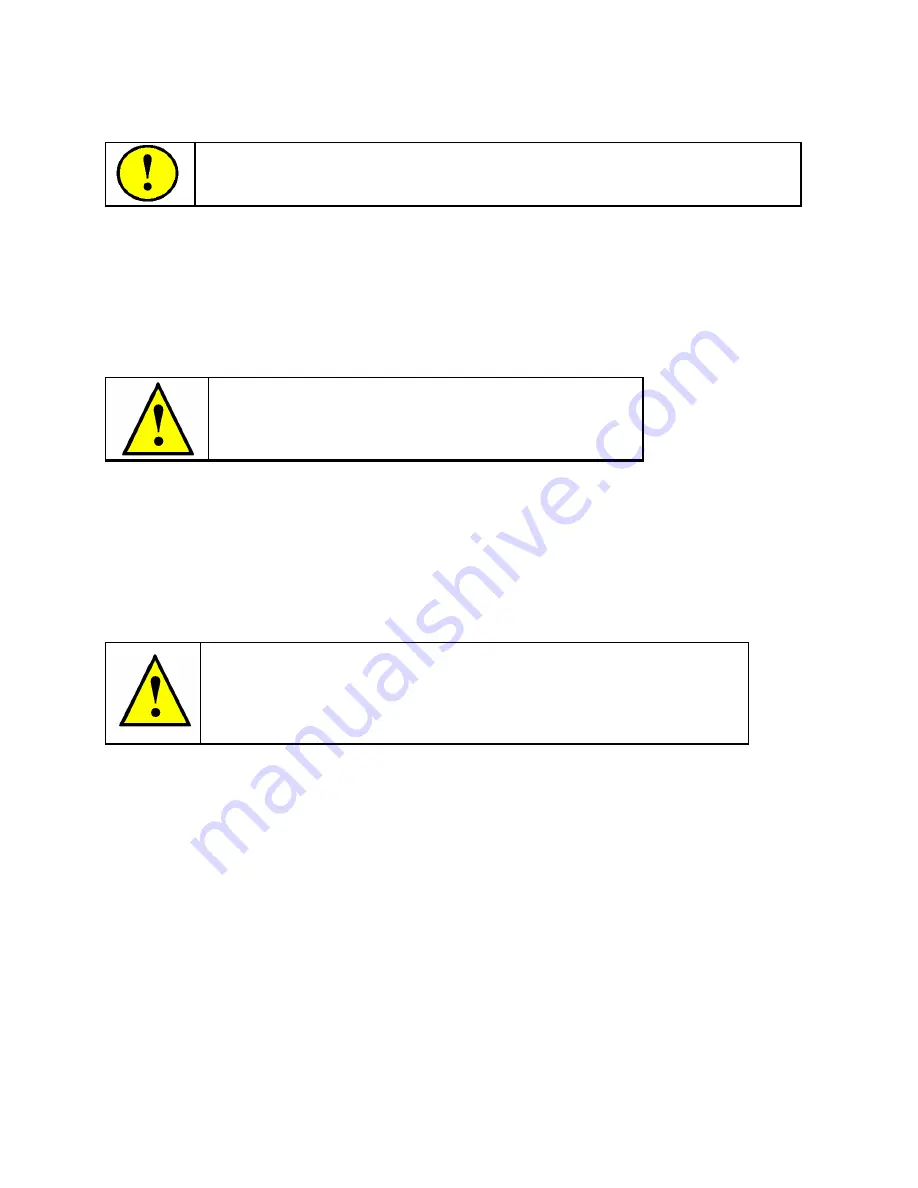
SPI Supplies
10
SPI-DRY Critical Point Dryer
2.4.4
Instrument Functionality Signs
CAUTION
Extreme care should be taken during transfer to prevent surface drying of the specimen.
Should air drying occur, the specimen will be irreversibly damaged.
Figure 2.3 - Typical Warning sign as shown in this Manual
This typical sign applies to cautions where there is a risk to the functionality of equipment due to
incorrect operation. These cautions or warnings will be contained in a box and be accompanied by a
circular warning symbol as shown in Figure 2.3.
2.4.5
Serious Damage to Instruments
WARNING
Do NOT depress button “P” as this will change the program.
Figure 2.4 - Typical Warning sign as shown in this Manual
This typical caution sign is used where serious damage will be caused by incorrect operation of
instrumentation. They will follow the same form as functionality warnings but with a triangular warning
symbol as shown in Figure 2.4.
2.4.6
Hazard to Operator
WARNING
HAZARD TO HEALTH!
Risk of asphyxiation in poorly ventilated rooms.
As carbon dioxide is heavier than air, the concentration of exhaust gas will be
greater at ground level and the oxygen concentration correspondingly reduced.
Figure 2.5 - Typical Warning as shown in this Manual
These warnings will generally occur in relevant installation and maintaining sections where there exists
a potential hazard to the engineer working on the instrument. They will take the form of the triangular
warning symbol accompanied by an international warning sign and bold type lettering beginning with
“WARNING-HAZARD TO HEALTH!”
as shown in Figure 2.5.