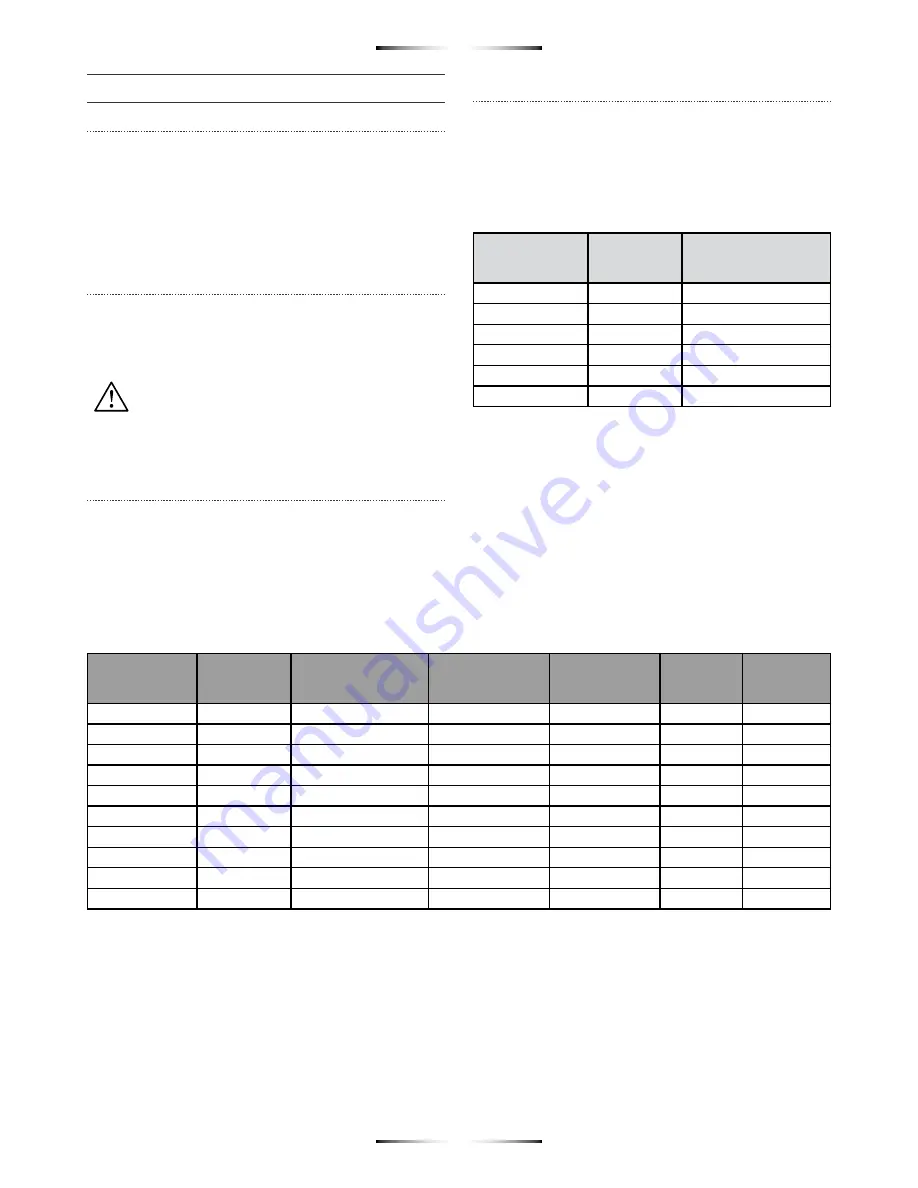
ENGLISH
34
34
4.- OPERATING INSTRUCTIONS
4.1.- Positioning and testing
All Steyer Welding machines of the series must be handled
using the handle which is arranged for transport.
A fee space of at least 15cm must be arranged around the
equipment, and free circulation of air must be secured for
correct heat dissipation. Before each work, good operation and
correct tightening of all external elements of the equipment shall
be verified: power supply plug, cable, housing structure and
connection terminals and switches.
4.2.- Tool changing
All Steyer Welding machines of the series have a 1/2 inch DINSE
quick connector for the welding cables. To remove or put the
connector on, it is sufficient to turn the connector a quarter turn
leftward or rightward.
WARNING:
Always connect the DINSE connector as
far as it will go and make sure that the splice with the
cable is in a good condition and that the contact surface
is clean. A bad splice or a dirty connection will result in a bad
performance and make the front panel to become overheated,
fused or burnt.
4.3.- Setting operations
All Steyer Welding machines contain a complex electronic system
and come completely calibrated ex works, so that, for the sake
of efficiency and safety, it is not authorized to be manipulated by
the user. In case of any doubt regarding a malfunction, contact
your distributor or our helpdesk system.
4.4.- Limits regarding the size of the workpiece
The main restriction regarding the size of the workpiece is its
thickness which is limited by the power of the equipment. With
more power, you may carry out accurate welds (with suitable
penetration of the welding bead) in pieces having a higher
thickness. The following table may serve you as an orientation:
SHIELDED ELECTRODE WELDING
Thickness of
the piece to be
welded
E6013
electrode
diameter
Amperage setting
range
1 a 2 mm
1,6 mm
30 – 60
1,5 a 3 mm
2,0 mm
50 – 70
2,5 a 5 mm
2,5 mm
60 – 100
5 a 8 mm
3,2 mm
85 - 140
8 a 12 mm
4,0 mm
120 – 190
More than 12 mm
5,0 mm
180 – 240
ALUMINIUM WELDING
Thickness of
the piece to be
welded
Tungsten
electrode
diameter
Filler rod diameter
Amperage setting
range
Argon gas flux
Joint size
Joint shape
mm
mm
mm
A
l/min
mm
0.6
1.0 - 1.6
0 - 1.0
25 - 40
4 - 5
1
a.b
1.0
1.0 - 1.6
0 - 1.6
40 - 60
4 - 7
1
a.b
1.5
1.0 - 1.6
0 - 1.6
60 - 90
6 - 9
1
b
2.5
1.6 - 2.4
1.6 - 2.4
80 - 120
6 - 9
1
b
3.0
1.6 - 2.4
1.6 - 2.4
100 - 160
7 - 10
1 - 2
b.c
4.0
2.4
1.6 - 2.4
130 - 200
10 - 15
2 - 3
c.d
5.0
2.4 - 3.2
2.4 - 3.2
150 - 250
10 - 15
2 - 3
c.d
6.0
2.4 - 3.2
2.4 - 3.2
200 - 280
10 - 15
3 - 4
c.d
8.0
3.2 - 4.0
3.2 - 4.0
200 - 300
12 - 18
4 - 5
d
Summary of Contents for S60.17L
Page 2: ...2 2 Fig 1 S60 17L Fig 2 T100 20H TIG DC 200 HF 1 2 3 4 5 1 2 3 4 6 7 5 10 8 5...
Page 4: ...4 4 Fig 5 PANEL CONTROL T100 25PAHT Fig 6 PANEL CONTROL T40 20PAH...
Page 5: ...5 5 Fig 7 Conexiones de S60 17L TIG LIFT ARC electrodo negativo polaridad directa...
Page 6: ...6 6 Fig 8 Conexiones para soldadura convencional electrodo positivo polaridad inversa S60 17L...
Page 49: ...49 49 NOTAS...
Page 50: ...50 50 NOTAS...
Page 51: ...51 51 NOTAS...