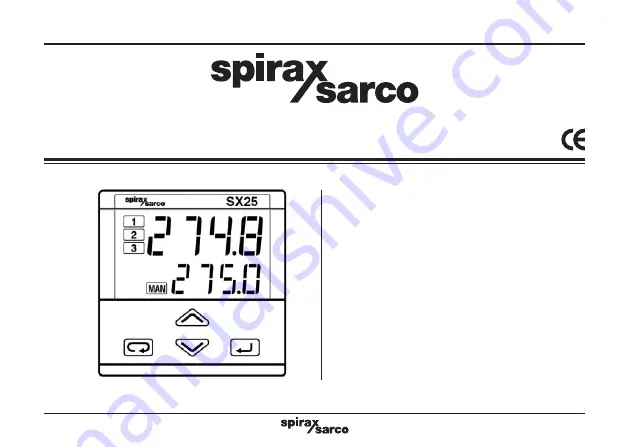
IM-P323-25 CH Issue 3
1
SX25 Series Process Controller
Installation and Maintenance Instructions
IM-P323-25
CH Issue 3
3231450/3
1. Safety Information
2. Installation
3. Electrical connections
4. Configuration
5. Operations
6. Commissioning examples
7. Automatic tuning
8. Technical specifications
Printed in the UK
© Copyright 2003