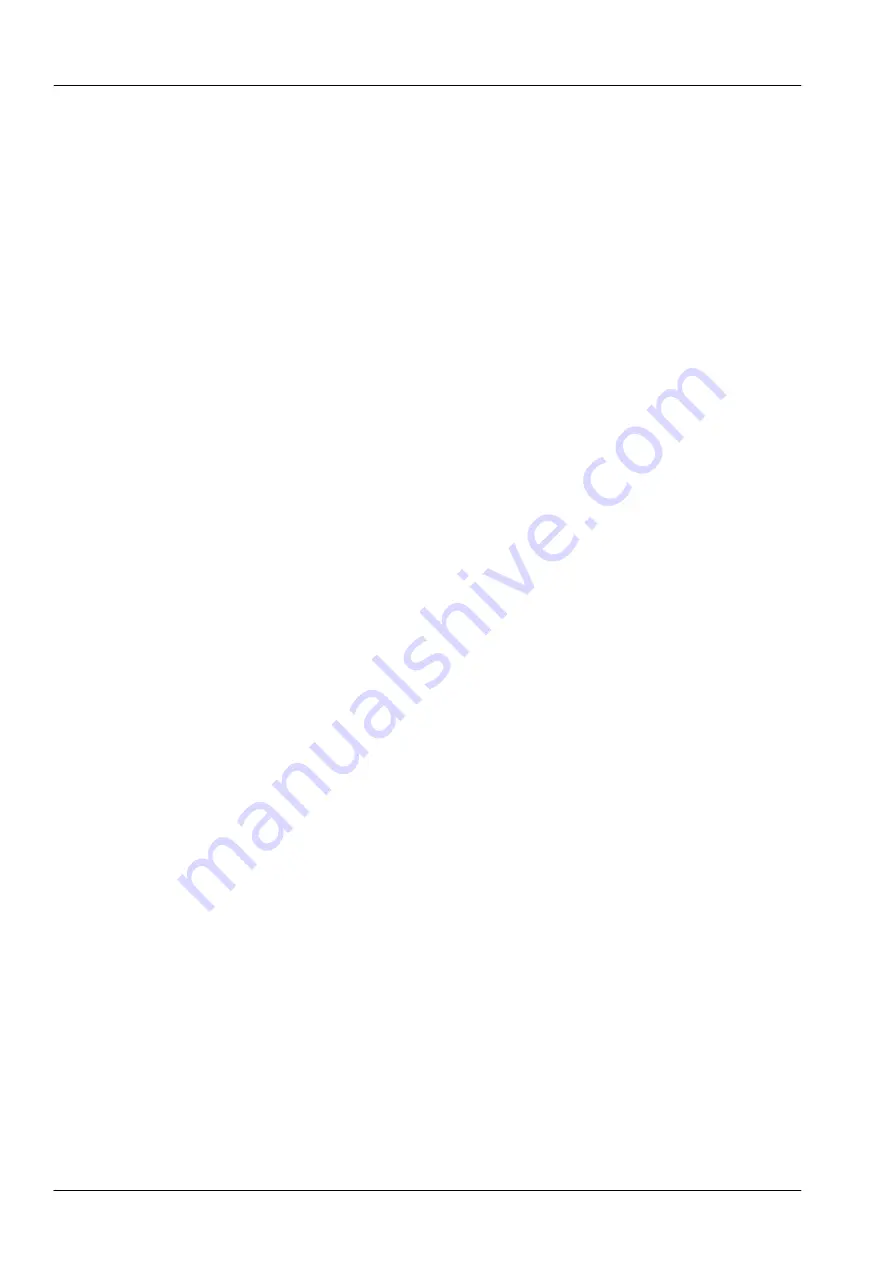
Midilift XLplus
Maintenance Guide
Jan
2014
Issue
4
16
11.3 Drive shaft bearings
•
Required
standard
Important note: Persons are not permitted to stand on the car roof.
Access to the upper shaft work is gained
by removing the cabin (
4.4 Ceiling removed, pg 5
)
The main drive shaft support bearings (2 off), located on the bedplate at the top of the shaft, need to be checked
for re-lubrication. The bearings are considered to be lubricated for life, but due to differing operating conditions
(temperature, vibration, loads etc) they need to be checked to ensure the moving elements of the bearing are
lubricated. Firstly, check for excessive noise and vibration while running the lift (remove the motor access panel,
located in the upper landing controller, for a clearer examination of the noise). Also, assess the bearings for
general wear/degradation and check for excessive grease seeping out around the bearing seals (a small amount is
acceptable and will not require attention).
Note: Do not attempt to tighten the bearing collar fixings. Attempts to tighten the fixings could result in
deformation of the collar. If it is suspected that the shaft has moved in the bearings, first check that the
fixings securing the bearing housings to the bedplate are secure. Following this, technical assistance
should be sought due to the specific procedure required to refit the bearings to the shaft.
•
Required
action
If it is determined that the bearings need relubricating, isolate the power to the lift and gain access to the upper
shaftwork (
4.4 Ceiling removed, pg 5
). Using a grease gun and SKF LGWA 2, LGMT 2, LGMT 3 or equivalent
grade grease, slowly press in the lubricant into the bearing via the grease nipple located on top of each housing. A
flexible extension hose may be required to access the grease nipples (dependant on headroom). Stop pressing the
grease into the bearing as soon as fresh grease starts escaping out of the seal. Avoid excess pressure as this can
damage the seals.
If the remedial work cannot be completed, or the bearings need replacing, inform the customer and supervisor that
the lift will need to be taken out of service immediately and advise on the work required.
11.4 Ultimate limit switch
•
Required
standard
The ultimate limit is located on the lift sling. Call the lift up to upper landing using upper landing call station and on
arrival of lift remove COP and rear walls (
4.5 COP and rear wall removed, pg 5
).
Using the push-pull switch located on the din rail assembly within the upper control unit, switch the lift to slow
speed by pushing the switch in. Use the test control (
4.3 Upper floor landing controls, pg 4)
to operate the lift
upwards at slow speed. Lift should stop before clashing with bedplate at approximately 50mm above floor level.
When the lift has come to a halt, use the test controls to operate the lift downwards, the lift should not move as the
ultimate limit switch will be engaged.
To move the lift downwards, link out G2A to G3 on the controller. Once the ultimate limit pin has moved away from
the ultimate limit ramp, reset switch ‘A’ and remove link from G2A to G3 (
Figure 2 - Ultimate limit switch
).
•
Required
action
If lift comes to a halt before the ultimate limit stops the lift, look the following areas.
-
If the counterweight is coming to rest on the buffer before the switch activate, check rope stretch (
10.4
Rope connections and wear/stretch, pg 14
).
-
If the sling clashes with the bedplate before the switch activates. Check the position of the ultimate limit
ramp.
- If the switch pin is activating but not cutting power to the motor, check wiring and carry out any
immediate remedial work.