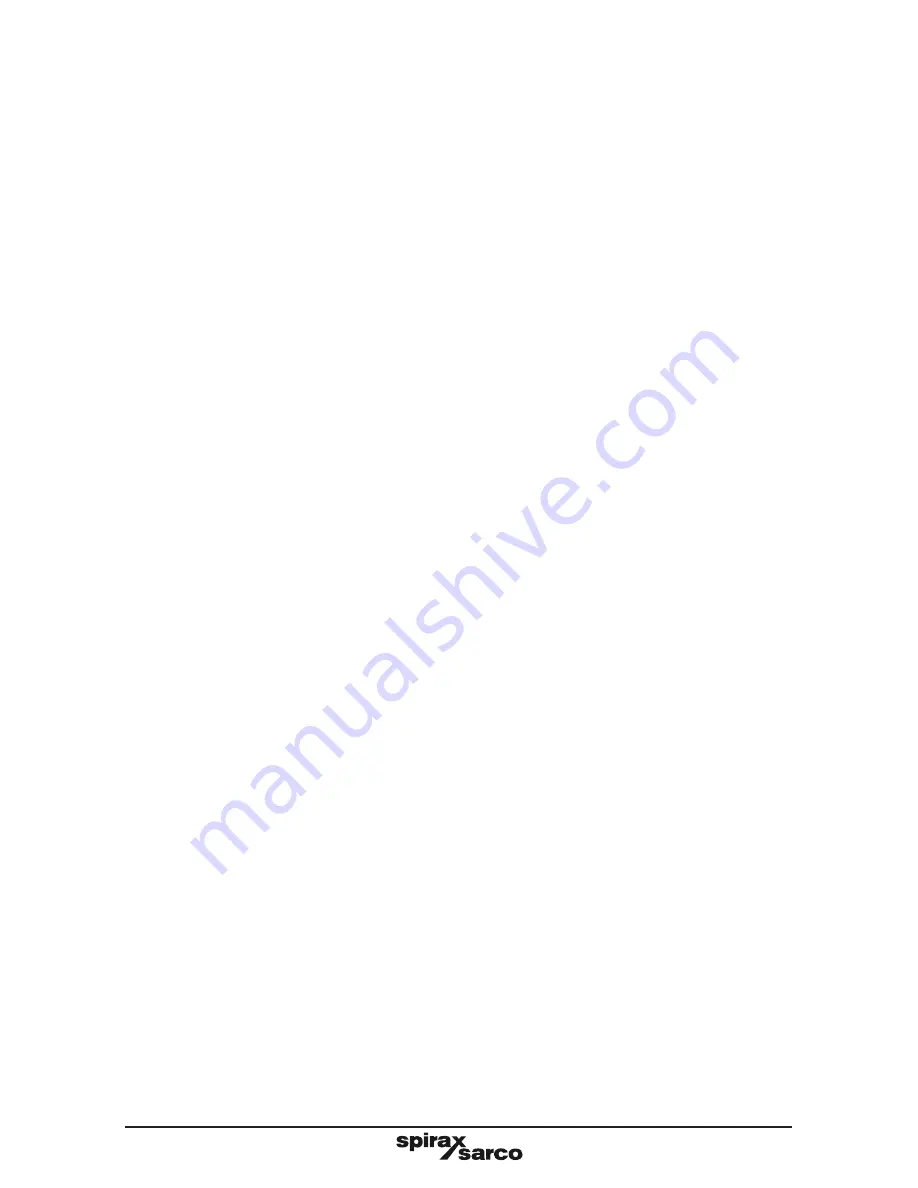
IM-P493-01
EMM Issue 2
7
3. Installation
Note: Before actioning any installation observe the 'Safety information' in Section 1.
It is important that installation should only be carried out by qualified, experienced personnel,
who are familiar with the fitting of Steam Jet Thermocompressors and have read and
understood all the instructions in these Installation and Maintenance Instructions.
3.1 Suction piping and orientation - Installation considerations:
3.1.1
Spirax Sarco SJT Steam Jet Thermocompressors can be installed and operated in any
position but, the preferred orientation is to have the ejector discharge connection
pointing virtically downwards.
In cases where the motive steam supply is likely to be wet, an installation which has
the thermocompressor discharge connection pointing upwards must be avoided.
Further, when deciding on the orientation of a thermocompressor, remember that when
the unit is shutdown, condensate is likely to build-up around the low points within the
ejector body, which could influence the corrosion rate and cause operational problems
during start -up. If the ejector discharges vertically downwards, full drainage of the unit
will be achieved after shutdown and these possible sources of problems eliminated.
3.1.2
The connecting suction pipework should be sized and installed so as to provide as little
resistance to flow as possible. The effect of pipeline frictional losses must be considered
when specifying the performance of an SJT Steam Jet Thermocompressor.
It is recommended that the connecting pipework should have at least the same bore
as the mating unit flange. However, if this is not possible, slow tapers should be installed,
preferably 6 to 10 pipe diameters away from the unit.
We strongly recommend that the Installation Engineer performs velocity calculations
to size the suction pipework and does not simply make the piping the same size as the
suction connection on the thermocompressor, without performing a check.
3.1.3
The thermocompressor should be located as close as possible to the source of the low
pressure water vapour that forms the suction gas - thus keeping the piping as short
and as straight as possible.
3.1.4
The suction line should lead downwards to the connection on the thermocompressor.
This will avoid condensate from the motive steam line entering the plant during start-up.
The best layout would be to have the ejector suction branch below the point where the
vacuum is required. The connecting suction pipework would then come down and turn
through a 90
º
bend, immediately before the ejector suction branch. We appreciate that
this is an ideal situation and may not be achieved in practice but, any potential problems
due to liquid build-up are eliminated because of the natural drainage of this type of
layout.
3.1.5
If flow reversal into the suction branch must be prevented, a check valve should be
installed in the suction piping, adjacent to the thermocompressor. The resistance to
flow offered by such a valve should have been taken into account when the
thermocompressor was specified.
3.1.6
The suction piping must be free of any loops in the vertical plane. These are potential
sources of liquid and solids collection points and they can cause serious operational
problems - particularly if the suction gas contains droplets, dust or vapour near its
saturation point.
3.1.7
An isolation valve should be fitted in the suction line, bearing in mind that this valve
will present an additional resistance to flow. We strongly recommend the use of full
bore valves (e.g. Ball valves, Gate valves).
Summary of Contents for Steam Jet Thermocompressor
Page 16: ...IM P493 01 EMM Issue 2 16...
Page 17: ...IM P493 01 EMM Issue 2 17...