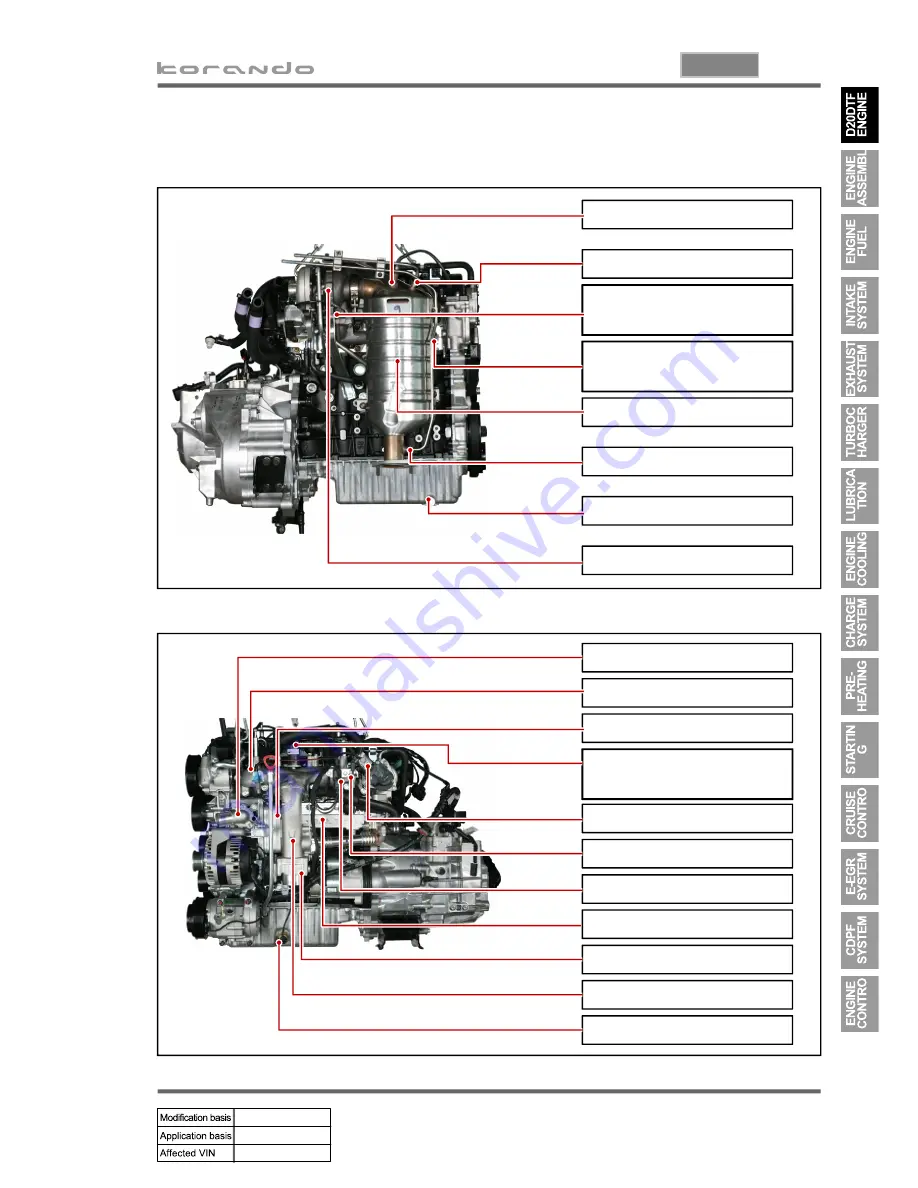
01-5
D20DTF ENGINE INFORMATION
korando 2010.10
0000-00
Right view
▶
Wide-band oxygen sensor
Pressure port before CDPF
Front exhaust gas
temperature sensor
Rear exhaust gas
temperature sensor
CDPF assembly
E-VGT
Pressure port after CDPF
Oil drain plug
Left view
▶
Thermostat assembly
Knock sensor 1 connector
Variable swirl valve assembly
Oil cooler assembly
E-EGR valve
Knock sensor 2 connector
E-EGR solenoid valve
EGR cooler
Electronic throttle body
T-MAP sensor
Oil level switch