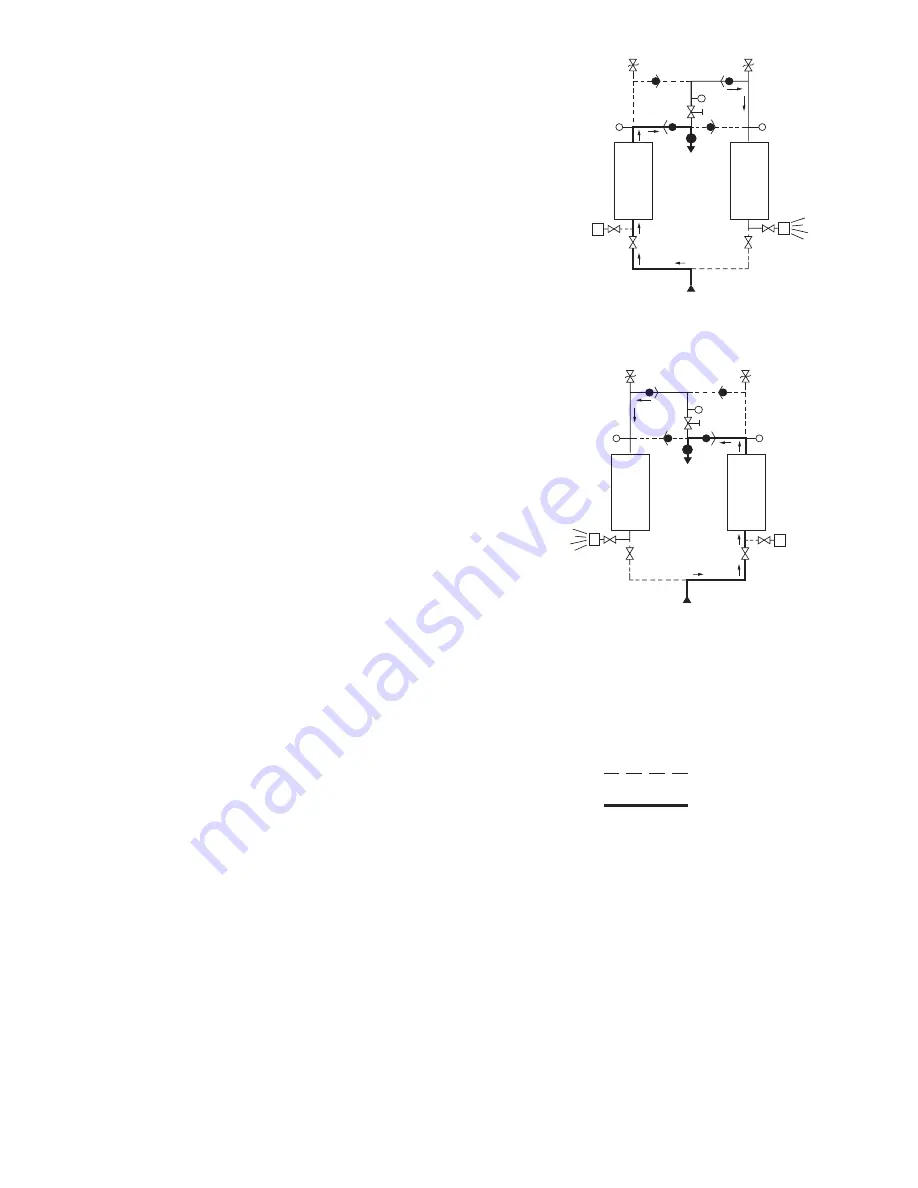
5
8
1
5C
5D
8
7
) (
2
6
1
5A
10A
9A
3A
3B
9B 10B
5B
11
INLET
TOWER
4B
TOWER
4A
OUTLET
FIGURE 1A
TOWER 4A DRYING: TOWER 4B REGENERATING
Purge Stream
Process Stream
FIGURE 1B
TOWER 4B DRYING: TOWER 4A REGENERATING
1.2 Description of Operation
1.2.1 Dryer (
Refer to Figure 1A.)
Compressed air flows through inlet switching valve (3A) (normally open)
to tower (4A) where the air is dried. After the air is dried it flows through
check valve (5A) and then to the dryer outlet.
A portion of the dry air, the purge stream, branches off from the main air
stream prior to the outlet. The purge stream flow rate is controlled by the
adjustable purge rate valve (6) and the purge orifice (7).
The purge flow, which has been throttled to near atmospheric pressure,
is directed through check valve (5D) to tower (4B). As the purge flow
passes over the desiccant in tower (4B), it removes the water vapor
which was deposited there while the tower was on-line drying. The purge
air then passes through purge and repressurization valve (9B) (normally
closed) and purge muffler (10B) to the atmosphere.
After regeneration, purge and repressurization valve (9B) (normally
open) closes allowing tower (4B) to repressurize slowly. Adequate
repressurization time is allowed so that tower 4B is fully repressurized
before switchover. After a controlled time period, air inlet switching valve
(3B) (normally open) opens and inlet switching valve (3A) (normally
open) closes, purge and repressurization valve (9A) (normally closed)
then opens.
(Refer to Figure 1B.)
Tower (4B) is now drying the main air stream while
tower (4A) is being regenerated by the purge air stream. The operation
of the inlet switching (normally open) and purge and repressurization
valves (normally closed) is sequenced by the control system located in
the electrical box.
8
1
5C
5D
8
7
) (
2
6
1
5A
10B
9B
3B
3A
9A
10A
5B
11
INLET
TOWER
4B
TOWER
4A
OUTLET
1. Pressure Gauges
2. Purge Pressure Gauge
3. Inlet Switching Valves
4. Desiccant Drying Towers
5. Check Valves
6. Adjustable Purge Rate Valve
7. Purge Orifice
8. Pressure Relief Valves
9. Purge / Repressurization Valves
10. Purge Mufflers
11. Moisture Indicator