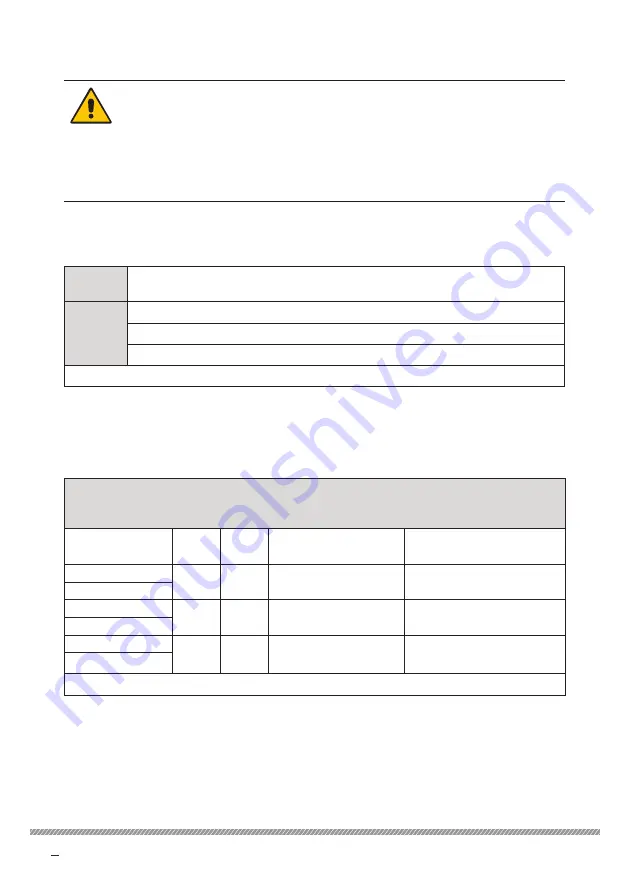
5
Installation
2.2.3 Electrical installation
WARNING!
PERSONAL INJURY AND/OR
EQUIPMENT DAMAGE HAZARD
Never work on any control equipment without first isolating all power supplies
from the equipment.
Protection must be provided by a correctly rated semi-conductor fuse, fitted
upstream of the drive. The fuse must have an I
2
t rating of less than 150 A
2
s at the
applied supply voltage.
9.
Wire the plug-in terminal blocks and re-attach to the drive. Refer to the diagrams on
page 11 and page 12.
DO NOT APPLY POWER AT THIS TIME.
Control
cable
1.5 mm
2
External
control
options
Speed setpoint from external 10K potentiometer* or isolated reference voltage
Optional external contacts for reference voltage invert/non-invert control
External RUN contact (Terminal 9) for electronic STOP/START
* Potentiometer, graduated dial and knob - Sprint Electric part number: POTKIT
FUSE - Class aR Series semiconductor - fitted upstream of the drive
To satisfy UL requirements for branch circuit short-circuit protection, the fuse MUST be of
type FWH5-020A6FR (part number CH00620A), or a lower rated fuse from the same series.
drive model
drive
rating
fuse
rating
Sprint standard fuses Fuses for UL compliance
340i
3.4 A
6.3 A
CH0066A3
Bussmann FWH-6.30A6F
340i LV60
680i
6.8 A
12.5 A CH00612A
Bussmann FWH5-12.5A6FR
680i LV60
1220i
12.2 A 20 A
CH00620A
Bussmann FWH5-020A6FR
CH00620A
1220i LV60
6 x 32 mm Panel-mount fuse holder - CP102071; DIN rail clip for fuse holder - FE101969
EMC wiring:
If the unit is going to be used in the domestic environment, then for
installations in the EU, a supply filter is recommended in order to comply with EN61800-3.
Sprint Electric part number: FRLN16.
Short Circuit Rating
Suitable for use on a circuit capable of delivering not more than 5000 A RMS Symmetrical
Amperes when protected by a Class aR Series semiconductor fuse.