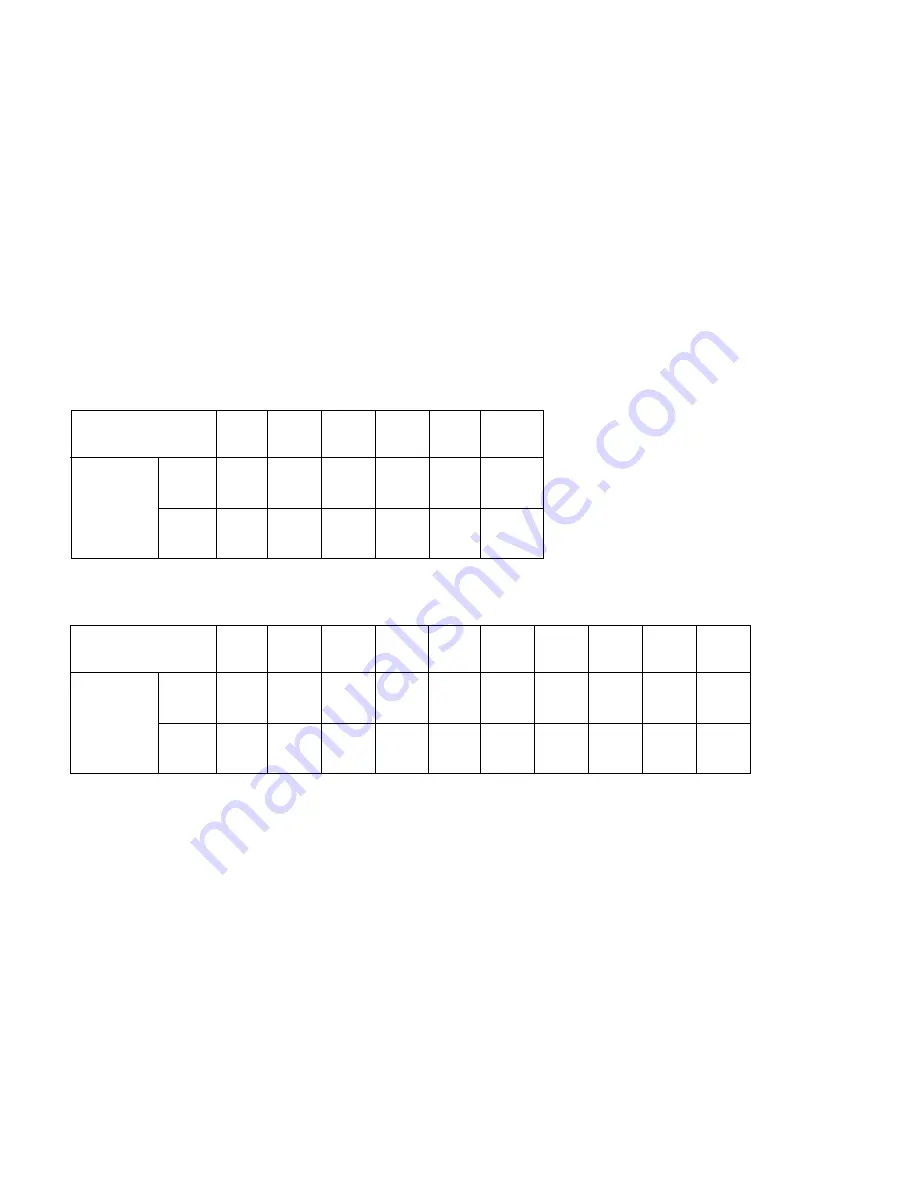
3
MINI INSTRUCTIONS
For complete instructions on installation, operation, and maintenance, consult manual.
I . INSTALLATION
1. Install on level surface.
2. Ambient temperature range: 35 to 120
°
F (1.7 to 49
°
C) [ if low ambient package supplied: -10 to 120
°
F (-23 to 49
°
C) ]
3. Install purge mufflers if shipped separately.
4. Connect air from compressor to inlet.
• Maximum compressed air temperature: 120
°
F (49
°
C)
• Maximum compressed air pressure: Refer to serial number tag.
• Minimum compressed air pressure: See section 2.2.1.2 .
5. Connect outlet to air system.
6. Refer to serial number tag for correct voltage. Make electrical connection to terminal strip in electrical enclosure. Standard units: connect
line to position 5, neutral to position 6 and ground to position 7.
Automatic purge saving system: connect wires to positions 2 and 3; ground to position 1.
7. Set controller for 120V or 240V using selector switch.
I I. START UP
1. Set or verify controller settings. See section 3.1.1.
2. SLOWLY pressurize unit.
3. Energize dryer by turning on/off switch on. ("I" is on; "O" is off)
4. Adjust purge air flow rate. Turn purge rate valve until Purge Pressure Gauge reads as shown in the following table.
NOTE: One tower must be purging when setting purge pressure.
III . OPERATIONAL CHECKPOINTS
1. Check that dryer is energized (indicating lights are illuminated)
2. MOISTURE INDICATOR - Indicator should be green (Allow 4 hours after start up for indicator to turn green).
3. TOWER PRESSURE GAUGES -
• Tower on line should read line pressure
• Tower off line should read 2 psig or less while purging. If pressure exceeds 2 psig replace purge muffler elements.
NOTE: An extra set of elements is shipped with dryer.
4. PURGE PRESSURE GAUGE - Verify proper setting.
5. CHECK FOR ALARM CONDITION.
IV . DEPRESSURIZATION
Isolate dryer. Run timer until both tower pressure gauges read 0 psig.
150 psig M.W.P. models
4
Min.
10
Min.
250 psig M.W.P. models
CYCLE
TIME
SETTING
80
79
78
77
76
75
70
64
60
57
4
Min.
10
Min.
—
—
—
—
—
132
123
115
108
102
INLET PRESSURE
60-100
110
120
130
140
150
(psig)
CYCLE
TIME
SETTING
45
43
41
39
37
36
70
66
63
60
58
56
INLET PRESSURE
125
130
135
140
145
150
175
200
225
250
(psig)