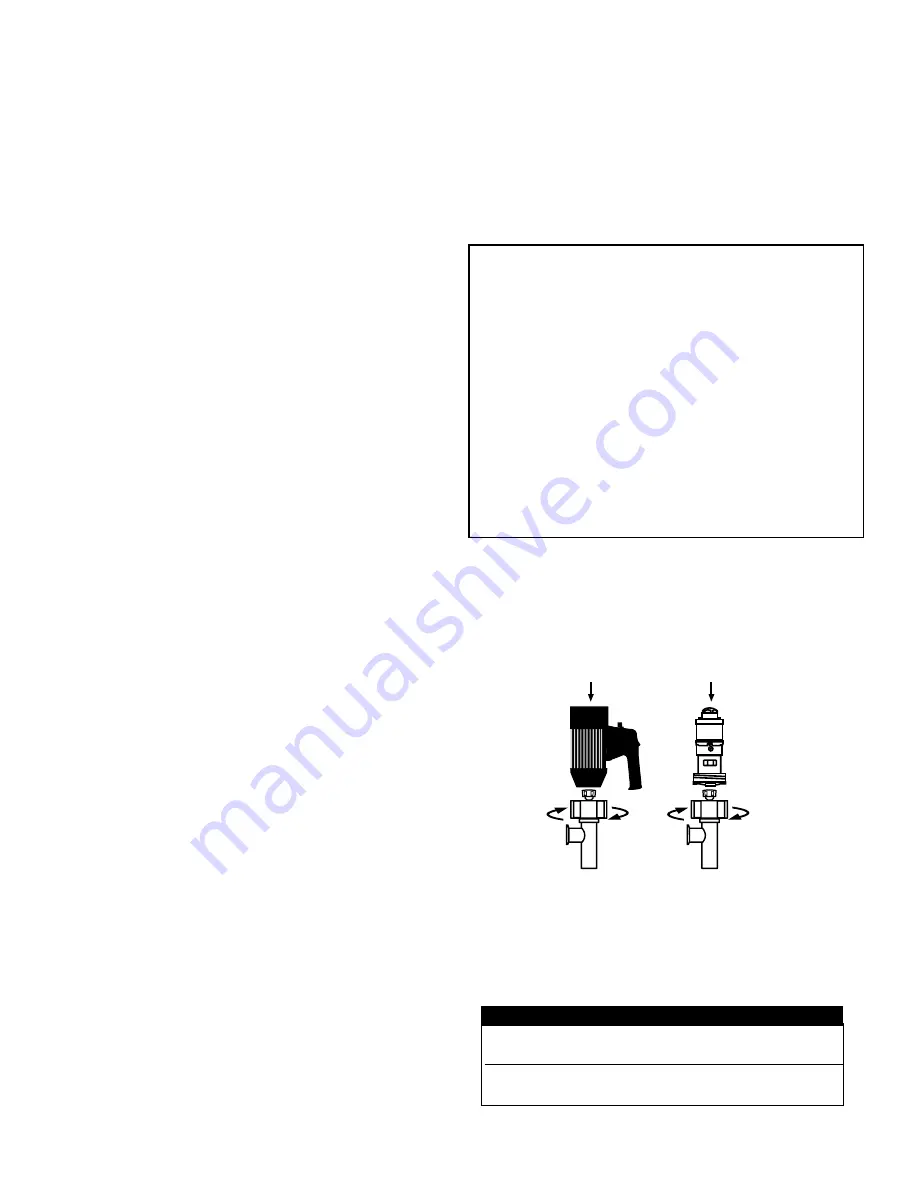
2
Standard Pump Operating Instructions and Parts Manual (OIPMS0611)
Standard Pump Operating Instructions and Parts Manual (OIPMS0611)
Description
Standard’s Drum Pumps are designed to transfer a variety of
materials from 55 gallon drums and tanks . Standard Pump
offers several different pumps, each designed for specific
applications. Before operating, please confirm that the pump’s
materials of construction are suitable for the application.
Unpacking
Cartons should be handled with care to avoid damage from
dropping, etc . After unpacking, inspect carefully for any
damage that may have occurred during transit. Check for
loose, damaged or missing parts .
General Safety Information
The responsibility for safe assembly, installation, and operation
ultimately rests with the operator. Read and understand ALL
safety precautions and operating instructions before operation .
Careless pump operation can result in serious injury .
1. Before operating the pump, read and understand these
operating instructions .
2. The operator should wear suitable protective clothing
including the following: face mask, safety shield or
goggles, gloves, apron, and safety shoes.
3. Before operating, verify the materials being pumped are
compatible with the pump’s “wetted components.”
4. All Federal, State, and local safety codes should be
followed .
5. Verify that the motor voltage corresponds to proper
electrical supply .
6. Before plugging motor into power supply, make sure the
motor switch is in the OFF position.
7 . Before operation, confirm all pump connections are
properly tightened.
8. First pump clean water in order to familiarize yourself with
the pump’s operation, flow rate, discharge pressure and
motor speed .
9. Before starting the pump, confirm the discharge hose is
securely fastened to the receiving vessel in order to prevent
splashing.
10 . Never leave pump unattended during operation .
11. Do not submerge the motor in any liquid.
12. When finished using the pump, flush the pump by
pumping water or an appropriate cleaning solution . Do not
use flammable or combustible cleaning solutions .
13. Never carry the motor by the power cord.
Assembly
1. Remove the pump and motor from packaging.
2 . Inspect all contents for damage .
3. Couple the motor to the pump tube by using the Hex Nut
(see Figure 1) .
4. It is recommended to thoroughly clean and sanitize models
SP-8100 & SP-8200 before operation .
5. First pump clean water in order to familiarize yourself with
the pump’s operation, flow rate, discharge pressure and
motor speed .
Standard Pump
Sanitary Pump Models:
SP-8100, SP-8200, SP-8800, SP-8900, SP-800SR & SP-800DD
SP-8100 & SP-8200 SERIES
Note:
Flow rates are based on water. As viscosity increases, the flow
rate will decrease .
Specifications
Models SP-8100 & SP-8200
Maximum Liquid
Temperature . . . . . . . . . . . . . . . . . . . .175º
F (79
º C)
Pump Type . . . . . . . . . . . . . . . . . . . . . . .Centrifugal
Pump Speed . . . . . . . . . . . . . . . . . . . . .10,000 RPM
Max. Flow Rate
SP-8100
. . . . . . . . . . . . . . . . . . 32 GPM (121 LPM)
SP-8200 . . . . . . . . . . . . . . . . . . . . 15 GPM (57 LPM)
Max. Discharge Pressure SP-8100
. . . . . . . . . . . . . . . . . . . . . . . . 16 psi (1,1 bar)
SP-8200 . . . . . . . . . . . . . . . . . . . . . . . . 32 psi (2,2 bar)
Wetted Materials . . . . . . . . . . . .SS 316, Buna & Teflon
Immersion Length
. . . . . . . . . . .47" (1200 mm) (Tanks)
39
" (1000 mm) (Drums & Barrels)
Discharge Port
. . . . . . . . . . . . . . . . . . . .1 .0"
(25 mm) Hose Barb &
1 .5" (38 mm) Tri-Clamp
Motors . . . . . . . . . . . . . . . . . . . . . . . . . . . . .SP-280P Series, SP-ENC Series,
SP-A1FP, SP-A2 Series
Electric
Air
Figure 1
Model
Air Connection
Consumption
SP-A1FP
.125" (3,2 mm)
28 CFM @ 90 psi
13 .2 L/sec @ 6,2 bar
SP-A2L
.25" (6,3 mm)
28 CFM @ 90 psi
SP-A2
13 .2 L/sec @ 6,2 bar
Note:
For optimum performance make sure proper size air
lines are installed .