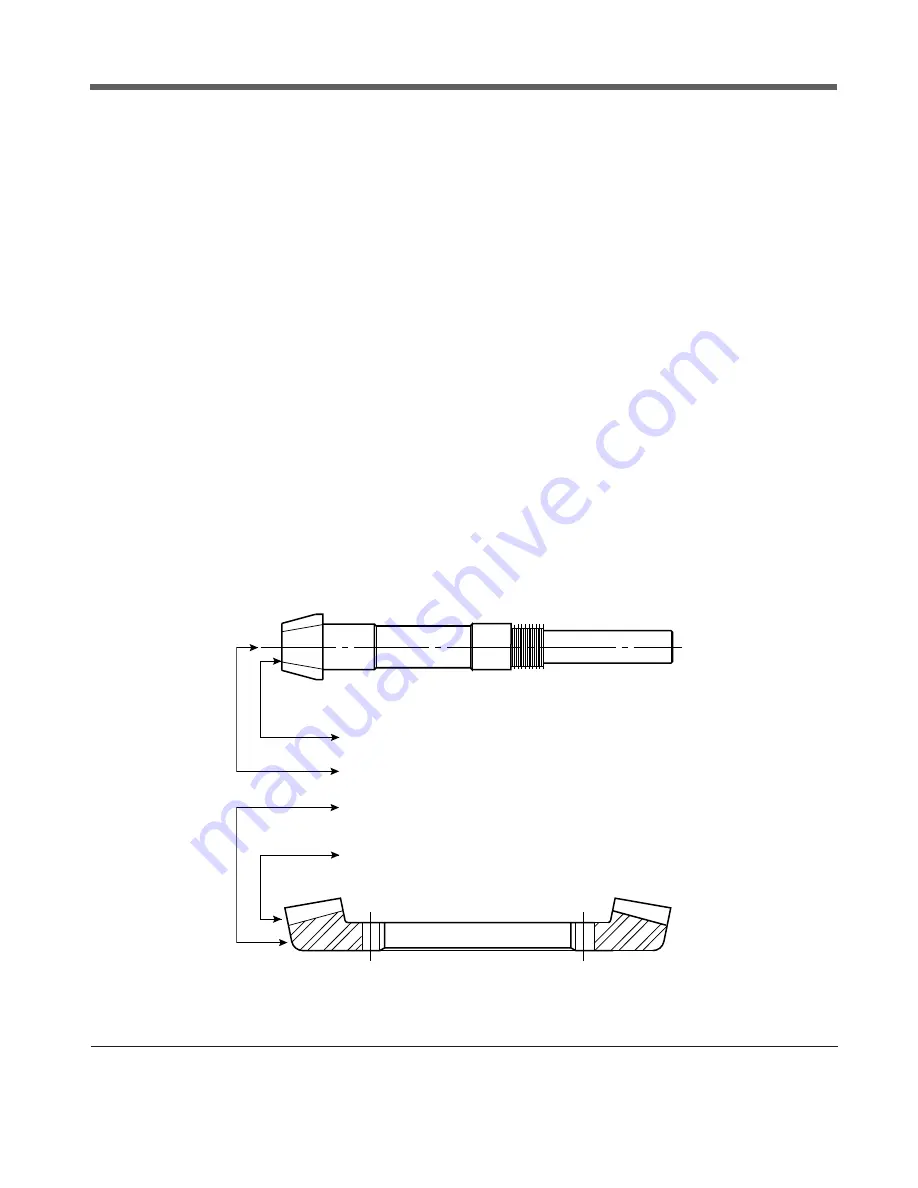
8
field repair
GENERAL
Geareducers can be repaired in the field—however, major repairs
require the use of a fully equipped machine shop. When field repair
or replacement of parts is necessary, the following procedure is
recommended for the disassembly and assembly of the unit. If any
O-ring, oil seal or gasket is to be reused, care should be taken
not to damage it during disassembly. Parts which contain O-rings
or seals should not be jerked or twisted past a shoulder or edge.
These parts are marked with an asterisk (*) in the description
below. O-rings, oil seal and gaskets should be carefully inspected
for damage before being reinstalled. Marley recommends that new
O-rings and oil seal be installed during a major overhaul.
DISASSEMBLY
Part numbers and references—refer to
Figure 3
.
1. Drain oil.
2. Remove outer ring of bolts in pinion cage and remove pinion
subassembly*.
Note
—The thickness of the shim pack (
320
) is important in reset-
ting the gears. The shim pack should either be saved or carefully
measured with a micrometer. If the gears are to be replaced,
record the pinion setting distance that is etched on the pinion
gear. See
Figure 4
.
3. Remove water slinger*.
4. Remove bearing retainer and shim pack (
420
) from top of
case.
Note
—The thickness of this shim pack is important in
the endplay and backlash setting of the gears. The shim
pack should either be saved or carefully measured with a
micrometer.
FIGURE 4
Gear Match Numbers and Setting Data
MATCHED NUMBER TO BE COMPARED WITH THE SAME
NUMBER ON THE RING GEAR. (EXAMPLE CO-43)
PINION SETTING DISTANCE. (EXAMPLE 4.860)
BACKLASH (NORMAL) AT WHICH THE GEARS WERE
LAPPED. (EXAMPLE .010)
MATCHED NUMBER TO BE COMPARED WITH THE SAME
NUMBER ON THE PINION GEAR. (EXAMPLE C0-43)
THE PINION SETTING DISTANCE IS THE DISTANCE
THE END OF THE PINION SHOULD BE FROM THE
CENTERLINE OF THE RING GEAR SHAFT.