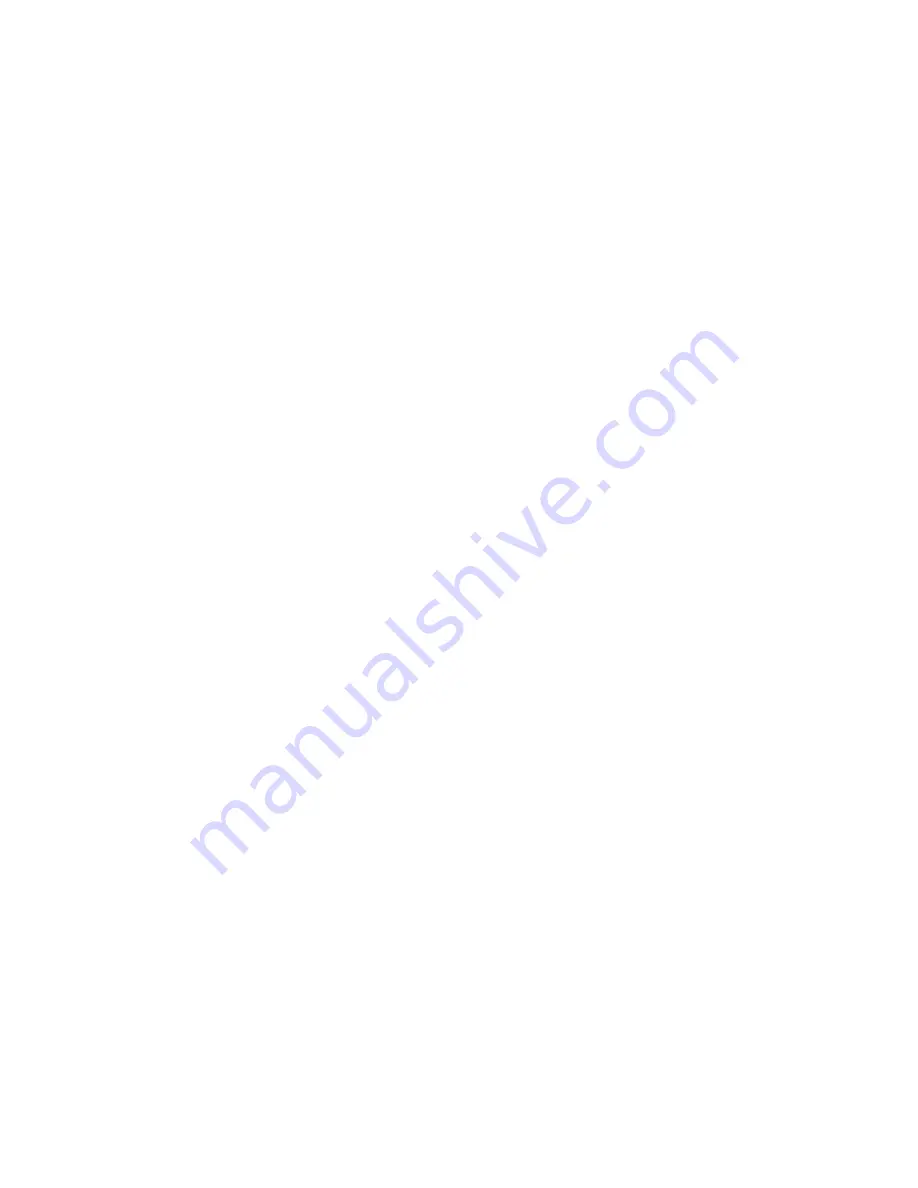
Contents
Overview And Specifications ......................................................... 7
General Features And Benefits.......................................................................................................... 7
Detailed Specifications ....................................................................................................................... 9
Table 1.1. Electrical specifications—module .................................................................................................. 9
Table 1.2. Physical specifications ................................................................................................................... 10
Table 1.3. Environmental specifications ........................................................................................................ 10
Installing And Wiring Your Module ............................................. 11
Avoiding Electrostatic Damage........................................................................................................ 12
Determining Power Requirements .................................................................................................. 12
Table 2.1. Backplane current consumed ........................................................................................................ 13
Selecting a Rack Slot ........................................................................................................................ 13
Setting your Jumpers ....................................................................................................................... 13
Inserting Your Module Into The Rack ........................................................................................... 14
Wiring Your Module ........................................................................................................................ 15
Terminal Block Wiring ................................................................................................................................... 17
Labeling And Re-Installing The Terminal Block
(if it is removed) .......................................................................................................................... 18
Things To Consider Before Using
Your Module ............................................................................. 19
Module ID Code ................................................................................................................................ 19
Table 3.1 Module ID codes .............................................................................................................................. 19
Module Addressing ........................................................................................................................... 20
Figure 3.1 .......................................................................................................................................................... 20
Operating Modes .............................................................................................................................. 22
Table 3.2 Module operating modes ............................................................................................................... 22
Input Configurations ........................................................................................................................ 22
Gate Modes ........................................................................................................................................ 24
Channel Turn-On,
Turn-Off, and
Reconfiguration Times ............................................................................................................... 24
Response to Slot Disabling ............................................................................................................... 24
Channel Configuration, Data,
and Status .................................................................................. 27
Configuring Each Input Channel ................................................................................................... 27
Output Register - Scale and Limit Data Values ............................................................................. 34
Input Registers - Channel Data ...................................................................................................... 37
Summary of Contents for 1746sc-CTR4
Page 2: ......
Page 4: ......
Page 26: ...26 SLC500 50KHzCounter FlowmeterInputModule ...
Page 42: ...42 SLC500 50KHzCounter FlowmeterModule ...
Page 50: ...50 SLC500 50KHzCounter FlowmeterModule ...
Page 63: ...AppendixA FloatingPointRateMode 63 ...