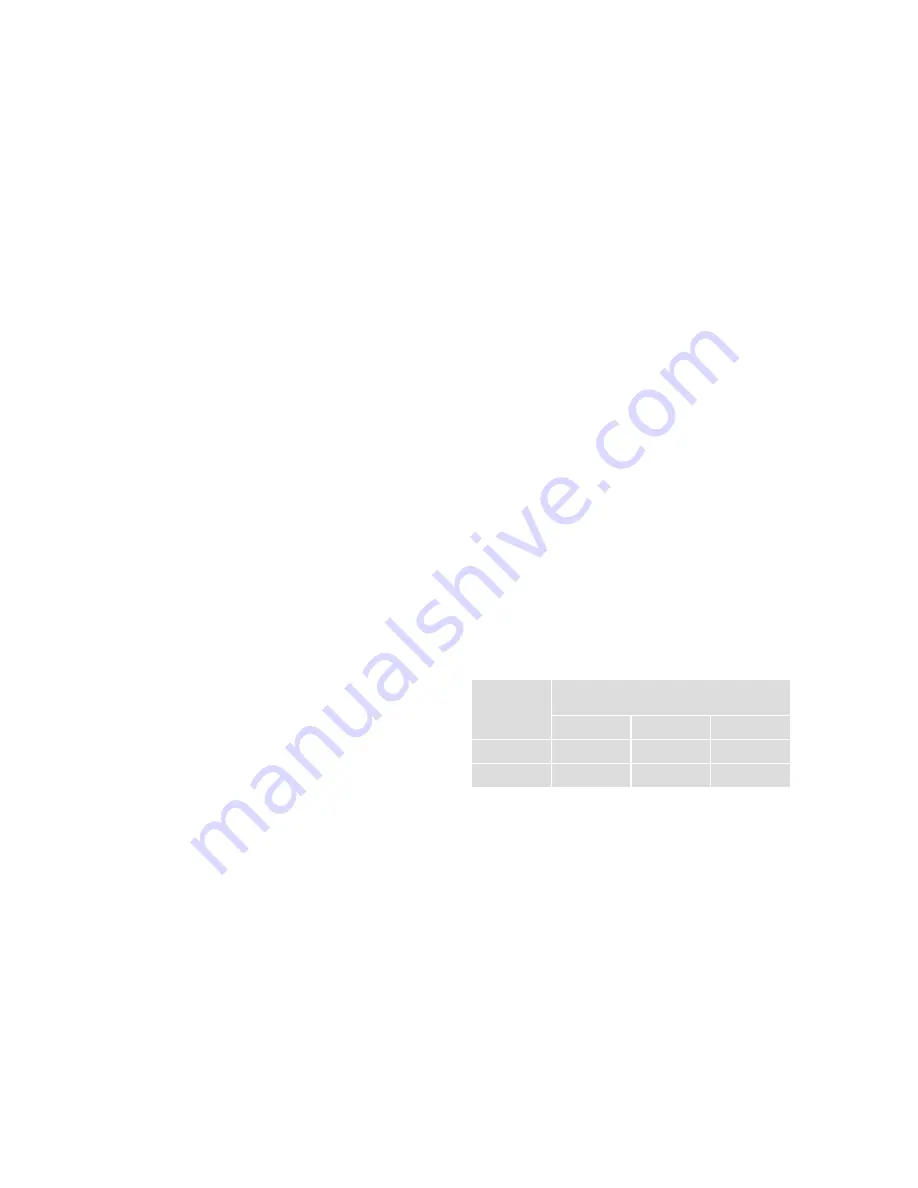
42
7.5.8 Preheating
Preheating decelerates the cooling of the welded joint and
lessens the degree of hardening. This prevents the formation
of a hard and brittle zone in the HAZ, and thereby the
development of hydrogen cracks. The need of preheating
depends on steel grade, material thickness, filler metal
(hydrogen content), heat input and welding conditions. High-
strength steel, thick material, high hydrogen content (e.g. moist
electrodes) and low heat input are factors that increase the
need of preheating. More detailed instructions for the selection
of preheating can be found for example, in SSAB’s manual
“Hot rolled steel plates, sheets and coils. Welding”. Usually, for
example, no preheating is required when welding S355 steel
less than 20 mm thick provided that dry basic electrodes are
used. Moist electrodes must always be dried before use. When
welding at temperatures below +10 °C, the pile ends are to be
preheated to +50 to +100 °C before starting the work.
7.5.9 Welding
Pile ends must be clean inside and out for a distance of about
50 mm on each side of the groove. If necessary, any impurities,
grease, moisture, rust, etc. is to be removed as they are likely
to cause welding defects and thereby impair the quality of the
weld. Any possible backing must also be cleaned, if necessary.
After joint preparation and cleaning, the pile ends are centred
and carefully fitted together so that the inner surfaces of the
two pile sections are aligned and the required air gap remains
between them (see Figures 13 and 14). The fitting of the pile
ends together can be facilitated by welding guide blocks
onto one pile; they are removed after tacking. There also are
special devices on the market for centring pipes. Wedges,
electrode core wires (e.g. 3.2 mm), etc. can be used to ensure
the required gap width; they are removed after tacking.
If the gap width varies, it must be ensured that it meets
the minimum requirement even at its narrowest point.
Any difference in root face height must be eliminated by
grinding before aligning the pile sections. Thereafter, the
pile ends are connected by short tack welds. If a tack weld
is left in the groove as part of the root run, the ends of tack
welds must be carefully ground to remove any crater pipes
and to ensure full penetration.
A 2.5 mm electrode is recommended for the manual
welding of root runs. Filling and capping runs are usually
made with 3.2 mm electrodes. With thick-walled pipes,
even thicker electrodes may be used for filling and capping
runs. The most common wire diameter of a tubular cored
electrode is 1.2 mm. However, tubular cored electrodes
ranging from 0.9 mm to 1.6 mm are available depending on
the intended application and requirements.
The supplier of the welding apparatus provides the
necessary training for mechanized welding.
Piling can be continued when the weld is cooled below
500 °C.
7.5.10 Inspection of Welded splices
Inspection of welds is conducted in accordance with the
requirements and scope of inspection specified in the design
documents. Unless otherwise specified, the following is to be
observed in the inspection requirements and scope:
In piling class 1 sites, all welds of piles are first examined
visually. Visual inspection is aimed to detect any
imperfections in weld dimensions, misalignments,
undercuts, defects breaking the surface, etc.
At piling class 2 sites, the welder is usually required to make
a so-called production weld test before starting the work,
where two pile pipes are joined by welding according to the
welding instructions. The result must meet the requirements
of the required weld quality level in terms of observable
errors. The results of the production weld test are recorded
in the piling inspection documents.
Besides the production weld test and visual inspection, piling
class 3 sites usually require inspecting at least 10 % of the
welds by a non-destructive test (NDT), such as an ultrasound
test. Test length is the entire weld, that is, one weld out of ten is
inspected entirely, unless otherwise agreed.
Table 32 presents the number of NDT tests on welded splices
in different welding quality levels and consequence classes.
Table 32. Number of NDT tests on the welded splices of
compression loaded steel piles in different piling classes
and consequence classes.
Piling
class
Number of NDT tests, percentage of welds
CC1
CC2
CC3
PTL3
-
10
15
PTL2
-
-
10
NDT tests on compression loaded piles can be made
right after the welding when the weld has cooled down
sufficiently for the test.
With tension piles the minimum cooling times of Table 23 in
EN 1090-2 are to be observed before performing NDT tests,
unless otherwise agreed for an individual project.
If mechanised welding is used, for example, in foundation
underpinning projects where the number of splices per pile is
large, the number of tests is always indicated in the designs.
Generally tests are made for 10 % of all piles and for at least
two welds per pile. The test is started with the first weld and
cover, for example, internal defects of the weld and defects of
the root side of the weld. Defects exceeding the limit values
of weld quality levels specified in standard EN ISO 5817 and
affecting strength are repaired. Repaired welds are tested
anew, and two other welds are also tested.