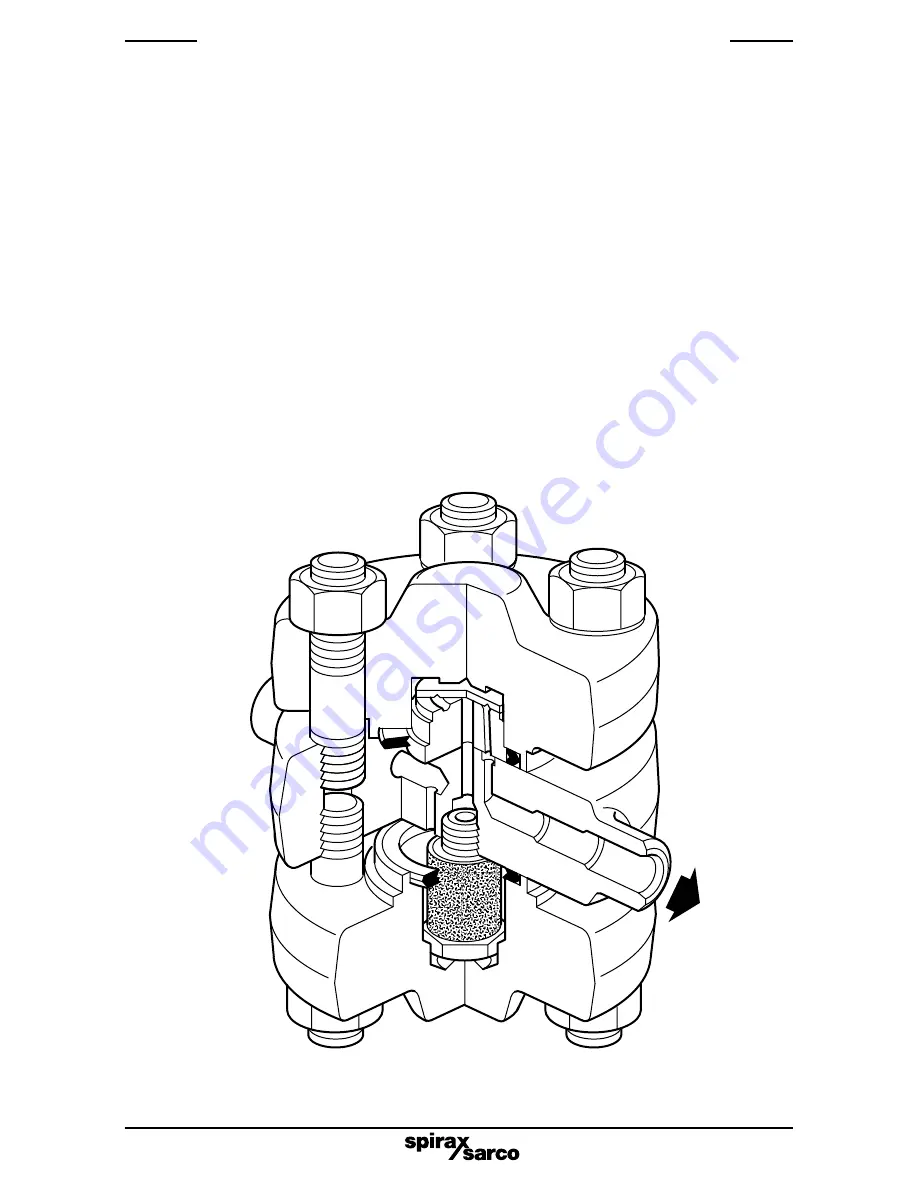
IM-P150-07
ST Issue 4
5
2. General product information
2.1 General description
The TD120 is a maintainable medium high pressure thermodynamic steam trap with integral
strainer designed specifically for steam mains drainage applications up to 250 bar g
(3 625 psi g).
Standards
This product fully complies with the requirements of the European Pressure Equipment
Directive 97/ 23 / EC.
Certification
This product is available with certification to EN 10204 3.2.
Note:
All certification / inspection
requirements must be stated at the time of order placement.
Note:
For additional information see Technical Information Sheet TI-P150-01.
2.2 Sizes and pipe connections
½
",
¾
" and 1" Butt weld ends to suit Schedule 160 pipe.
½
",
¾
" and 1" Socket weld ends to ANSI B 16.11 Class 6000.
DN15 and DN25 standard integral flange DIN 2549 PN250.
DN15, DN20 and DN25 standard integral flanges: ANSI 600, ANSI 900, ANSI 1500,
DIN 2547 PN100 and DIN 2548 PN160.
Fig. 1 Thermodynamic steam trap