Special requirements must be considered if placing the system in a garage or other area where
combustible vapors may be present. Consult local, state and national codes and regulations to ensure
proper installation.
BUILT-IN SAFETY DEVICES
The ThermElect Hydronic heating system incorporates safety devices to ensure normal operating temperatures
are maintained. The chart below describes these safety devices.
DEVICE NAME
FUNCTION
LOCATION
ON SYSTEM
Core Charging
High Limit
Switches
(Auto Reset)
These limit switches monitor the core and top temperatures. If
normal operating temperatures are exceeded, the system will
display "CORE FAIL" and the elements will not be allowed to
operate.
Right side and top of
the system.
Heat Exchanger
Limit Switch
(Manual Reset)
This linear limit switch monitors the temperature of the water in
the exchanger and interrupts power to the core blower if a water
temperature of 250
o
F/121
o
C is exceeded. If this limit switch opens,
contact a qualified service technician.
Behind front lower
painted panel. Reset
button visible in lower
right front corner.
Outlet Water
Temperature Limit
Switch (Auto Reset)
This linear limit switch monitors the temperature of the water in
the exchanger and interrupts power to the core blower if a water
temperature of 225
o
F/107
o
C is exceeded.
Behind front lower
painted panel.
Pressure Relief
Valve
If the water pressure exceeds maximum psig, the pressure relief
valve opens. Once water pressure of less than maximum psig is
achieved, the valve closes.
Factory provided, field
installed to outlet of
heat exchanger.
Definite Purpose
Contractors
If one or more of the core charging high limits open, the definite
purpose contactors will interrupt power to the heating elements
until the core limit closes.
Inside the Electrical
Panel.
Heat Sink High
Limit Switches
(Auto Reset)
These limit switches monitor the heat sink temperature for
abnormal temperature rise. If the temperature of the heat sink is
too high, the limits open and remove power from the SSR’s causing
the elements to turn off.
Inside the Electrical
Panel.