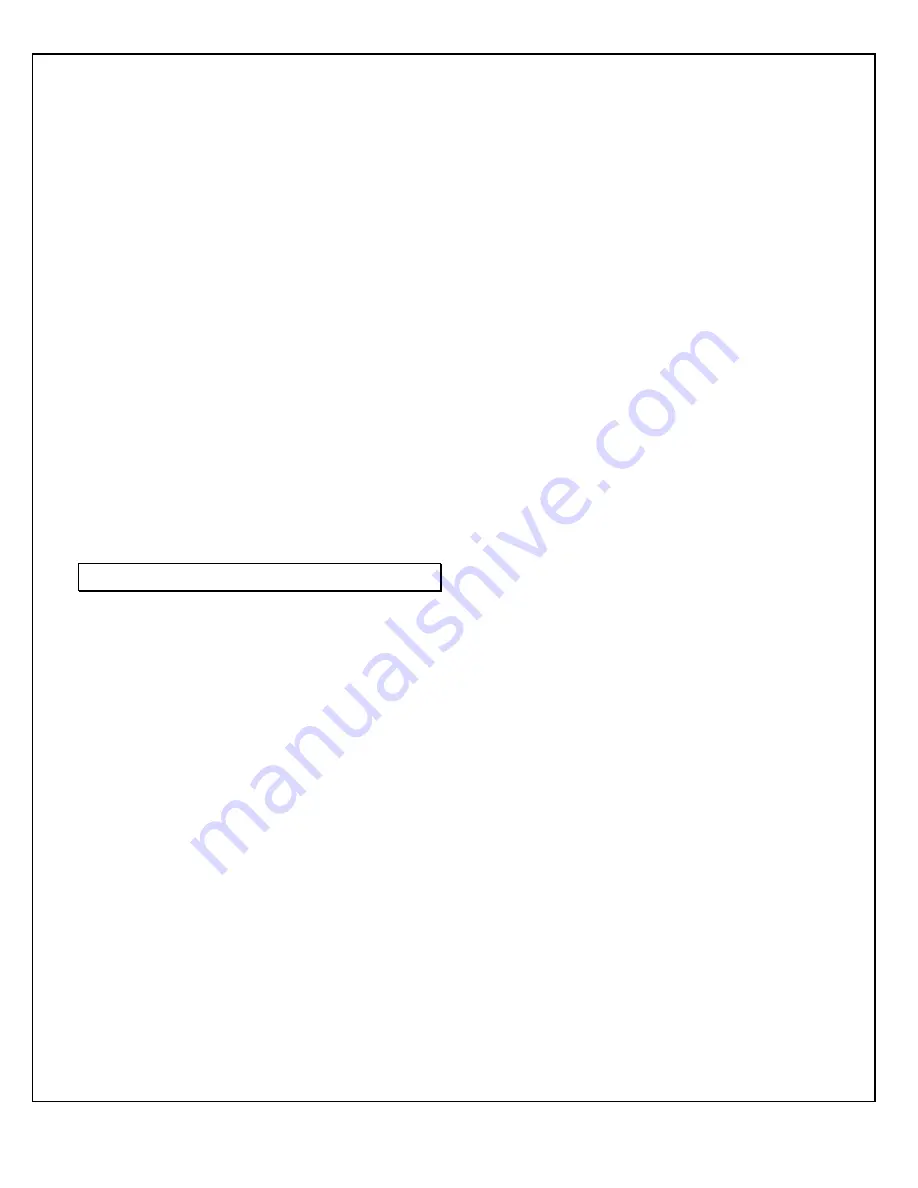
EPM/SMS MANUAL
15
118026-001 REV K
Chapter 4
P
RINCIPLES
O
F
O
PERATION
he EPM/SMS Series of high voltage power supplies
utilizes sophisticated power conversion technology.
Advanced analog and power conversion techniques
are used in the EPM/SMS series. The intention of the
Principles of Operation is to introduce the basic function
blocks of the EPM/SMS series power supply. For details
on a specific circuit, consult Spellman’s Engineering
Department.
The EPM/SMS series power supply is basically an DC to
DC power converter. Within the power supply,
conversions of DC to high frequency AC, then to high
voltage DC take place.
Typical EPM/SMS series power supplies comprise a few
basic building blocks. These are: 1) High frequency
quasi-resonant inverter, 2) High voltage transformer and
rectifier circuits, and 3) Control and monitoring circuits.
The following is a brief description of each building
block.
WARNING
The energy levels used and generated by the
power supply can be lethal! Do not attempt to
operate the power supply unless the user has a
sufficient knowledge of the dangers and hazards
of working with high voltage. Do not attempt to
approach or touch any internal or external
circuits or components that are connected or
have been connected to the power supply. Be
certain to discharge any stored energy that may
be present before and after the power supply is
used. Consult IEEE recommended practices for
safety in high voltage testing #510-1983.
4.1 High Frequency Inverter
The EPM/SMS series uses a resonant converter operating
in a zero current switching, resonant flyback and forward
converter topology. MOSFET transistors switch DC
voltage to the resonant circuit. Typical operating
frequency is in the range of 30-35kHz depending on
model. Control of the resonant circuit output is done by
the low voltage control circuits. The resonant circuitry
consists of a resonant inductor and step-up transformer.
4.2 High Voltage Circuits
The high voltage transformer is a step-up type. The
secondary of the high voltage transformer is connected to
the high voltage rectifier circuit. The rectifier circuit will
vary depending upon the rated output voltage. For lower
output voltage, a full bridge or doubler circuit is used.
For higher voltages, a half wave Cockroft-Walton
multiplier is used. A feedback signal is generated by the
high voltage resistor divider. This feedback signal is sent
to control circuits to provide voltage regulation and
monitoring. A current sense resistor is connected at the
low voltage end of the rectifier circuit. The circuit sense
signal is sent to the control circuits to provide current
regulation and monitoring.
In the SMS series, an auxiliary voltage sense signal is
generated by the overvoltage protection feedback resistor.
This is used to provide overvoltage protection.
The high voltage rectifier output is connected to an R-C
type filter to reduce high frequency ripple components.
The filter is then connected to the output limiting resistors.
These resistors limit the peak surge current in the event an
arc or discharge occurring. The limiting resistor output is
connected to the output cable or connector provided.
4.3 Control Circuits
Control circuits are used for regulation, monitoring, pulse-
width, control, slow-start and inhibit control. Feedback
signals are calibrated and buffered via general purpose
OP-AMPS. Pulse width control is accomplished by a
typical PWM type control I.C. Logic enable/disable is
provided by a logic gate I.C. Regulators ge/- 15V
and 10VDC.
4.4 Options
Due to the variations of models and options provided in
the EPM/SMS series, details of actual circuits used may
differ slightly from above descriptions. Consult
Spellman’s Engineering Department for questions
regarding the principles of operations for the EPM/SMS.
T