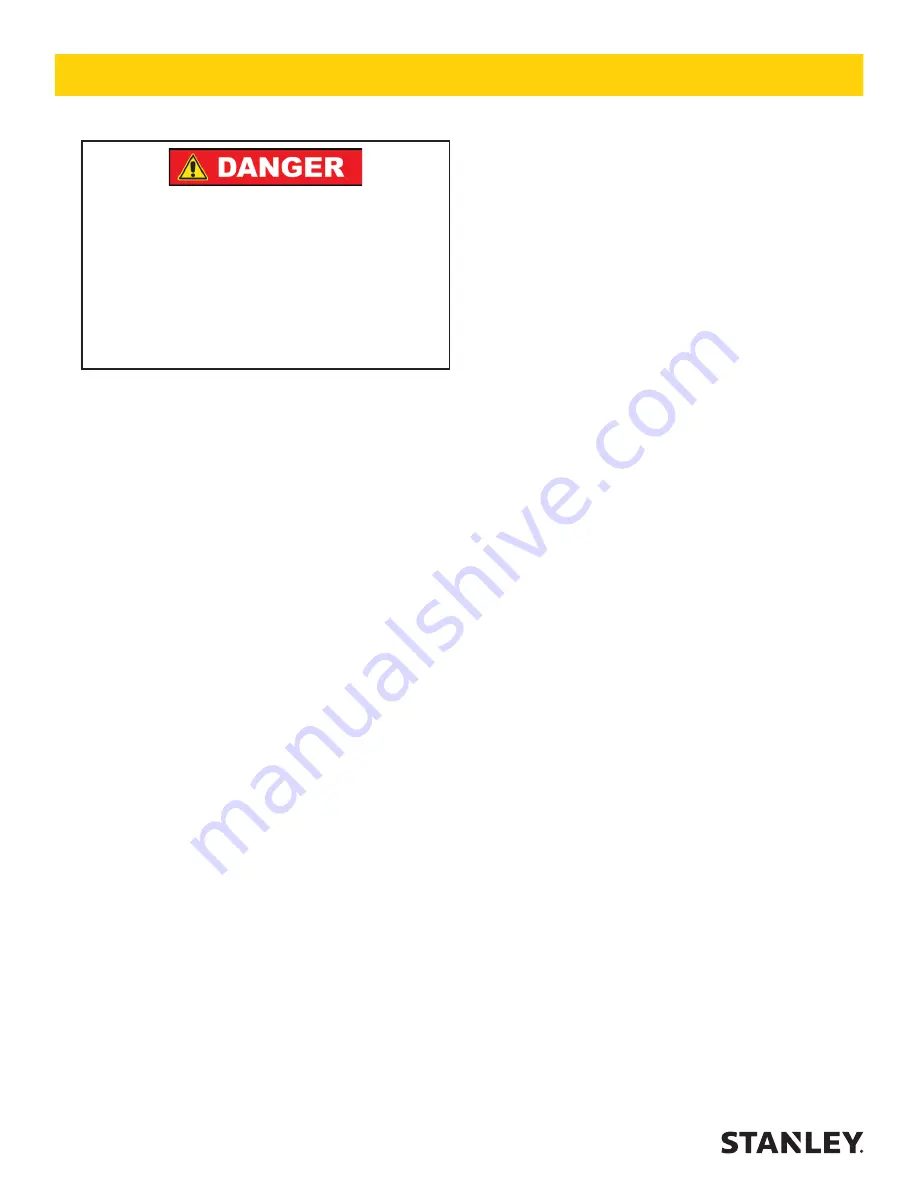
18 ► MHP3
User Manual
2.
Loading and unloading of any type of machine is
dangerous. Never attempt to load or unload the
machine without loading ramps or a loading dock.
Loading ramps must be strong enough, have a low
angle, and correct height. Load and unload the
machine on a level surface. Never attempt to load
or unload the machine if the ramp incline exceeds
15 degrees. Failure to follow these instructions may
result in serious injury or death.
Ensure the wheels of the trailer and the tow vehicle
have been chocked front and rear.
3. Use the
SLOW
throttle setting when loading or
unloading. Always switch the two-speed control to
LOW
speed operation when moving in reverse.
4. Drive the machine onto the trailer backwards (en-
gine first). This will help prevent instability and keeps
the operator “up hill” from the machine during load-
ing and unloading.
5. After loading, place chocks at the front and rear of
the tracks.
LIFTING
The unloaded TracHorse can be lifted using the single
central lift point. Some safety rules may require 3-point
lifting. (Center lift point plus 2-points on forward side of
rails.)
If lifting with any items in the bed, a 3-point lift is re-
quired. (A 3-point lifting sling is available, refer to Acces-
sories page.)
TRANSPORTING
1. Read the instructions for loading and unloading in
this section.
2. Use chains and binders to secure the load to the
trailer.
ROUTINE MAINTENANCE
Good maintenance practices will keep the machine on
the job and increase its service life.
A very important maintenance practice is to keep the hy-
draulic fluid clean at all times. Contaminated hydraulic
fluid causes rapid wear and/or failure of internal parts.
Follow the maintenance instructions contained in the en-
gine manual.
ENGINE MAINTENANCE
Follow the maintenance schedule and general mainte-
nance instructions in the engine maintenance and op-
eration manual furnished with the power unit. Normal
maintenance includes:
•
Service foam air pre-cleaner every 25 hours of op-
eration.
•
Service air paper cartridge every 100 hours of op-
eration.
• Replace in-line fuel filter every 100-300 hours or
sooner if required.
•
Replace spark plugs every 100 hours of operation.
• Change engine oil after first 5 hours of operation,
then after every 50 hours of operation. If engine has
been operating under heavy load or in high ambi-
ent temperature, change the oil every 25 hours of
operation.
• Change oil filter when engine oil is changed.
•
Check oil level daily.
•
Remove dirt and debris from engine with a cloth or
brush daily. Do not use water spray.
•
Clean air cooling system every 100 hours of opera-
tion.
HYDRAULIC SYSTEM
MAINTENANCE
Observe the following for maximum performance and
service life from the hydraulic system.
• Always keep hydraulic system and fluids clean.
• Keep water out of fluid. (See paragraph below.)
•
Keep air out of hydraulic lines. Hydraulic system
overheating and foam at the hydraulic tank breather
indicate air is present in the lines. Keep all suction
line fittings and clamps tight.
•
Hydraulic system wear is noted by increased heat
during tool operation, reduced tool performance and
eventual system breakdown.
• Operate with the fluid temperature at 50–140 °F/
10–60 °C for improved seal and hose life, and maxi
-
mum efficiency.
OPERATION
Summary of Contents for MHP3
Page 2: ...2 MHP3 User Manual NOTES...
Page 25: ...MHP3 User Manual 25 HOSE FITTING ILLUSTRATION MHP3 PARTS ILLUSTRATION...
Page 31: ......