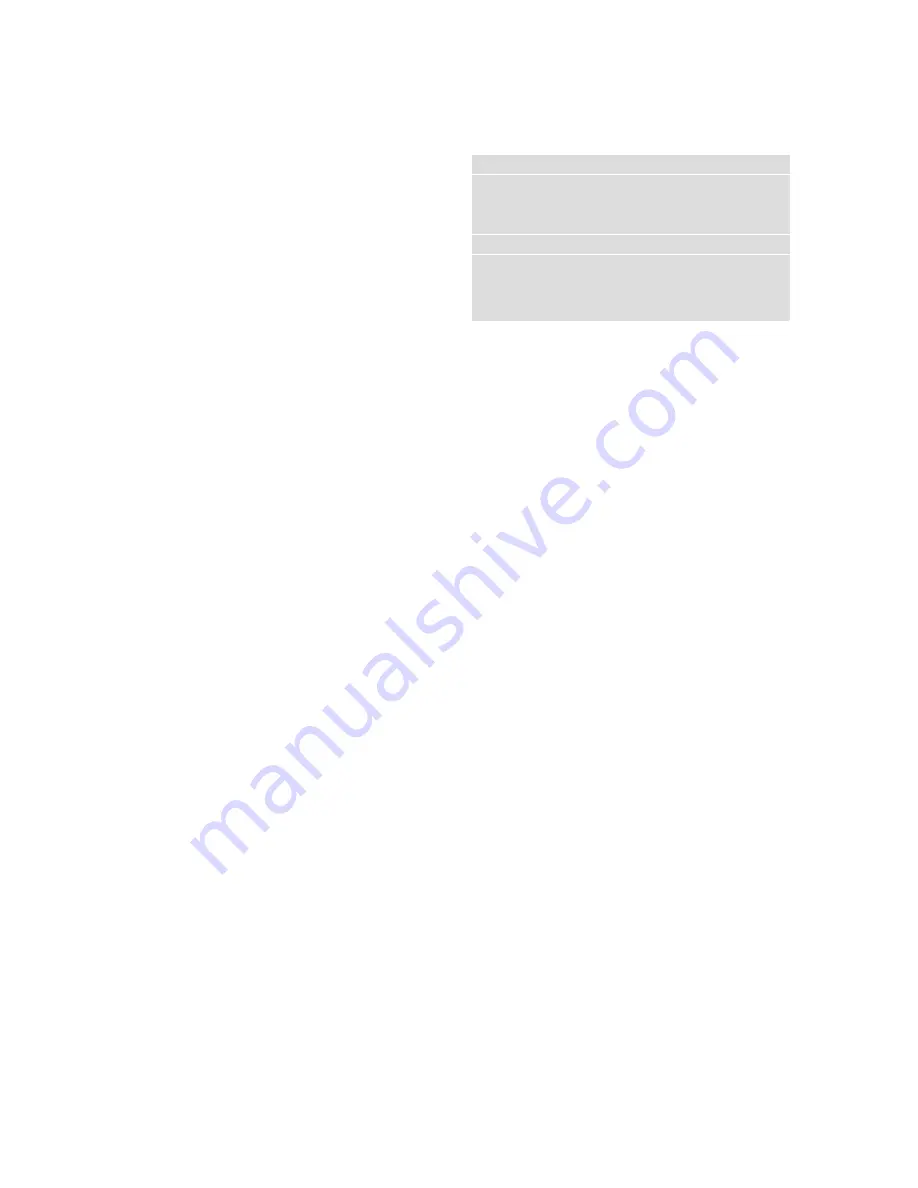
40
7.5.4 Welding Procedures
Manual metal arc welding is the conventional welding
procedure for splicing steel piles on sites. It is a versatile
and flexible method that uses simple, easily transportable
equipment.
Flux cored arc welding is a more modern welding procedure.
Its advantages include high efficiency, consistent weld
quality and suitability for mechanised production. Different
types of welding nozzle conveyors attachable to the
pipe are available for mechanised flux cored arc welding.
These devices facilitate work in cramped spaces, such as
underpinning sites, where piles must be positioned close to
a wall. The space between pile and wall may be as narrow
as 150 mm. When welding with shielding gas, it may be
necessary to use screens to prevent the detrimental effect
of wind and draught. There are also cored filler wires on the
market that can be used without shielding gas.
Workshop welding may be carried out by any welding
procedure for non-alloy steels.
7.5.5 Welding Consumables
The standards for covered electrodes are EN ISO 2560
(Welding consumables. Covered electrodes for manual
metal arc welding of non-alloy and fine grain steels.
Classification) and EN ISO 18275 (Welding consumables.
Covered electrodes for manual metal arc welding of high
strength steels. Classification).
The standards for cored wires and rods are EN ISO 17632
(Welding consumables. Tubular cored electrodes for
metal arc welding with and without a gas shield of non-
alloy and fine grain steels. Classification), EN ISO 14341
(Welding consumables. Wire electrodes and weld deposits
for gas shielded metal arc welding of non alloy and fine
grain steels. Classification) and EN ISO 18276 (Welding
consumables. Tubular cored electrodes for gas-shielded
and non-gas-shielded metal arc welding of high-strength
steels. Classification.)
Filler materials are to meet the above standard
specifications.
Filler materials are chosen on the basis of the strength
and impact-strength requirements of the steel grade
of the piles according to Table 30 or SSAB’s manual
”Kuumavalssatut kelat ja -levyt, Materiaalivalinta,
Hitsausaineet”. The complete classification specifications
of the welding consumables presented in Table 30
according to EN standards are as shown in Table 31:
Table 31. Designation of welding electrodes and cored
electrodes.
Covered electrodes:
ESAB OK 48.00: EN ISO 2560: E 42 4 B 42 H5
ESAB OK 48.08: EN ISO 2560: E 46 5 1Ni B 32 H5
ESAB OK 55.00: EN ISO 2560: E 46 5 B 32 H5
ESAB OK 74.78: EN ISO 18275: E 55 4 MnMo B 32
Tubular cored electrodes:
TRI-MARK TM-770: EN ISO 17632 T 42 2 P M 2 H10
TRI-MARK TM-881 K2: AWS E81T1-K2J, E81T1-K2 MJ H8
ESAB OK Tubrod 15.14: EN ISO 17632 T 46 2 P M/C 2 H10
ESAB Dual Shield 55: EN ISO 18276-A, T55 4 Z P M H5
ESAB Filarc PZ 6138: EN ISO 17632-A, T 50 6 1Ni P M21 1 H5
When welding together pile sections of different strength or
type, the filler is generally selected according to the softer
or less alloyed steel grade. However, when for instance wel-
ding fixtures, etc. to a pile, the filler is selected on the basis
of the more alloyed steel (pile) in order that the filler to be
incorporated into the pipe wall is sufficiently alloyed.
Covered electrodes must be of the basic type, indicated
by the letter B (basic) in the designation.
When necessary, subject to agreement between the parties,
the root run can be welded with filler material of lower
strength than the parent metal. The coatings of covered
electrodes and some cores of tubular cored electrodes being
hygroscopic, they easily absorb moisture from ambient air.
Moisture may cause gas pores, splatter and, in the worst
case, hydrogen cracking in the weld. Therefore, it is important
to handle and store these products carefully. The contractor
is obliged to ensure that filler materials remain dry on
site. They are to be stored in a dry and warm space which
prevents moisture from condensing inside the package due
to variations in temperature.
At the actual welding site, filler materials are to be
protected from rain, etc. and electrodes to be kept in a
separate heated quiver from which the welder withdraws
them one at a time. Electrodes are also available in
hermetically sealed packages. Each package contains
just a few electrodes which can be used within 4 hours of
opening the package without the risk of humidification.
Moist or otherwise damaged filler materials must not
be used. Wet electrodes can be dried according to the
manufacturer’s instructions, for example at +300 °C to
+400 °C for 2 to 3 hours.
When welding is finished, the coils of tubular cored
electrode should be removed from the machine and taken
to a dry and warm place for storage.
7.5.6 Welding Conditions
Weather is a major factor affecting weld quality and the
welders’ working conditions. Welding conditions that enable
attaining the planned quality level must be provided.
If necessary, the welding site should be appropriately
protected against wind and rain, and it should also be