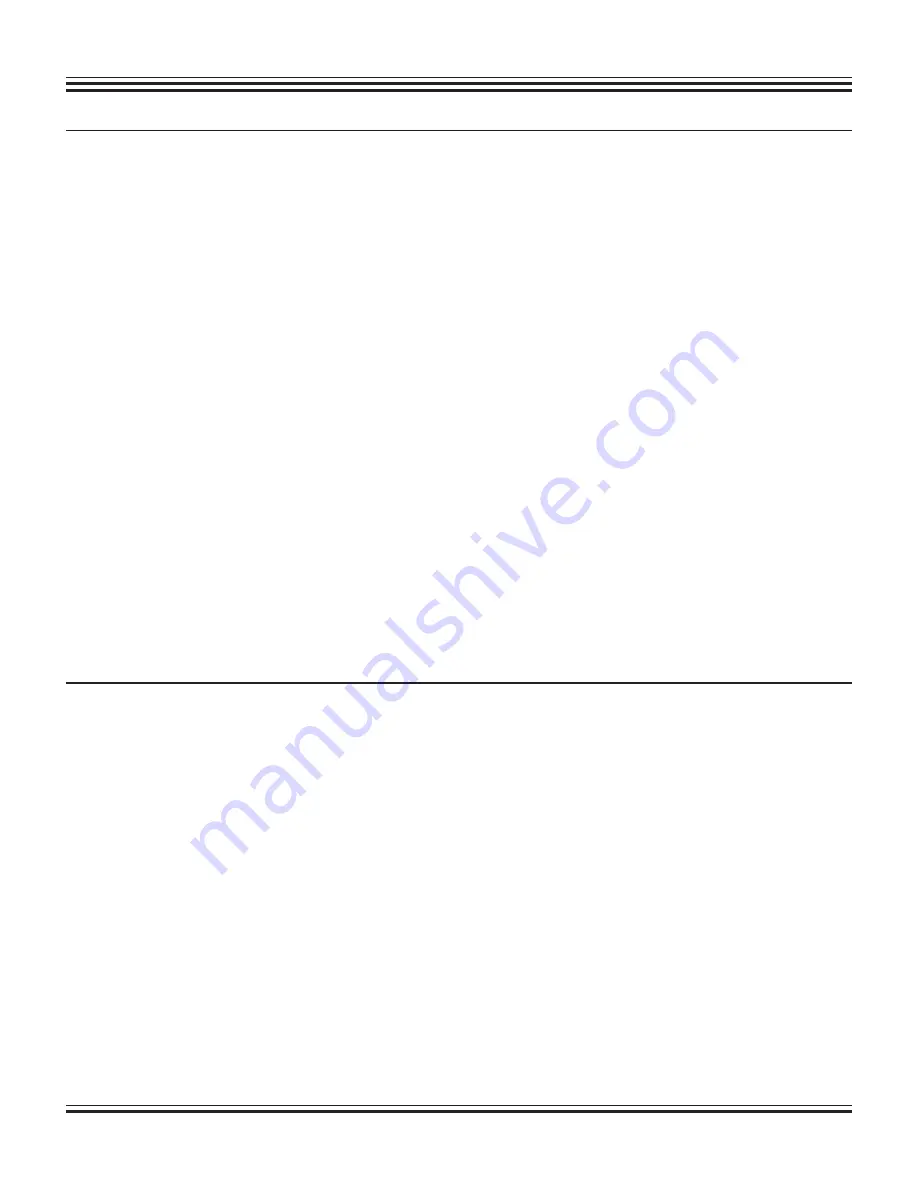
SpectraPure
®
SpectraPure
®
Inc.
480.894.5437 Call us toll-free 1.800.685.2783
2167 East Fifth St, Tempe, Arizona 85281
23
ONE YEAR LIMITED WARRANTY
SpectraPure, Inc.
®
warrants the product to the original owner only to be free of defects in material and workmanship for a period of
one year from the date of receipt. SpectraPure’s liability under this warranty shall be limited to repairing or replacing at SpectraPure’s
option, without charge, F.O.B. SpectraPure’s factory, any product of SpectraPure’s manufacture. SpectraPure will not be liable for any
cost of removal, installation, transportation or any other charges which may arise in connection with a warranty claim. Products which
are sold but not manufactured by SpectraPure are subject to the warranty provided by the manufacturer of said products and not
by SpectraPure’s warranty. SpectraPure will not be liable for damage or wear to products caused by abnormal operating conditions,
accident, abuse, misuse, unauthorized alteration or repair or, if the product was not installed in accordance with SpectraPure’s
or other manufacture’s printed installation and operating conditions, or damage caused by hot water, freezing, flood, fire or
acts of God.
SpectraPure will not be responsible for any consequential damages arising from installation or use of the product, including any
water or mold damage due to flooding which may occur due to malfunction or faulty installation, including, but not limited to
failure by installer to over- or under-tighten fittings, housings, and/or push-style fittings, or improper installation of push-style fittings.
Consumable items such as prefilters and membranes are not covered under the one year warranty.
To obtain service under this warranty, the defective system or components must be returned to SpectraPure with proof of purchase,
installation date, failure date and supporting installation data. Any defective product to be returned to the factory must be sent freight
prepaid. Documentation supporting the warranty claim and a Return Merchandise Authorization (RMA) number must be included.
SpectraPure will not be liable for shipping damages due to the improper packaging of the returned equipment and all returned goods
must also have adequate insurance coverage and a tracking number.
SpectraPure will not pay for loss or damage caused directly or indirectly by the presence, growth, proliferation, spread or any activity
of “fungus”, wet or dry rot or bacteria. Such loss or damage is excluded regardless of any other cause or event that contributes
concurrently or in any sequence to the loss. We will not pay for loss or damage caused by or resulting from continuous or repeated
seepage or leakage of water, or the presence or condensation of humidity, moisture or vapor, that occurs over a period of 14 days
or more. “Fungus” and “fungi” mean any type or form of fungus or Mycota or any byproduct or type of infestation produced by such
fungus or Mycota, including but not limited to, mold, mildew, mycotoxins, spores, scents or any biogenic aerosols.
SpectraPure will not be liable for any incidental or consequential damages, losses or expenses arising from installation, use, or any
other causes. There are no expressed or implied warranties, including merchantability or fitness for a particular purpose, which extend
beyond those warranties described or referred to above.
* The one year limited warranty does not apply to consumable items, including but not limited to, filters and cartridges
unless specifically stated above.
TERMS AND CONDITIONS:
1.
Shipping charges on units or parts submitted to our facility for repair or replacement must be borne by the registered
purchaser. After repair or replacement, the factory will return the unit or part freight prepaid to the customer.
2.
We assume no warranty liability in connection with our equipment other than as herein specified.
3.
This warranty is in lieu of all other warranties expressed or implied, including warranties of fitness for a particular purpose.
4.
We do not authorize any person or representative to assume for us any other obligation on the sale of our equipment. This is
the exclusive remedy and liability for consequential damages under any and all warranties which are excluded to the extent
exclusion is permitted by law.
5.
Proof of original purchase date must accompany all warranty claims.
6.
SpectraPure, Inc. Reserves the right to change prices without notice when necessary. All prices in the catalog are quoted in
US dollars.
7.
Claims for error in quantity or condition must be made within 10 days of receipt of material. SpectraPure, Inc. will not be
responsible for any claimed shortages not reported within 10 days. Returns other than warranty claims may be subject to
20% restocking fee.
8.
SpectraPure, Inc. cannot be held liable for damage or loss to a shipment by a freight carrier. Check shipment for damage
before acceptance or note on freight bill subject to inspection for concealed damage. Consignee must file claim. SpectraPure,
Inc. will offer as much assistance as possible.
9.
A complete credit check is required prior to shipping on a Net 30 basis. In the interim period during which credit references
are being evaluated, all orders must be prepaid until approved.
10.
All returned checks (due to insufficient funds or closed accounts) will be subjected to a
$35 penalty charge.
11.
Invoices on Net 30 accounts not paid within 30 days of shipment will be considered delinquent and will accrue Finance
charges at the rate of 1.5% per month (18% per annum).