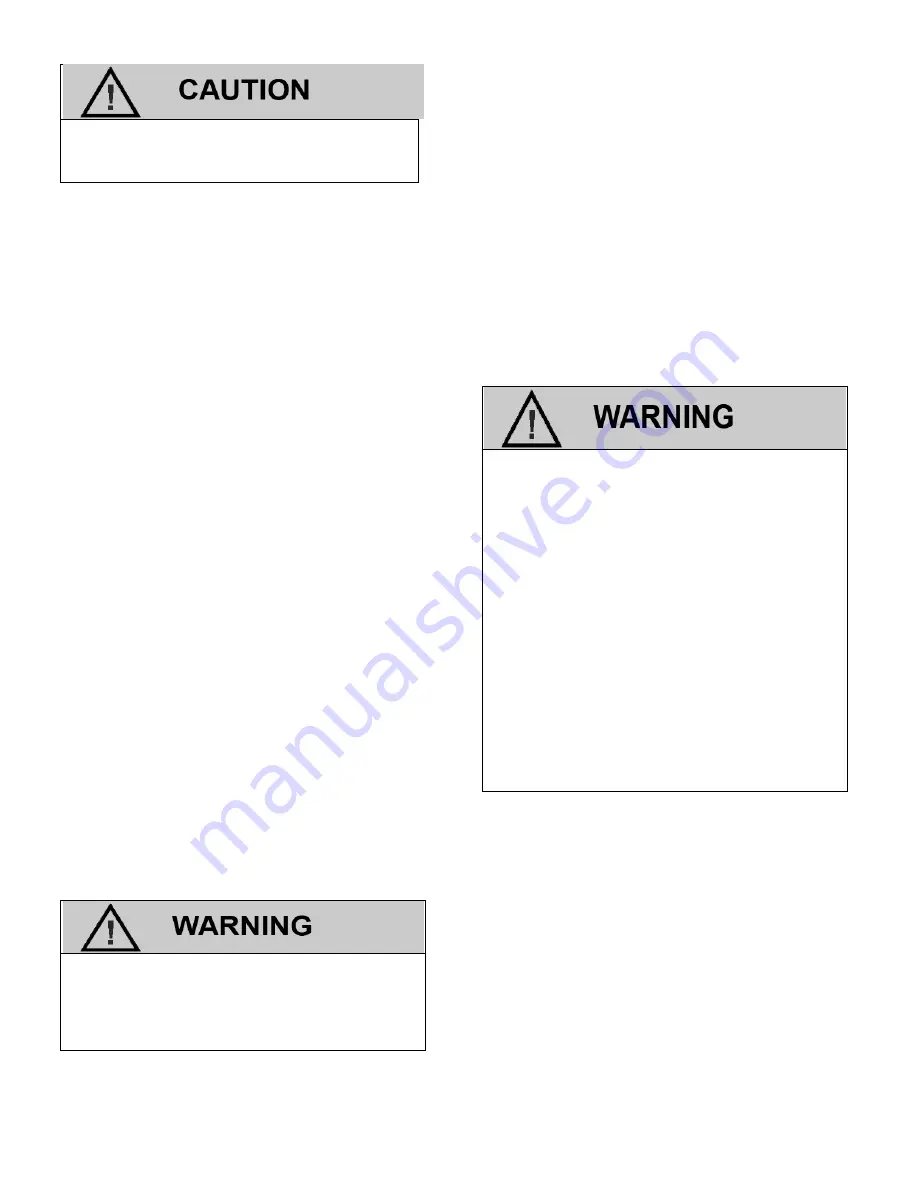
249
The coolant may be hot. Use caution when
removing hose(s) to prevent contact.
3. Remove clamps from each end of the Hose
and remove Hose.
INSTALLATION PROCEDURE
IMPORTANT
Coolant hoses are speci
fi
cally designed for their
application. DO NOT use hose material or length
other than the OEM speci
fi
ed parts. DO NOT mix
the inlet or outlet ends of the Hose when reinstal-
ling.
1. Slide Clamps over each end of the Hose.
2.
Insert Port Fittings into each end of the Hose.
3. Slide Hose Clamp to a position approximately
½” from the end of the Hose and tighten.
4.
Re
fi
ll with coolant.
5.
Start engine and let run until it reaches operat-
ing temperature.
6.
Check for leaks. If leaks are detected, make
repairs.
7. Stop engine and allow to cool. Check coolant
level and add coolant as necessary.
XXI. FUEL VAPOR HOSE
REMOVAL PROCEDURE
1.
Relieve the LPG fuel system pressure. Refer
to
XVIII. LPG FUEL SYSTEM PRESSURE
RELIEF.
2. Disconnect negative battery cable.
3. Remove Retaining Clips securing Port Fittings
on both ends and remove with Hose attached.
4. Remove Hose Clamps.
5. Remove Port Fittings from Hose.
Residual vapor pressure will be present in
the fuel system. Ensure the work area is
well ventilated before disconnecting any
fuel line.
IMPORTANT
Hoses are designed for specific applications. DO
NOT use Hose material or length other than spe-
cified by the OEM. DO NOT mix the inlet or outlet
ends of the Hose when reinstalling.
INSTALLATION PROCEDURE
1.
Slide Hose Clamps over each end of the Fuel
Hose.
2.
Insert Port Fittings into each end of the Hose.
3. Slide each Hose Clamp to a position approx-
imately ½” from the end of the Hose and
tighten.
4.
Lightly lubricate new O-ring with
Vaseline or
petroleum jelly prior to installation.
Contamination of the HEGO sensor can re-
sult from the use of an inappropriate RTV
sealer or silicone spray products. Do not use
silicone sprays or hoses which are assem-
bled using silicone lubricants. Always use
“oxygen sensor safe” RTV sealant for repair
procedures. Silicon contamination will cause
a high but false HEGO signal voltage (rich
exhaust indication). The ECM will then re-
duce the amount of fuel delivery to the
engine, causing a severe driveability prob-
lem. If silicone contamination is suspected,
remove and visually inspect the sensor ele-
ment. If contaminated, the portion of the
sensor exposed to the exhaust stream will
have a white powdery coating. Always be
sure to eliminate the cause of contamination
before replacing the sensor.
5. Reinstall Hose at both ends and secure using
Retaining Pins.
6. Reconnect negative battery cable.
7. Open LPG tank valve.
8. Turn Key to the ON position for several
seconds, then turn back to OFF.
Check for
leaks at the inlet and outlet
fi
ttings using a
soapy solution or an electronic leak detector.
If leaks are detected, make repairs.
9. Start engine and check for leaks.
10.
If a DTC code is found, refer to the Electrical
Section for further diagnosis.
Summary of Contents for 3.0L GM
Page 4: ...4 ...
Page 5: ...5 General Information ...
Page 9: ...9 Maintenance ...
Page 16: ...16 ...
Page 17: ...17 LPG Fuel System ...
Page 18: ...18 LPG FUEL SYSTEM OPERATION ...
Page 25: ...25 LPG Closed Loop Schematic ...
Page 26: ...26 ...
Page 27: ...27 LPG System Diagnosis ...
Page 35: ...35 Fuel Symptom Diagnostics ...
Page 51: ...51 Electrical Section ...
Page 52: ...52 ...
Page 53: ...53 DST Diagnostic Scan Tool ...
Page 59: ...59 Select the USB button then click the OK box Click on the Search attached device box ...
Page 67: ...67 When connected the live data stream appears in the Value column ...
Page 78: ...78 ...
Page 80: ...80 ...
Page 81: ...81 Engine Wire Schematic ...
Page 82: ...82 2011 3 0L GM Engine IMPCO Emission Certified LPG Fuel System ...
Page 83: ...83 ...
Page 84: ...84 ...
Page 85: ...85 Engine Wire Harness Repair ...
Page 89: ...89 Diagnostic Trouble Codes DTCs ...
Page 93: ...93 ...
Page 101: ...101 ...
Page 105: ...105 ...
Page 109: ...109 ...
Page 119: ...119 ...
Page 129: ...129 ...
Page 133: ...133 ...
Page 137: ...137 ...
Page 141: ...141 ...
Page 145: ...145 ...
Page 161: ...161 ...
Page 165: ...165 ...
Page 169: ...169 ...
Page 173: ...173 ...
Page 201: ...201 ...
Page 209: ...209 ...
Page 213: ...213 ...
Page 217: ...217 ...
Page 221: ...221 ...
Page 225: ...225 ...
Page 229: ...229 ...
Page 237: ...237 Servicing the Fuel System ...
Page 254: ...254 ...
Page 255: ...255 LPG Parts Diagram ...
Page 256: ...256 THROTTLE BODY ASSEMBLY ...
Page 258: ...258 FUEL RAIL INJECTORS ...
Page 260: ...260 REGULATOR ASSEMBLY ...
Page 262: ...262 HOSE ASSEMBLIES COOLANT VACUUM FUEL ...
Page 264: ...264 THERMOSTAT HOUSING ...
Page 266: ...266 ENGINE CONTROL MODULE ...
Page 267: ...267 ENGINE CONTROL MODULE Item Description Qty IMPCO Part Number 1 ECM Liugong 1 A11 173 ...
Page 268: ...268 SENSORS 4 1 3 6 5 2 7 ...
Page 270: ...270 DISTRIBUTOR ...
Page 272: ...272 FUSE BOX BRACKET ...
Page 274: ...274 IGNITION COIL ...
Page 275: ...275 IGNITION COIL Item Description Qty Part Number 1 Coil Ignition 1 7245530 ...
Page 276: ...276 MANIFOLDS ...
Page 278: ...278 WIRE HARNESS FUSES FUSE BOX COVER Fuse Box Layout 4 ...
Page 280: ...280 PCV VENT VALVE ...
Page 282: ...282 MISCELLANEOUS ENGINE ...
Page 284: ...284 ALTERNATOR ...
Page 286: ...286 STARTER ...
Page 291: ...291 ...
Page 292: ...292 3 0L UPPER ...
Page 294: ...294 3 0L LOWER ...
Page 298: ...298 ...
Page 299: ...299 Labor Time Guide ...
Page 317: ...317 Definitions ...
Page 322: ...322 ...
Page 323: ...323 Appendix ...
Page 327: ...327 DTC SPN FMI Chart ...