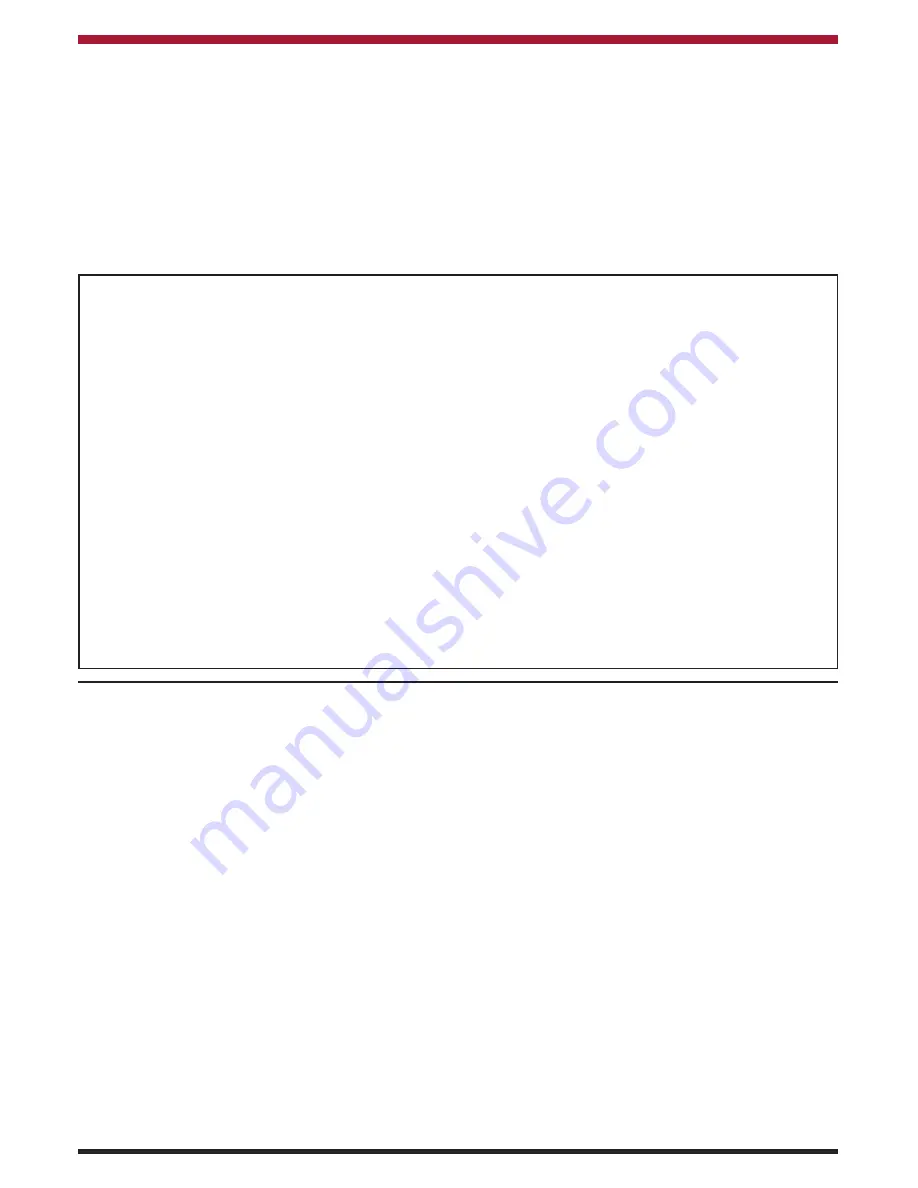
INSTALLATION
As manufacturers and suppliers of cooking and heating appliances, we take every possible care to ensure as
reasonably practicable that these appliances are so designed and constructed as to meet the general safety
requirements when properly used and installed.
The installation must comply with the following:
*
B.S. 5410 Oil Installation Part 1 under 45 kW
*
The Building Regulations Part J Ireland, England and Wales, Part F section III Scotland, Part L
Northern Ireland.
*
The Control of Pollution (oil) Regulations.
*
B.S. 5449 Forced Circulation Hot Water Central Heating System for Domestic Installation.
*
Health & Safety at Work Act.
*
B.S. 7671 Requirement for Electrical Regulations.
*
Safety Document 635 : The Electricity at Work Regulations.
*
B.S. 7593: Treatment of Water in Domestic Hot Water Systems.
*
B.S. 7074: Part 1 & 2 Hot Water Supply.
*
B.S. 4814: Sealed Systems.
IMPORTANT NOTICE:
Any alteration to this appliance that is not approved in writing by Waterford Stanley,
will render the guarantee void.
LOCATION
When choosing a location for this appliance you
must have:
a)
Sufficient room for the installation (see
clearances) a satisfactory flue (see chim-
neys) and an adequate air supply for cor-
rect combustion and operation.
b)
Adequate space for maintenance and air
circulation.
HEARTH CONSTRUCTION
When a non-combustible floor surface is not avail-
able then we recommend that the cooker be placed
on a slab of formed concrete 40mm (1 1/2”) deep or
a slab of other insulating material. This hearth must
extend 225mm (9”) to the front and 150mm (6”) to
either side of the appliance.
ELECTRICAL SUPPLY
All wiring external to the appliance must conform to
the current B.S. 7671, B.S. 7462, Safety Document
635, ETC Part 1 section 5.4.6 and the Electricity at
Work Regulations. The cooker requires 230V -
240V, 50Hz supply. Connection of the appliance
and any system controls to the mains supply must
be through moulded-on plug top with a 5 amp fuse,
which is fitted to the appliance in accordance with
E.N. 60335, Consumer Protection S.I. 1996 No.
1768, plug and sockets etc.. Safety Regulations
1994.
Always install in accordance with current local
wiring regulations.
WARNING: THIS SUPPLY MUST BE EARTHED
(Refer to B.S. 7430 code of Practice for Earthing)
Where a risk of low voltage can occur, a voltage sen-
sitive device should be fitted to prevent start up of
the burner so as not to endanger the installation.
The appliance must be positioned so that the
plug is accessible.
6
TECHNICAL DATA
THIS COOKER IS SUITABLE FOR HOMES UP TO 1,100 sq. ft. = 102 sq meters.
Cooker Output:
At 1.8 kg = 2.08 Litres Kerosene/Hour
Gross Output:
20 kW = 69,000 Btu’s/Hr
Net to Water:
13.7 kW = 47,000 Btu’s/Hr (Max.)
Jet:
60 Degree Solid Pattern (0.60 U.S. gallons)
Oil Pressure:
8.16 Atmosphere = (120 p.s.i)
Radiation Surface:
Heating Surface only 22.2 sq. meters = 240 sq.ft.
Heating and Domestic Hot Water 19.4 sq. meters = 210 sq. ft.