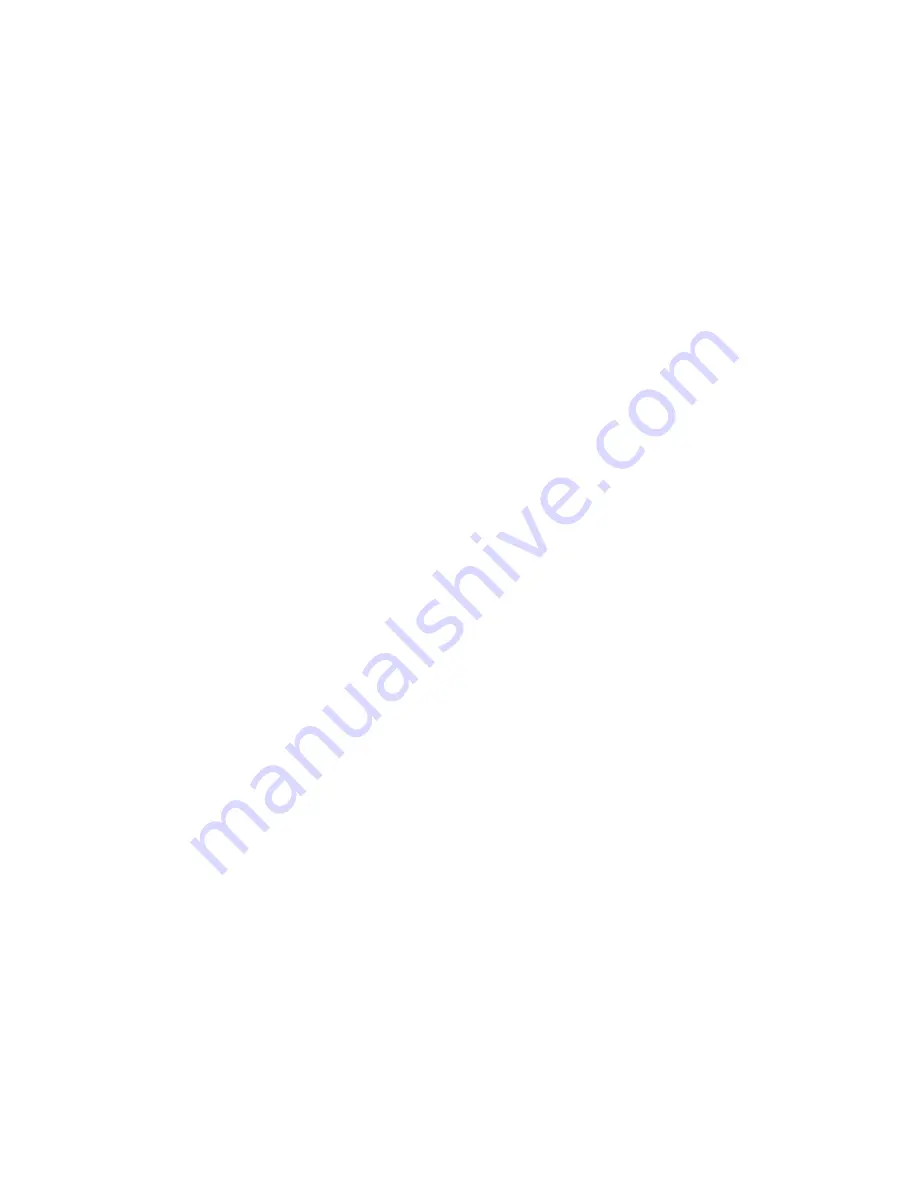
34
7.3.9 Preparation of end-of-driving instructions for
large diameter piles in piling classes PTL3 and
PTL2
In the beginning of piling, test piles are installed at spots
highly representative of the soil conditions. One or more
piles are usually installed where pile lengths are the longest
or the soil conditions are most demanding in terms of
driving. Test piles usually become part of the final structure,
but separate test piles may be used, if necessary.
At the pile testing stage it is useful to drive piles with
different end-of-driving criteria. Then, the ”strictest” end-
of-driving criteria used are the end-of-driving instructions
or maximum drop heights presented in the end-of-driving
tables for PTL3. Yet, it may advantageous to install piles, for
example, using the end-of-driving criteria for PTL2. In the
case of large diameter piles that have no general end-of-
driving criteria, the criteria for final blows before load tests
are defined case by case considering the pile driver, the pile
(diameter, wall thickness and length) and soil conditions.
Dynamic load tests are made on the piles of the piling test
stage. A special load test hammer is recommended for load
tests on piles installed with hydraulic rams or pneumatic
hammers in order to mobilise sufficient geotechnical
resistance. If it is observed during piling that the piles bear
on bedrock, the load tests can be made very soon or even
immediately after pile installation. When piles bear on soil
layers, the recommended interval between installation and
testing is at least 24 hrs, preferably longer. The resistance
measured from piles is generally the higher, the longer the
waiting period. The target levels of dynamic load tests are
defined at the design stage according to Sec. 5.5.4.
Suitable end-of-driving criteria for the site are determined
on the basis of dynamic load tests. If pile lengths and soil
conditions vary a lot, different end-of-driving criteria are
assigned to different pile lengths and soil conditions.
7.3.10 Final blows on friction piles
In piling tests before or at the beginning of actual piling, friction
piles are usually driven to the level designed on the basis
of geotechnical investigations and static bearing capacity
formulas and/or driving resistance based on a preliminary
estimate or analysis based on the stress wave theory.
Geotechnical resistance is measured by dynamic load tests
using signal modelling (e.g. CAPWAP analysis). In coarse-
grained soil layers skin friction usually develops in less than
a week, but in silty soil it may take considerably longer. The
target depth level and/or final driving resistance of piles are
determined on the basis of the results of dynamic load tests.
7.3.11 Project-specific driving instructions
Project-specific driving instructions must always be
prepared in piling class PTL3, and they must include at least
the end-of-driving criteria and maximum drop heights
for drop and hydraulic hammers. In the case of large
diameter piles with no predefined end-of-driving criteria,
project-specific driving instructions are also prepared in
piling class PTL2. Project-specific driving instructions are
recommended for friction piles also in PTL2. If necessary,
detailed instructions are given for the following:
•
drop height or impact energy used at different stages
of driving
•
instructions for filling closed top-driven piles with water
•
detailed instructions on driving the dowel of a rock shoe
into bedrock
•
instructions on measures to be taken in the case of
expected special events occurring during blowing
•
instructions on reporting responsibilities and detailed
instructions for a keeping piling record
•
instructions on dynamic load tests (quantities, waiting
periods, target levels)
7.3.12 Installation of jacked-RR piles
Jacked-RR piles are generally installed using hydraulic
jacks. The installation equipment must conform to
Ch. 2, Sec. 5.4.2.4 of PO-2016 and installation is to be
done according to Ch. 2, Sec. 5.4.4.5 of PO-2016.
7.4. Installation of RD piles
7.4.1 Piling equipment and drilling methods
The general requirements for RD piling equipment are
presented in Sec. 5.4.2.1 of PO-2016.
Top hammer or DTH hammer drilling equipment is used
with RD piles. Both can use either the eccentric or
concentric drilling method.
7.4.1.1 Top hammer-based equipment
The hammer drill of top hammer drilling equipment is
generally pneumatic or hydraulic. The drilling equipment
also includes a rotary unit and drill rods. Top hammer
equipment can be used to drill piles up to diameter RD170.
The blow of the hammer drill generally strikes the drill rod
inside the pile, which is being rotated simultaneously, and
subsequently the casing shoe at the lower end of the RD pile.
As a result, drilling capacity diminishes as pile length and the
number of drill rod splices increase. The maximum pile length
with top hammer equipment is generally about 30 m, although
it is possible to install 50 m piles in thick, soft cohesion soil
layers. With some top hammer equipment types, the RD pile
pipe also takes part of the blow of the hammer drill.
7.4.1.2 DTH hammer-based equipment
The hammer drill of DTH hammer-based equipment is
generally pneumatic or water powered. The equipment
also includes a hydraulic rotary unit and drill rods.