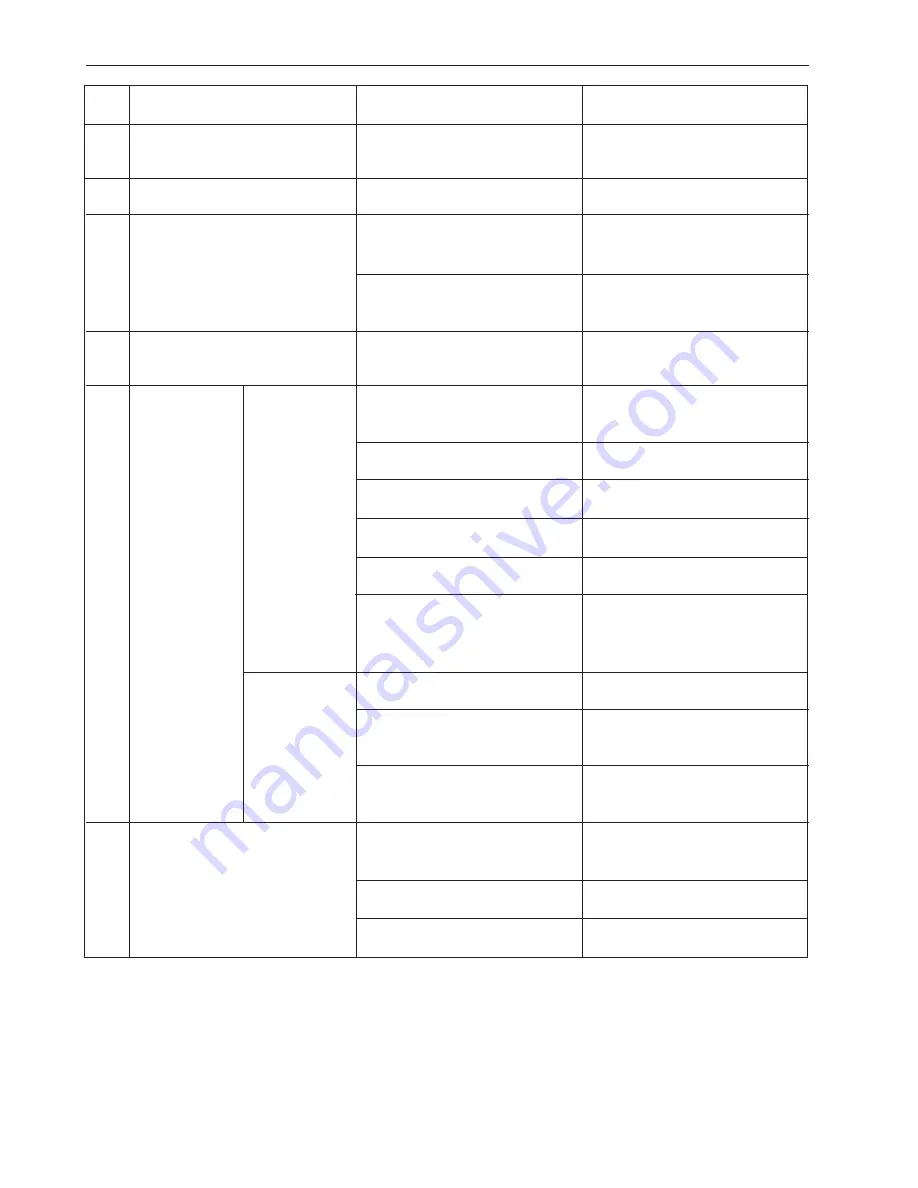
STEALTH DIGI-TIG 320 AC/DC PULSE
29
S/N
PROBLEM REASON
SOLUTION
3
Turn on the power source, lamp No power input
Check if there is power supply
is not on and fan doesn’t work Inside machine fuse damaged Change fuse (3A)
4
Display number not clear
LED is broken
Change LED
Max value is not accordant
Adjust potentiometer lmin on
(refer to 3.1)
power board
5
Max and min value displayed
does not accord with set value
Min value is not accordant
Adjust potentiometer lmax in
(refer to 3.1)
current meter
6
No no-load voltage output
Machine is damaged
Check main circuit and Pr4
(MMA)
Welding cable is not connected Connect welding cable to
with two output of welder
welder’s output
Welding cable damaged
Repair or change
Earth cable connection unstable Check earth cable connection
Welding cable is too long
Use appropriate welding cable
Oil or dust on the workpiece
Check and remove
7
Distance between tungsten
Reduce distance to approx
electrode and workpiece too
long
3mm
HF ignition board does not work Repair or change Pr8
Distance between charger too
Adjust distance to approx
short
0.7mm
Welding gun switch
Check welding gun switch,
malfunction
control and aero socket
Gas cyliner is close or pressure
too low
Open or change gas cylinder
8
No gas flow (TIG)
Blockage in valve
Remove blockage
Electromagnetic valve damaged Change valve
Spark on HF
igniting board
Arc cannot be
ignited (TIG)
No spark on
HF igniting
board