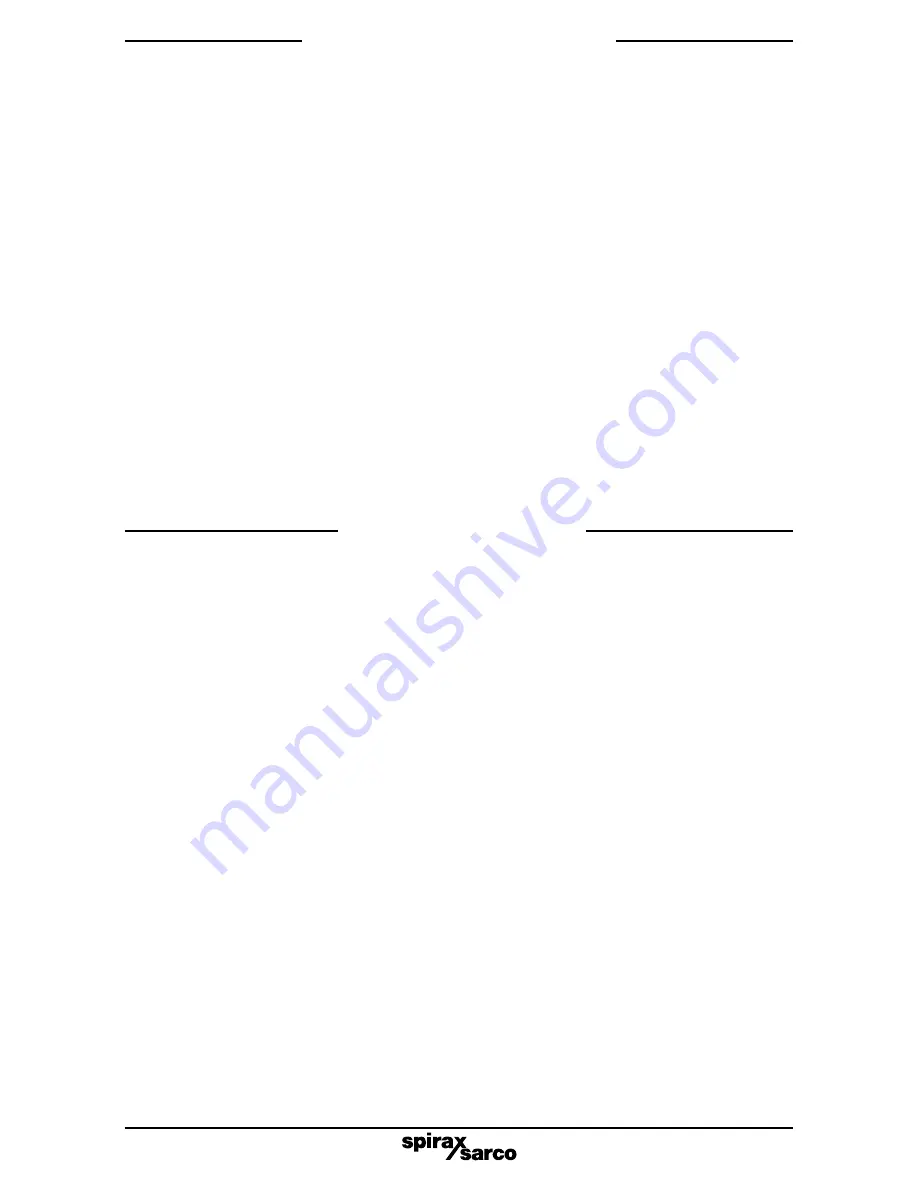
IM-P150-07
ST Issue 4
8
5. Operation
The TD120 is a thermodynamic steam trap which uses a disc to control the release of
condensate and to trap steam. The trap cycles open and closed to discharge condensate,
close to steam temperature, and closes tight between discharges.
The disc, which is the only moving part, rises and falls in response to dynamic forces produced
by the partial re-evaporation (flashing) of hot condensate. Cool condensate, air and other
non-condensible gases enters the trap through the central orifice, lifts the disc, and discharges
through the outlet orifice. When the condensate approaches steam temperature, a portion of it
flashes as it enters the trap. The flash steam passes at high velocity over the underside of the
disc and collects in the control chamber above. The resulting pressure imbalance, forces the
disc downward onto the seating surfaces, stopping the flow. The trap remains tightly closed
until the loss of heat through the trap body lowers the control chamber pressure, allowing the
inlet pressure to raise the disc and repeat the cycle.
4.1 Commissioning with particular reference to venting air
Initial start-up can take several hours (or days) to bring the system to normal operating
pressure and temperature. Even if the trap has replaced another trap while the main system
has remained running, it may still be necessary to vent air from the drop leg. If the trap is
some distance from stop valve '
A
' (Figure 2), it could be possible to air lock the pipework
between valve '
A
' and the trap (i.e. the trap closes to air and does not readily allow steam to
enter the pipework). To overcome this on start-up the following procedure should be adopted.
With the stop valve '
B
' closed, drain valve '
C
' open, slowly and partially open stop valve '
A
'.
This will discharge the air, condensate and any pipe debris.
Valve '
C
' should then be fully closed, and valves '
A
' and '
B
' slowly opened to the fully open
position. When the trap is more than 2 m (6 ft) away from the vertical drain leg, a suitable drop
leg at the inlet to the trap can improve its service life by ensuring that the trap does not see a
mixture of steam and condensate.
Important note
After the trap has been in service at normal operating pressure and temperature for
24 hours, it is essential that the cover nuts be retightened (see Table 1, page 11). This will
ensure the correct compression of the gasket under service conditions.
4. Commissioning