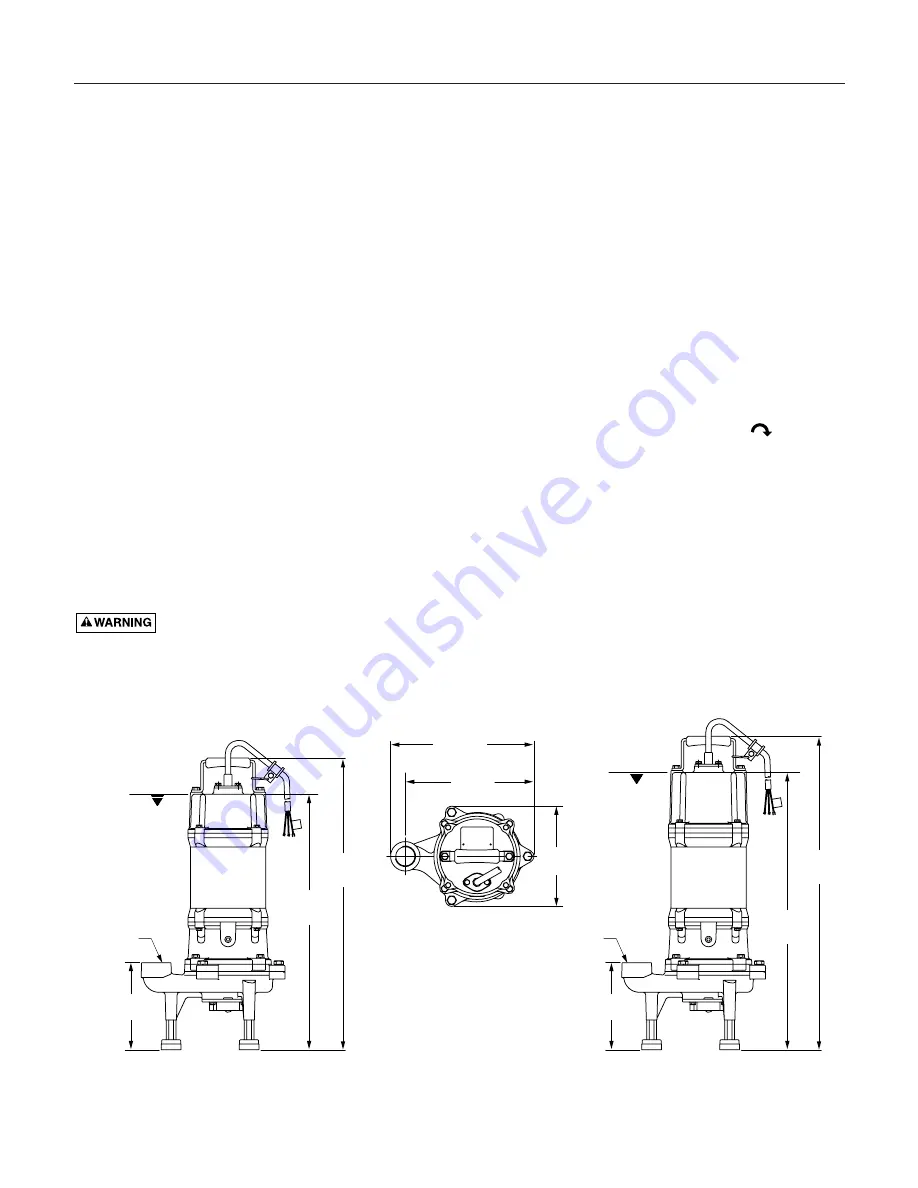
Installation / Electrical
3
INSTALLATION
This pump may be installed on a guide-rail lift-out sys-
tem for ease of inspection and service. Guide rails allow
removal of the pump without disturbing the piping or
requiring personnel to enter the wetwell (most codes
require protective equipment and training before entering
the wetwell). If installed with a guide-rail system, place
the pump opposite the influent opening to prevent stag-
nant areas where solids can settle.
Install the pump on a hard, level surface (cement,
asphalt, etc.). Never place the pump directly on earth,
clay, or gravel surfaces. The basin must be at least 18"
(458 mm) in diameter and 30" (762 mm) deep.
The pump’s feet are shipped loose in the crate with the
pump. Install them before putting the pump in the pit.
Pump Mount
Install the pump as a free standing unit.
Set the pump on the floor of the basin. Install a pipe union
in the discharge piping to allow removal for servicing.
Piping
The piping must not be smaller than the pump discharge.
ELECTRICAL
Hazardous voltage. Can shock, burn, start
a fire, or kill. When installing, operating, or servicing
this pump, follow electrical safety instructions below.
Only trained service personnel should install or service
this pump.
1. DO NOT splice the power cord.
2. DO NOT handle or service the pump while it is con-
nected to the power supply.
3. DO NOT operate the pump unless it is properly
grounded. Wire the pump directly into a grounded ter-
minal block in an automatic float or pump controller
box for automatic operation. Connect the pump
according to all applicable codes. For continuous
operation, wire the pump directly into the switch box.
4. Incorrect voltage can cause a fire or seriously damage
the motor and voids the warranty. Make sure that the
frequency and voltage shown on the nameplate cor-
responds to the frequency and voltage of the electri-
cal supply. The supply voltage must be 10%
of the nameplate voltage. If in doubt consult a
licensed electrician.
5. The pump rotation must be clockwise (
– viewed
from the top of the pump). NEVER operate it in
reverse.
6. Connect the pump to its own circuit with nothing else
on the circuit. See Table I, Page 4, for fuse or circuit
breaker sizes. See Figures 2 and 3 for 230/460 Volt 3
phase connection diagrams. Use a control panel sized
to match the pump. Refer to Control panel installation
instructions for wiring connection information.
7. Install the pump in accordance with all electrical
codes that apply. Install a fused disconnect switch or
circuit breaker in accordance with local codes.
8. If a three phase unit runs backwards, interchange two
of the three power supply wires to reverse the motor’s
direction of rotation.
25
(635)
22-3/32
(561)
1-1/4" NPT
Discharge
7
(178)
1-1/4" NPT
Discharge
Minimum
Water Level
11-7/16
(291)
10-1/4
(261)
8
(203)
Minimum
Water Level
21-5/8
(549)
19-1/16
(484)
7
(178)
Three-Phase Pump
Single-Phase Pump
4331 0203
Figure 1: Dimensions in Inches (mm)