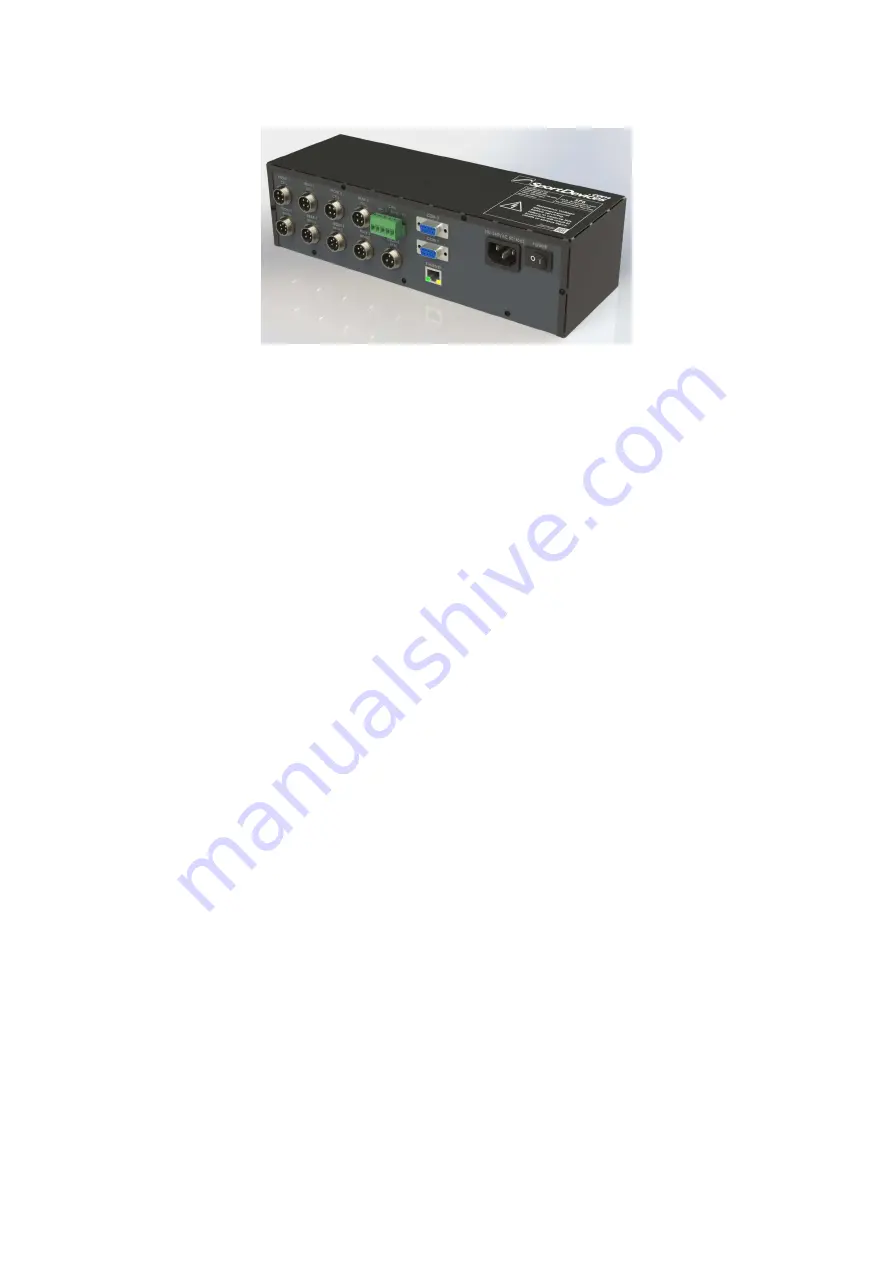
SP6 Installation and Setup V0.91
Sportdevices © 2019
20/NOV/2019
SP6 INSTALLATION AND SETUP MANUAL
Contents
1
S
portDevices End User Software License & Warranty Disclaimer ........................................ 2
2
General Safety Instructions
.................................................................................................... 3
2.1
SAFETY: When Working Inside Your Device ............................................................. 3
2.2
SAFETY: General Power Safety ................................................................................ 4
2.3
SAFETY: If Your Device Gets Wet ............................................................................. 4
2.4
SAFETY: If You Drop or Damage Your Equipment ..................................................... 5
2.5
Protecting Against Electrostatic Discharge ................................................................. 5
2.6
Dynamometer Important Safety Tips
.............................................................................. 6
2.7
Technical Specs
............................................................................................................ 6
2.7.1
Input Specs
.............................................................................................................. 6
2.7.2
Output Specs
........................................................................................................... 7
2.7.3
Connectivity Specifications
........................................................................................ 7
3
SP6 Installation .................................................................................................................. 8
3.1
Introduction
................................................................................................................ 8
3.2
Dynamometer Installation.
............................................................................................ 8
3.2.1
Vehicle dynamometers
............................................................................................. 8
3.2.2
2WD single / double roller dynamometer
.................................................................... 9
3.2.3
Single roller AWD dynamometer:
............................................................................. 10
3.2.4
Twin roller AWD dynamometer:
............................................................................... 11
3.2.5
HUB-2 Dynamometer
.............................................................................................. 12
3.2.6
HUB-4 Dynamometer
.............................................................................................. 13
3.2.7
Engine Test bed dyno installation
............................................................................. 14
3.3
Proposed installation parts.
......................................................................................... 15
3.4
SP6 Connections
........................................................................................................ 16
3.4.1
SP6 Front Panel
...................................................................................................... 16
3.4.2
SP6 Rear Panel
....................................................................................................... 18
4
SportDyno Quick Setup Guide
.............................................................................................. 22
4.1
Inertial Configuration: Roller / Flywheel
........................................................................ 22
4.2
Ratio Configuration
.................................................................................................... 23
4.3
Load Cell Calibration
................................................................................................... 24
4.4
Speed Control Configuration (SP4-SP6)
......................................................................... 25