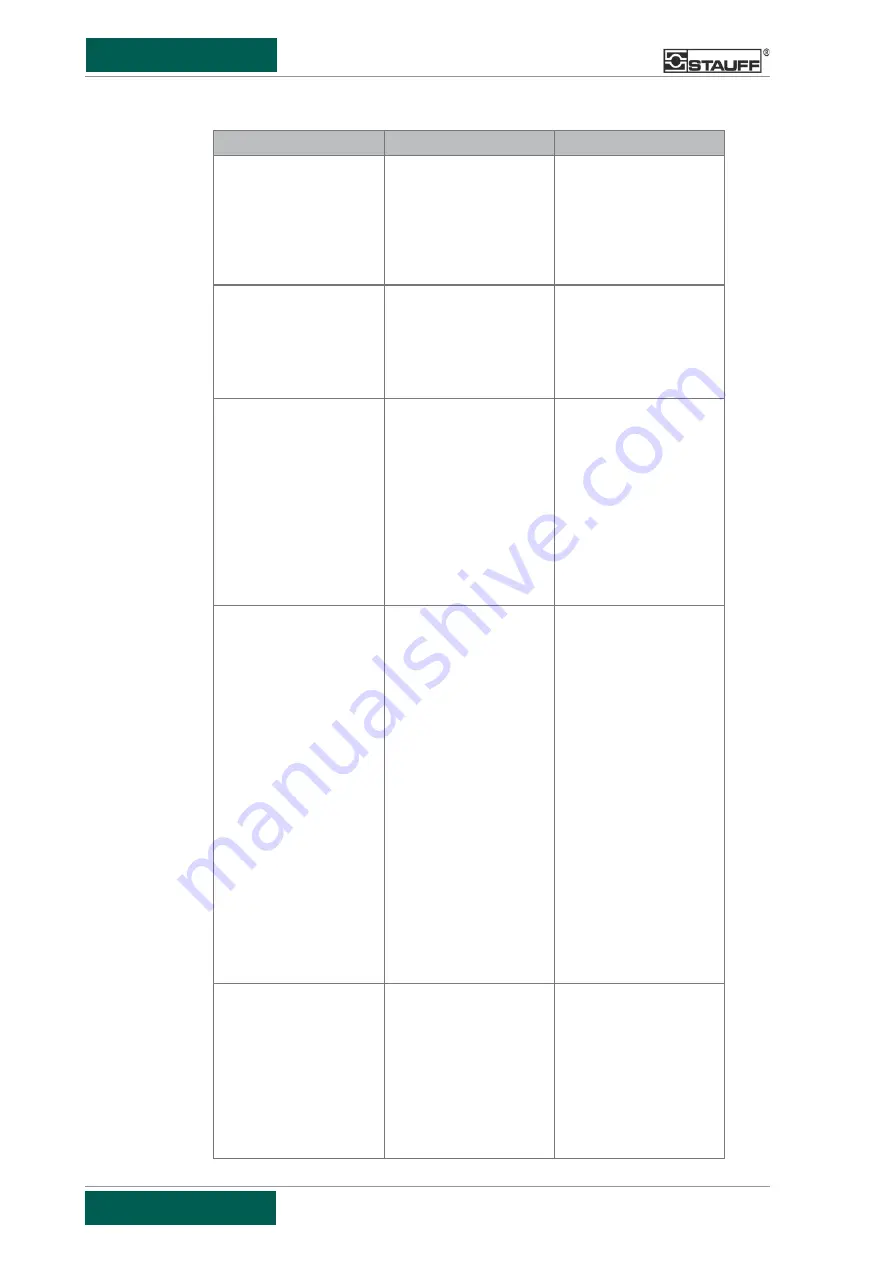
Mobile filter system
26 / 32
8 Malfunctions
8.3 Malfunctions table
Malfunction
Possible cause
Elimination
Motor does not start
• Power supply
interrupted
• Motor defective
• Plug the plug into the
socket
• Check the fuses
• Turn the electrical main
switch
• Check/replace the
motor
Motor protection switch
triggered
• Continuous operation
at high ambient
temperatures
• Use of media with
impermissibly high
viscosity
• Leave to cool down for
10
– 15 minutes
• Check whether the
viscosity of the oil used
is permissible
Pump does not run
smoothly/produces noise
• Medium highly
contaminated
• Shaft bearing damaged
• Check pre-filter and
clean if necessary
• Check motor direction
of rotation and swap
the phases in the plug
if necessary (CEE plug
equipped with phase
inverter)
• Send pump to factory
customer service for
repair
Flow rate is too low
• Filter elements not yet
filled
• Intake line blocked
• Pre-filter blocked
• Pressure loss from leak
• Filter elements blocked
• Hoses kinked
• Pump defective
• Medium cold or with
impermissibly high
viscosity
• Wait 30 – 60 seconds
• Clear the blockage
• Cleaning the pre-filter
• Identify the leak and
eliminate properly
• Check the
contamination
indicator, replace filter
elements if necessary
• Eliminate the cause
• Send pump to factory
customer service for
repair
• Use coarser filter
elements if necessary
• Check whether the
viscosity of the oil used
is permissible
Contamination indicator in
the red zone
• Filter elements blocked
• Medium cold or with
impermissibly high
viscosity
• Replace the filter
elements
• Check again after 20 –
30 minutes, use
coarser filter elements
if necessary
• Check whether the
viscosity of the oil used
is permissible