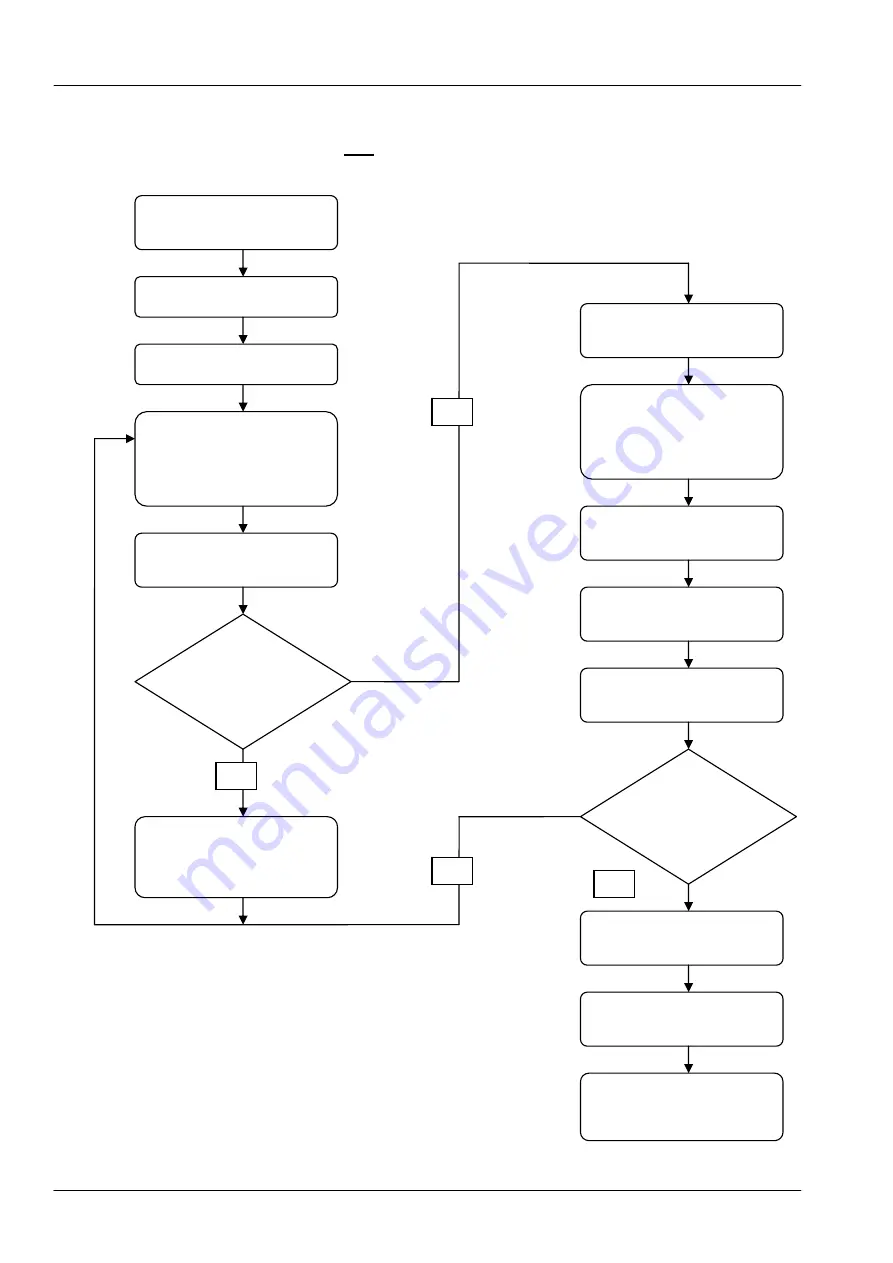
Midilift XLplus
Maintenance Guide
Jan
2014
Issue
4
32
17.3 Overspeed governor activation tests – for contracts without remote test control OSG activation
button only (see 17.2 for contracts with remote OSG activation) .
At the upper landing control
station, place shorting link
between
G1
and
G1A
terminals.
At the upper landing control
station, push in speed tab to
select half speed control
(Inverter screen should read
25Hz
).
Has the motor
stopped and
G2
supply been
lost?
Place shorting link between
G2
and
G2A
terminals.
At the upper landing control
station, push in speed tab to
select half speed control
(Inverter screen should read
25Hz
).
Reset OSG by running lift in
opposite direction.
Remove shorting link between
G2
and
G2A
terminals.
Has process
been repeated
in up direction?
Pull out speed tab to select full
speed control (Inverter screen
should read
50Hz
).
Remove shorting link between
G1
and
G1A
terminals.
Position lift car 1 M below floor
level.
Refer to and complete section
‘
17.4 Overspeed Lift
’
Select half speed control and
run lift in opposite direction to
reset OSG. Check for correct
OSG setup.
N
Refer to and complete section
’
17.5 Re set lift to run at 50Hz
’.
Remove rope from test groove
and return to normal service –
see section ’
17.4 Overspeed
Lift
’.
Y
Y
N
Run lift in down direction and
activate the OSG by switching to
full speed (pull out speed tab).