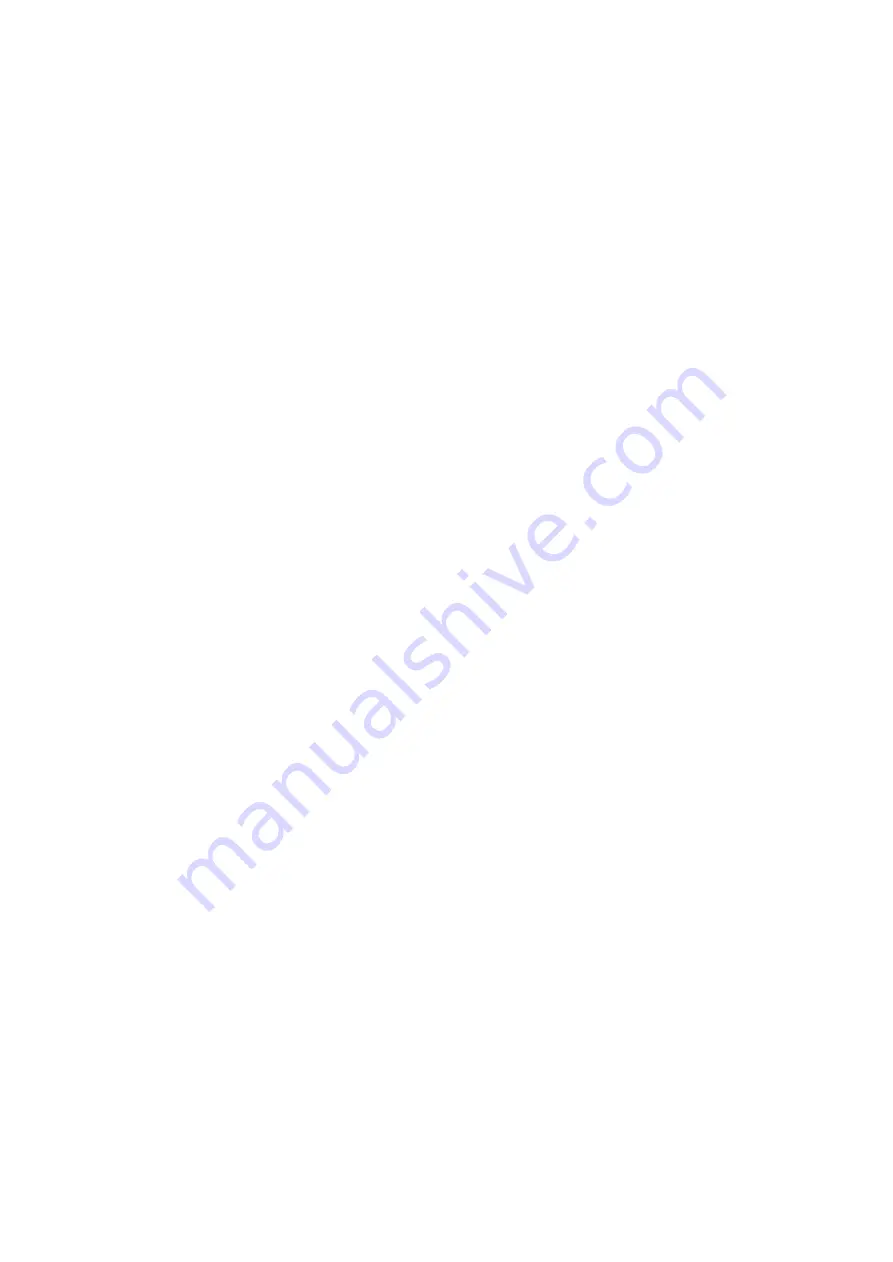
III
Use the following tools for maintenance and repair.
1.
Screw Driver
No. 2
2.
Screw Driver
6 to 7 mm
3.
Allen Wrenches
1.5, 2, 2.5, 3, 4, 5, and 6 mm
4.
Open-ended Wrench
5.5 x 7 mm
8 x 10
13 x 17
5.
Box Wrench
5.5 mm
6.
Snap-ring Expander
1. The following signs in this manual
represent wire color.
Sign
Color
C
Brown
R
Red
O
Orange
Y
Yellow
G
Green
B
Blue
V
Violet
H
Gray
W
White
D
Black
S
Transparent
LY Light Yellow
LG Light Green
LB Light Blue
P
Pink
2. The following abbreviations in this manual
represent electronic and electrical parts.
Abbreviation Meaning
CL
Clutch
BK
Brake
SW
Switch
mSW
Microswitch
M
Motor
LED
Light Emitted Diode
VR
Potentiometer
RY
Relay
II Signs and Abbreviations in This Manual
I Necessary Tool for Maintenance and Repair
Summary of Contents for PF-P320
Page 27: ... 22 ...