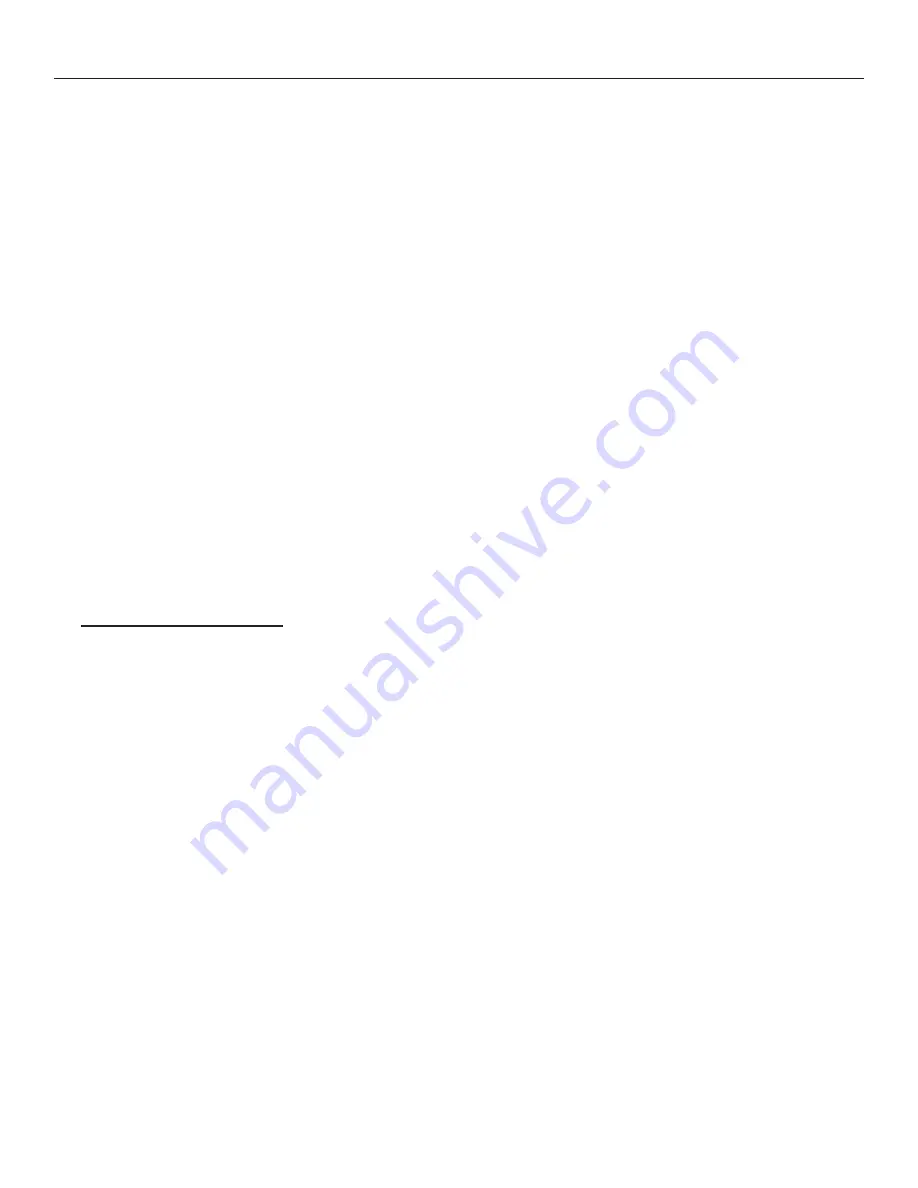
© SPX FLOW, Inc.
Form No. 1000623
Rev. 6 Jan. 10, 2017
Reaction Point Safety
Follow these guidelines when selecting appropriate reaction points:
• The reaction structure must be rigid enough to accommodate the forces from the hydraulic torque
wrench. Carefully inspect the reaction points for suitability before applying the torque tool. If in doubt,
contact the torque wrench supplier for advice.
• Tapered surfaces are generally unsuitable as the torque wrench tends to 'ride up' the taper, causing
adverse tool loads. Flat surfaces are preferred.
• Packing pieces, spacers, etc. must never be used as a makeshift reaction point. Reaction
accessories are available to increase the access to reaction points.
Use of Backing Wrenches
Backing wrenches are often used to prevent the non-tightening nut on the opposite side of the joint
assembly from turning during the torquing operation. Verify that the backing wrench is the correct
size and securely fastened in position (using straps, ropes, etc.). As the torquing operation begins, it
is normal for the backing wrench to move/rotate in conjunction with the torqued nut, until the backing
wrench contacts an adjacent reaction point. It is important that the operator stand clear of the moving
backing wrench to prevent accidental entrapment. The operator must also verify that the reaction point
is secure and sufficiently rigid to prevent damage to the structure.
Torque Wrench Selection
To choose the correct capacity Torque Wrench for the application, the estimated break-out torque
should be considered, not the tightening torque. Loosening bolts usually requires a higher torque, and if
a wrench has been selected on tightening criteria only, it will seldom perform in a break-out situation.
Break-out Considerations
Nuts / Bolts which have been correctly lubricated at the make-up / tightening stage will require
approximately 1.5 x tightening torque to loosen following a period of service, PROVIDED THEY HAVE
NOT BEEN SUBJECTED TO HEAT.
Corroded / rusted bolts, and bolts without lubrication applied at make-up, will require approximately 2 x
tightening torque to loosen. PROVIDED THEY HAVE NOT BEEN SUBJECTED TO HEAT.
Nuts / bolts subjected to heat, seawater corrosion, chemical corrosion, can require 3 to 4 x tightening
torque.
Before selecting a torque wrench for the application, ensure that the above has been considered.
Tightening Bolts
1. Apply the torque wrench and socket to the nut to be tightened, verifying that the reaction arm firmly
and squarely contacts the selected reaction point.
2. Start the pump and advance the hydraulic torque wrench. As the wrench strokes forward, the reaction
pad will press against the reaction point and the socket will rotate. When the hydraulic torque wrench
reaches the end of its stroke, the pump pressure will build rapidly. Fully retract the hydraulic torque
wrench (the wrench ratchet mechanism will be heard clicking as it retracts), and apply another
forward stroke.
3. Several forward strokes are made until the nut ceases to rotate during the stroke (known as stalling),
but bear in mind that nut rotation will always cease at the end of the wrench stroke and must not be
confused with the wrench stalling. When the wrench stalls, apply another forward stroke and observe
the pump pressure gauge. The pump pressure gauge should read the desired preset pressure.
4. Retract the hydraulic torque wrench, stop the pump unit, and remove the wrench from the nut.
Operating Instructions continued