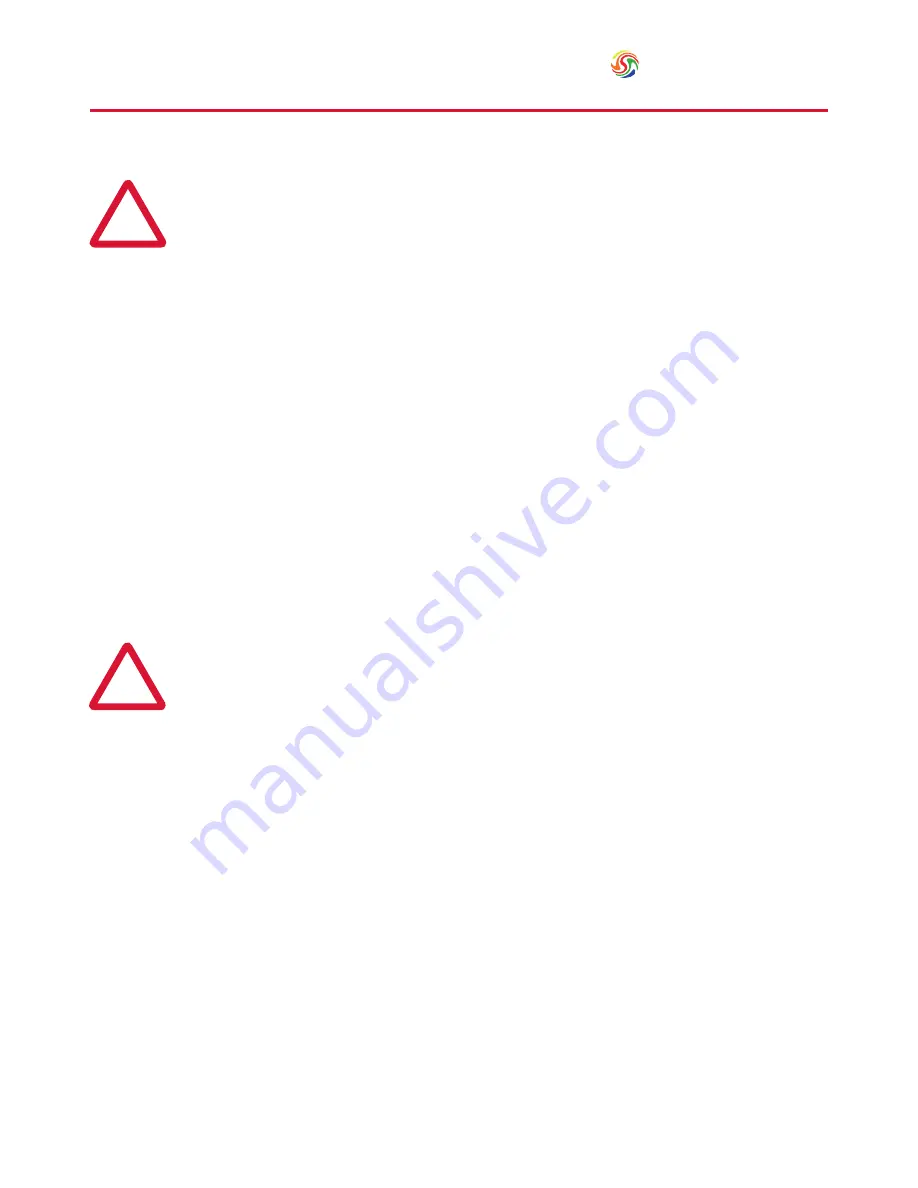
10
Spectrum
TM
Membrane Installation,
Removal & Replacement
Installing and replacing membranes in the membrane housings is an easy process if the correct information
and tools are at hand. Refer to the following instructions when removing or replacing membrane elements:
NOTE:
All pressure gauges must read zero before proceeding. Before attempting, disconnect
the power from the system and bleed all water pressure from the system.
1. Remove the black end cap from the top of the membrane housing. This is done by removing the yellow
locking clip and then the white snap ring on the membrane housing end.
2. Remove the replacement membrane element(s) from the shipping box; the membrane(s) should be
contained within a plastic oxygen barrier bag.
3. Cut the bag open as close as possible to the seal at one end of the bag, so the bag may be re-used if
necessary.
4. Make sure that all parts are clean and free from dirt. Examine the brine seal and permeate tube for
nicks or cuts.
5. Flow directions should be observed for installation of each element into their respective membrane
housings.
NOTE:
Wear gloves for the following steps in order not to contaminate the membrane.
Replacing the Membrane Element
NOTE:
The brine seal must be in the same position for each membrane element housing.
The brine seal is a rubber seal that protrudes on one side of the membrane and is always on
the feed side of the membrane element. On SPECTRUM Systems the brine seal should be
on the top side of the membrane housing.
1. Remove one membrane element at a time from the top of the membrane housings. Long nose pliers
may be necessary to pull the old membrane element out of the membrane housing.
2. Lubricate the brine seal with a non-petroleum based lubricant. Do not use a petroleum-based lubricant.
3. Install membranes with brine seal location depicted (
Figure 2).
4. With a smooth and constant motion, push the membrane element into the housing so the brine seal
enters the housing without coming out of the brine seal groove.
5. Once the membrane has been fully inserted into housing re-install black end plug, white snap ring
(ensure the white snap ring is fully seated all the way around end plug) and yellow locking clip.
6. Reconnect any fittings that may have been disconnected when the membrane housing were
disassembled.
7. To start-up the system refer to the initial start-up section of this manual.
!
!