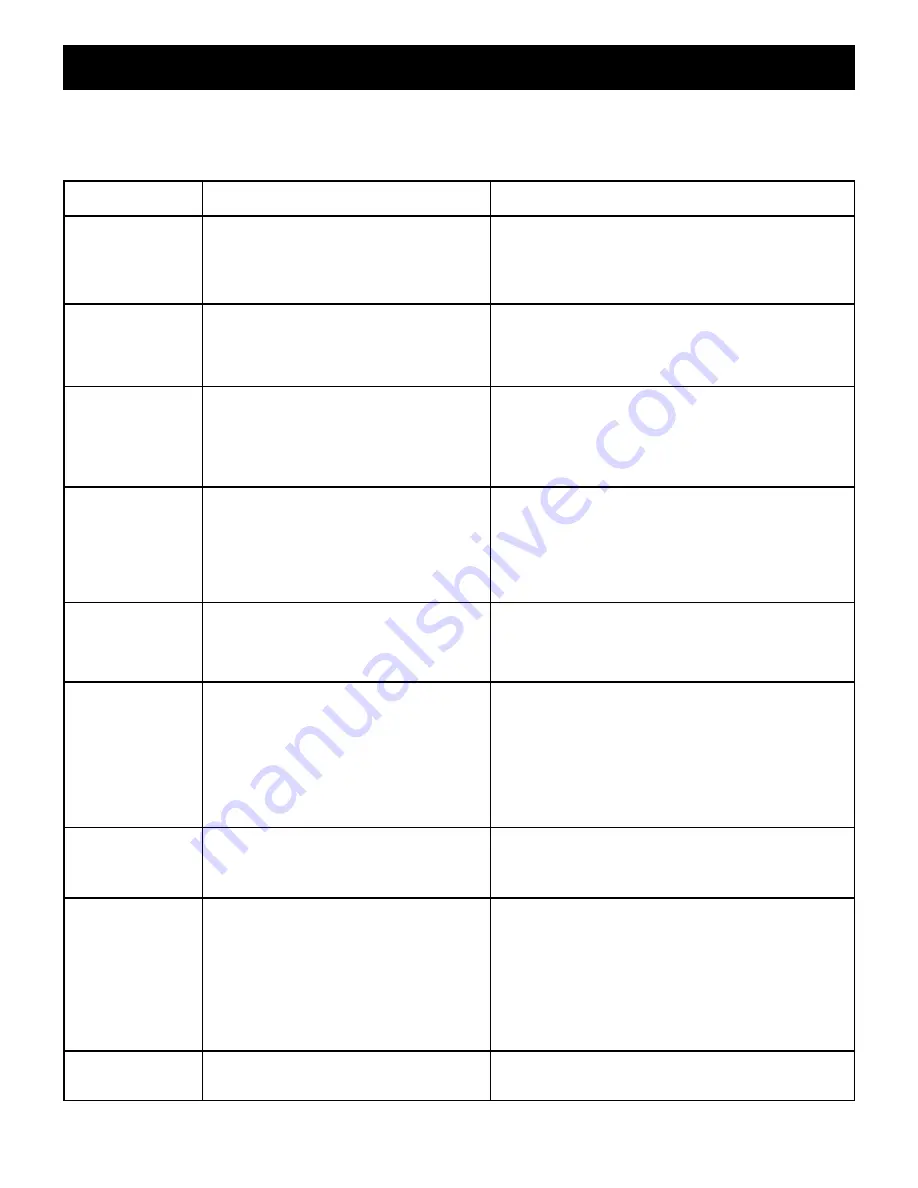
30
TROUBLESHOOTING GUIDE
This section covers the most common processing problems encountered in sawing and what to do about them.
Do not make any adjustments until the table saw is unplugged from the power source and moving parts have come
to a complete stop.
PROBLEM
LIKELY CAUSE(S)
SOLUTION
1. Overload tripped.
1. Allow motor to cool and reset by pushing off switch.
2. Saw unplugged from wall or motor.
2. Check all plug connections.
3. Fuse blown or circuit breaker tripped.
3. Replace fuse or reset circuit breaker.
4. Cord damaged.
4. Replace cord.
1. Stops not adjusted correctly.
1. Check blade with square and adjust stops.
2. Angle pointer not set accurately.
2. Check blade with square and adjust pointer.
3. Miter gauge out of adjustment.
3. Adjust miter gauge.
1. Fence not aligned with blade.
1. Check and adjust fence.
2. Warped wood.
2. Select another piece of wood.
3. Excessive feed rate.
3. Reduce feed rate.
4. Splitter not aligned with blade.
4. Align splitter with blade.
1. Dull blade.
1. Sharpen or replace blade.
2. Blade mounted backwards.
2. Properly mount blade.
3. Gum or pitch on blade.
3. Remove blade and clean.
4. Incorrect blade for cut.
4. Change blade to correct type.
5. Gum or pitch on table.
5. Clean table.
1. Extension cord too light or too long.
1. Replace with adequate size cord.
2. Low shop voltage.
2. Contact your local electric company.
3. Motor not wired for correct voltage.
3. Refer to motor junction box.
1. Stand on uneven floor.
1. Reposition on flat, level surface.
2. Damaged saw blade.
2. Replace saw blade.
3. Bad V-belts.
3. Replace V-belts.
4. Bent pulley.
4. Replace pulley.
5. Improper motor mounting.
5. Check and adjust motor.
6. Loose hardware.
6. Tighten hardware.
7. Loose set screw in pulley.
7. Tighten set screw.
1. Guide rails or extension wing not installed
1. Reassemble guide rails, refer to fence manual.
correctly.
2. Guide of rip fence not adjusted properly.
2. Adjust guides, refer to fence manual.
1. Rip fence out of alignment.
1. Align rip fence with miter slot and blade.
2. Splitter not aligned with blade.
2. Align splitter with blade.
3. Feeding stock without rip fence.
3. Install and use rip fence.
4. Splitter not in place.
4. Install and use splitter (with guard).
5. Dull blade.
5. Replace blade.
6. Letting go of material before it is past blade.
6. Push material all the way past blade before releasing work.
7. Anti-kickback fingers dull.
7. Replace or sharpen anti-kickback fingers.
1. Sawdust and debris in raising and tilting
1. Clean and grease.
mechanisms.
Saw stops or
will not start.
Does not make
accurate 45° or 90°
cuts.
Material binds blade
when ripping.
Saw makes
unsatisfactory
cuts.
Blade does not
come up to speed.
Saw vibrates
excessively.
Rip fence binds
on guide rails.
Material kicked back
from blade.
Blade does not raise
or tilt freely.
Summary of Contents for 35635
Page 18: ...18 G Left and Right Extension Wings H Blade Guard Assembly G H...
Page 31: ...31 u NOTES u...
Page 32: ...32 PARTS...
Page 34: ...34...
Page 36: ...36...
Page 38: ...38...
Page 40: ......