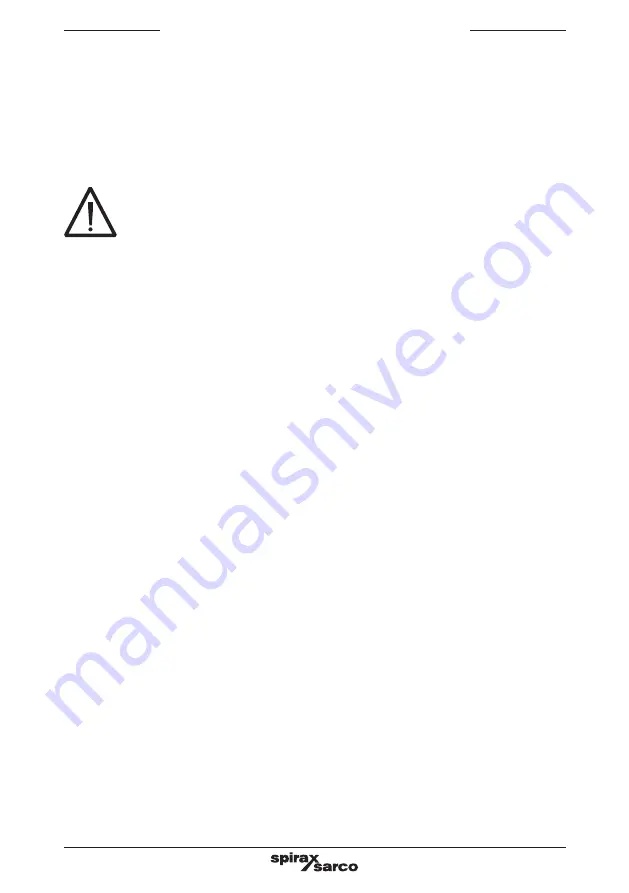
IM-P358-26
CH Issue 1
2
Safe operation of this product can only be guaranteed if it is properly installed,
commissioned, used and maintained by qualified personnel (see Section 1.13) in
compliance with the operating instructions. General installation and safety instructions
for pipeline and plant construction, as well as the proper use of tools and safety
equipment must also be complied with.
See separate Installation and Maintenance Instructions for the control valve.
If the actuator is handled improperly or not used as specified,
the resultant may:
-
cause danger of the life and limb of the third party,
-
damage the actuator and other assets belonging to the owner,
-
hinder the performance of the actuator.
1.1 Wiring notes
Every effort has been made during the design of the actuator to ensure the safety of
the user, but the following precautions must be followed:
i
)
Maintenance personnel must be suitably qualified in working with equipment
containing hazardous live voltages.
ii
)
Ensure correct installation. Safety may be compromised if the installation of the
product is not carried out as specified in this manual.
iii
)
Isolate the actuator from the mains supply before opening the unit.
iv
)
The actuator is designed as an installation category
II
product, and is reliant on
the building installation for overcurrent protection and primary isolation.
v
)
Wiring should be carried out in accordance with IEC 60364 or equivalent.
vi
)
Fuses should not be fitted in the protective earth conductor. The integrity of the
installation protective earth system must not be compromised by the disconnection
or removal of other equipment.
vii
)
A disconnecting device
(
switch or circuit breaker
)
must be included in the
building installation. This must be in close proximity to the equipment and within
easy reach of the operator.
-
There must be a 3 mm contact separation in all poles.
-
It must be marked as the disconnecting device for the actuator.
-
It must not interrupt the protective earth conductor.
-
It must not be incorporated into a mains supply cord.
-
The requirements for the disconnecting device are specified in IEC 60947
-
1
and IEC 60947
-
3 or equivalent.
viii
)
The actuator must not be located in such a way that the disconnecting device is
made difficult to operate.
1. Safety information
Summary of Contents for AEL5 Series
Page 27: ...IM P358 26 CH Issue 1 27...
Page 28: ...IM P358 26 CH Issue 1 28...