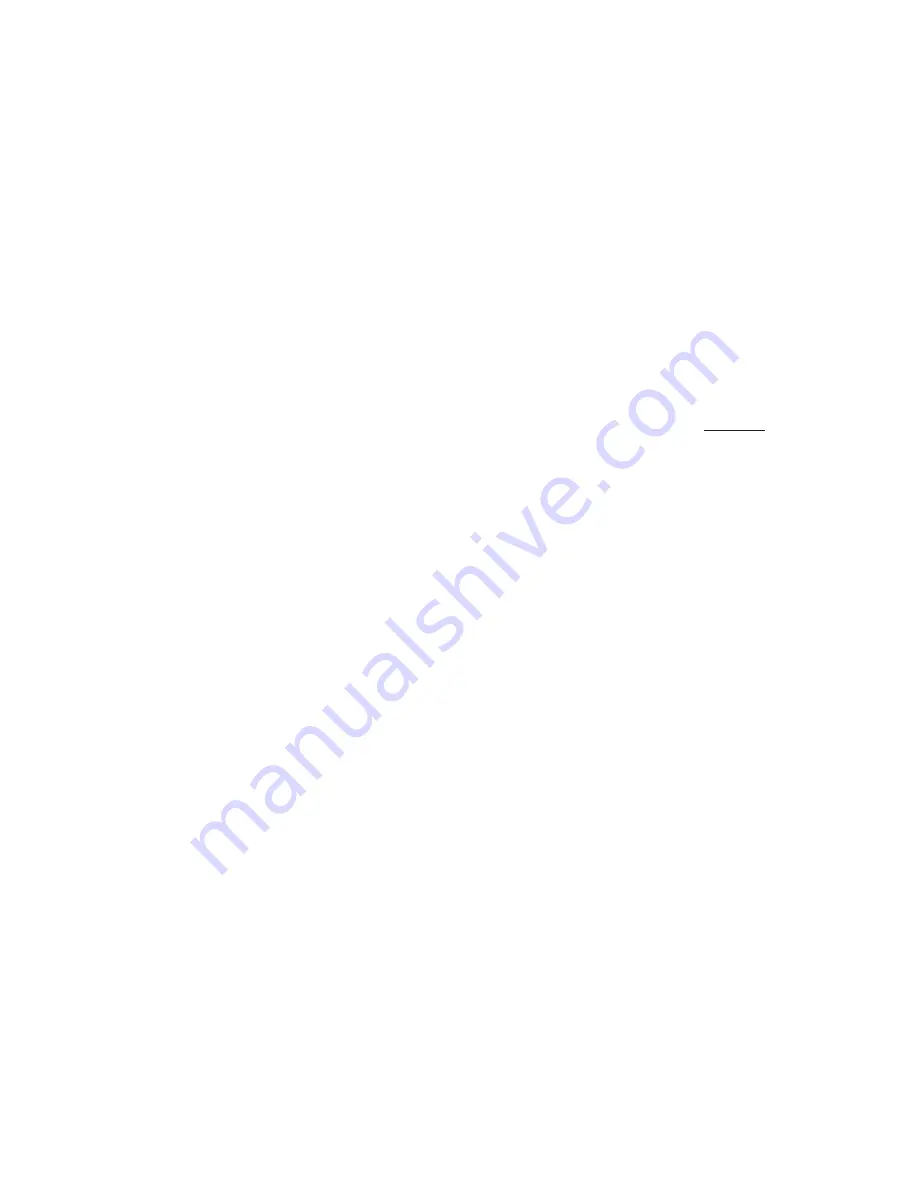
© SPX FLOW, Inc.
Form No. 1000623
Rev. 6 Jan. 10, 2017
Initial Setup
Each hydraulic torque wrench is supplied completely assembled and ready for use. A hydraulic pump
is required to provide the speed and pressure that makes the hydraulic wrench system efficient and
accurate.
1. Read and understand all instructions before operating the hydraulic torque wrench. It is the operator's
responsibility to read, understand, and follow all safety instructions.
2. Remove the hydraulic torque wrench from the shipping container and visually inspect all components
for any shipping damage. If any damage is found, notify the carrier immediately.
DO NOT USE
TOOL.
Power Requirements
The TWHC hydraulic torque wrench requires a hydraulic pump unit, twin-line connecting hose, and
couplings to operate. All components must be capable of operating at the system maximum working
pressure of 690 bar (10,000 psi). Note that the system maximum working pressure is dynamic, not
static.
Pump unit specification varies between manufacturers; however, for correct torque wrench operation,
the pump unit must include the following:
Double Acting
—Pump unit must be capable of double acting operation for advancing and retracting
the Torque Wrench.
Variable Pressure Output
—For torque setting, the pump unit must be able to be easily adjusted by the
operator for different pressure outputs.
Retract Pressure
—Sometimes termed 'idle' pressure, this is the pressure used for torque wrench
retraction and must be fixed at approximately 103 bar (1,500 psi). This pressure must not be operator
adjustable.
Remote Handset Controls
—The preferred configuration for the handset is such that, upon starting the
pump unit, the pump enters retract or idle mode (pressure fixed at 103 bar (1,500 psi)). To advance the
torque wrench, the handset advance/pressure button or lever is pressed and held, upon release of the
button, retract mode is automatically entered. A separate button or lever is used to stop the pump.
Automatic Pressure Release
—The pump must automatically release system pressure when switching
between advance and retract modes.
Pump Flow Rate
—The speed at which the hydraulic torque wrench operates is proportional to the oil
flow rate. In general, 2-stage pump units are preferred for torque wrench use as this allows rapid nut
rotation under low loads, with fast wrench retraction. As a minimum, 250 cm³/min @ 7 bar (15 ci/min @
100 psi) to 20 cm³/min @ 690 bar (1.2 ci/min @ 10,000 psi) should be specified; however, for optimum
speed and performance, at least 360 cm³/min @ 7 bar (22 ci/min @ 100 psi) to 30 cm³/min @ 690 bar
(1.8 ci/min @ 10,000 psi) is recommended.
Pressure Gauge
—Clarity is important for accurate torque setting; therefore, a pressure gauge of at
least 100-mm (4-in.) diameter should be fitted.
Hydraulic Couplings
—TWHC hydraulic torque wrenches are fitted with CEJN 230 screw-to-connect
couplings (1/4-in. NPT) as standard. Verify any couplings that are used are compatible with these
couplings and rated to the same working pressure, e.g. Parker 3000 couplings.
SPX Bolting Systems will not be responsible for torque wrench damage, malfunction or operator injury
caused by the use of an incorrect pump unit; therefore, check the compatibility of your pump unit before
operating the hydraulic torque wrench.