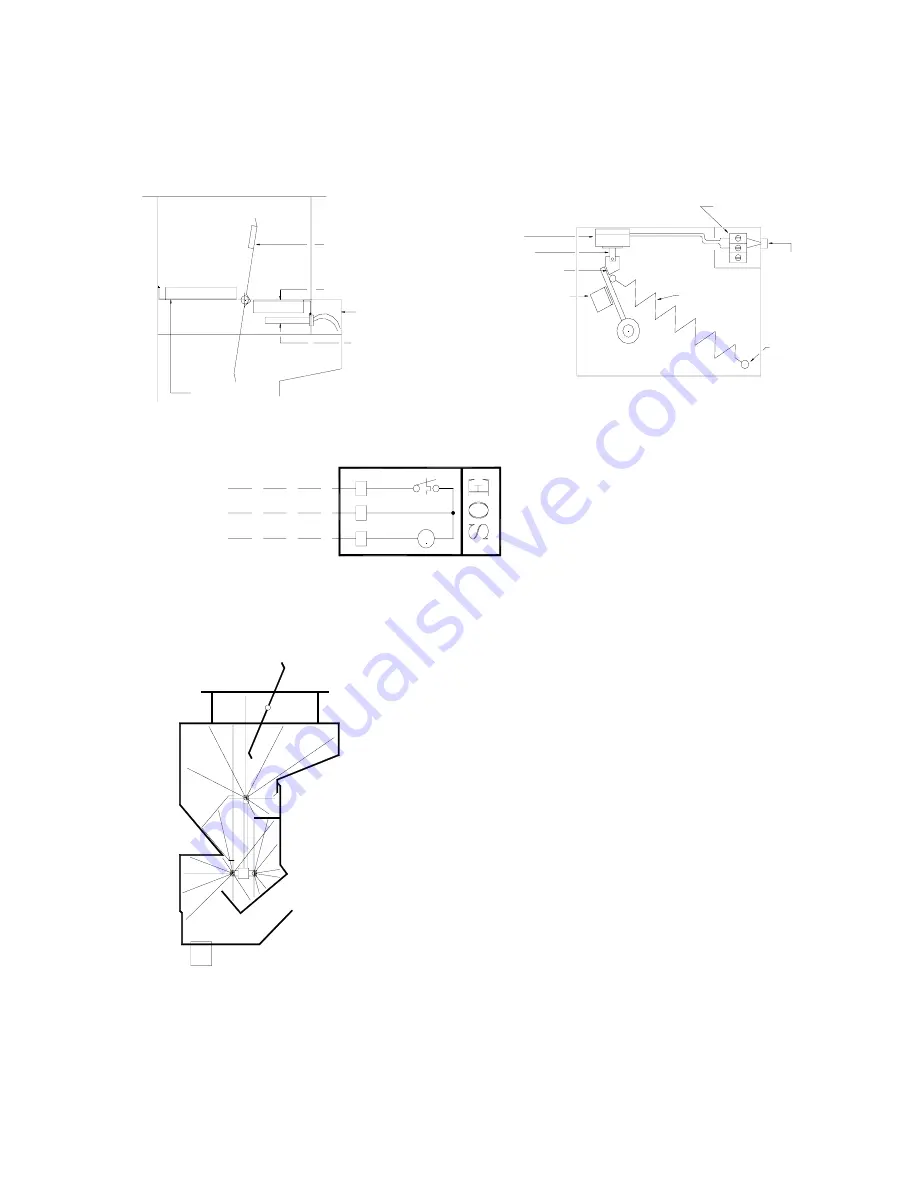
_____________________________________________________________________________________________
Spring Air Systems Water Wash Ventilator Maintenance Manual 11/01
21
Arrangement “T”: Thermostat Activated
The arrangement “T” hood and damper assembly consists of a thermostatically activated spring loaded fire damper
electrically connected to the water wash control panel by three wires.
Arrangement “T” Fire Damper
Figure 21
In addition the surface fire suppression system connect to terminals 5 & 1 the
Arrangement “T” fire damper SOE enclosure is connected to terminals 1, 2, & 4.
In the event of a fire in the grease extractor the thermostat mounted in the duct
collar is set to activate at 350 F. The thermostat energizes a solenoid, which
pulls a pin within the Fire Damper Solenoid Enclosure (SOE) releasing the fire
damper. The spring-loaded fire damper closes tight against a 40 lb. spring
force. The thermostat also activates the wash control panel through terminal 2.
Within the water wash control panel the fire relay R5 is energized activating the
water wash control panel hood and damper assembly.
1.
The exhaust fan is shut off.
2.
The hot water solenoid valve is energized releasing water into the interior
of the grease extractor.
After the fire has been extinguished, rotating a lever on the outside of the FIRE
DAMPER JUNCTION BOX - SOE, manually resets the fire damper.
Arrangement “T” & “F” Activated
Figure 22
ELECTRICAL WIRING TO SOE ENCLOSURE
SECTION VIEW DAMPER OPEN
DAMPER SOLENOID
4
FENWALL DETECTOR
1
2
DAMPER BLADE
STOPS
DAMPER BLADE STOPS
DAMPER BLADE STOPS
THERMOSTAT
THERMOSTAT J-BOX
DAMPER BLADE
120V/1/60 - 3 AMPS - WIRE EACH SOE IN PARALLEL.
THREE (3) WIRES TO EACH SOE ENCLOSURE LOCATED
AT EACH EXHAUST DUCT COLLAR ON EVERY HOOD
SIDE VIEW DAMPER OPEN POSITION
SOE ENCLOSURE
ARRANGEMENT "T" FIRE DAMPER:
DAMPER RETAINING
(DAMPER OPEN POSITION)
POSITION.
PIN BACK BACK STOP
CLIP
FIRE DAMPER PIN
SOLENOID
SOLENOID PIN
DAMPER RETAINING
CLIP - DOWN
ON TOP OF
VENTILATOR
SPRING
RETAINING
POST
DAMPER CLOSURE
SPRING
BX CONDUIT
TO J-BOX
TERMINAL BLOCKS