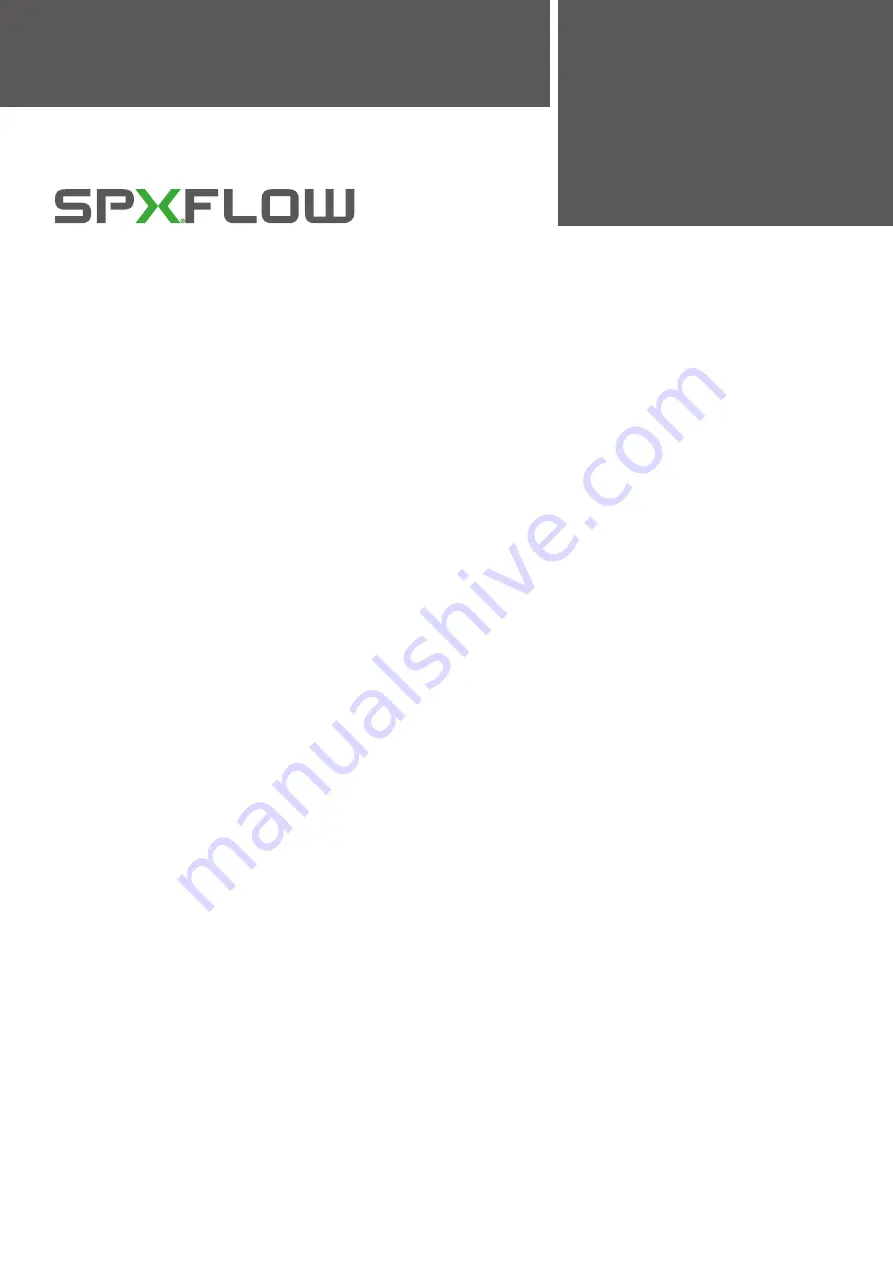
SPX FLOW
SPX FLOW
Design Center
Production
Gottlieb-Daimler-Straße 13
Stanisława Jana Rolbieskiego 2
D-59439 Holzwickede, Germany
PL - 85-862 Bydgoszcz, Poland
P: (+49) (0) 2301-9186-0
P: (+48) 52 566 76 00
F: (+49) (0) 2301-9186-300
F: (+48) 52 525 99 09
SPX FLOW reserves the right to incorporate the latest design and material changes without notice or obligation.
Design features, materials of construction and dimensional data, as described in this manual, are provided for your information only and should not
be relied upon unless confirmed in writing. Please contact your local sales representative for product availability in your region.
For more information visit www.spxflow.com.
ISSUED 06/2019 - Original Manual
COPYRIGHT ©2019 SPX FLOW, Inc.
APV CU4plus AS-interface
CONTROL UNIT