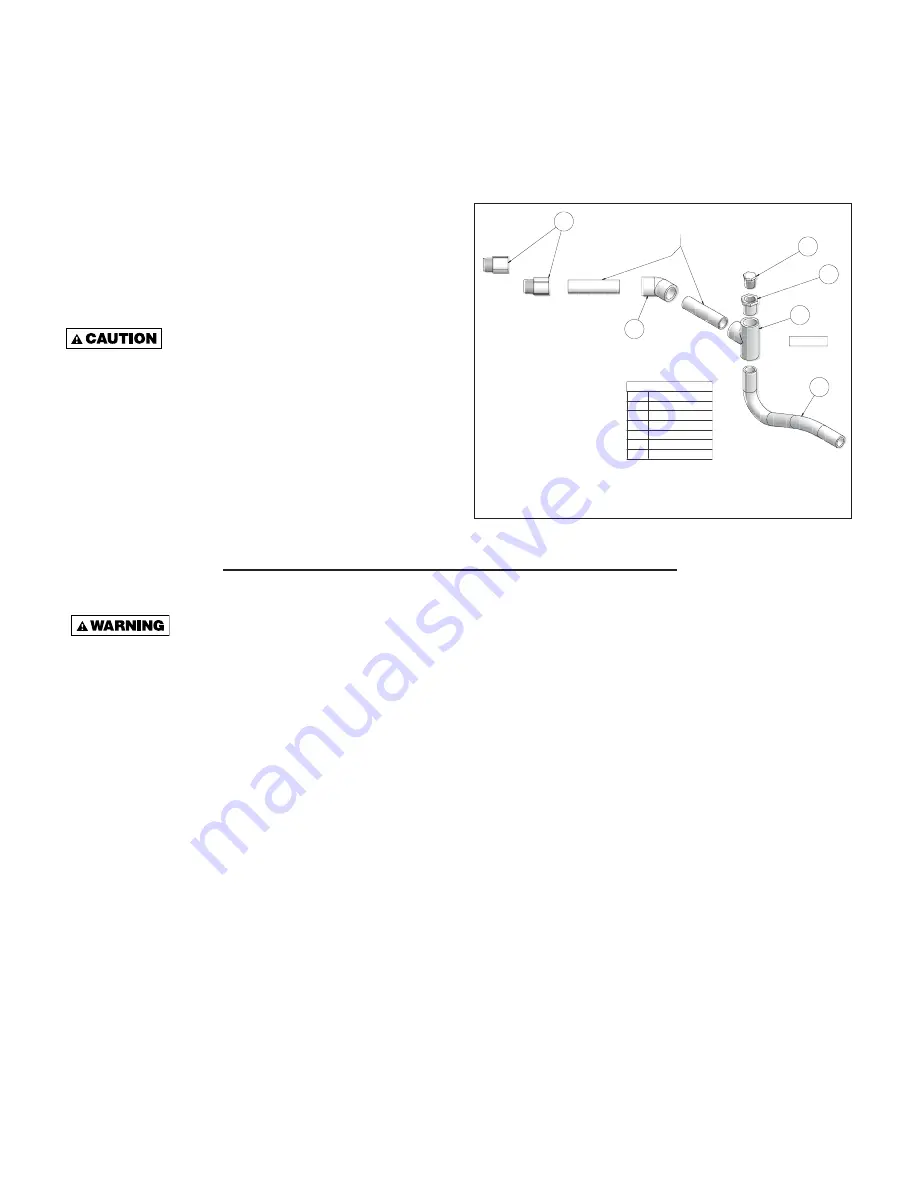
12
NOTICE: It is a requirement of the International
Mechanical Code (307.2.3) to install a secondary drain
or an auxiliary drain pan where damage to any building
components will occur as a result of overflow from the
equipment drain pan or stoppage in the condensate
drain piping from a cooling or an evaporator coil.
Follow local code requirements
Refer to Fig. 2.2 for primary and secondary condensate
drain locations. Components for the PVC condensate
trap are provided in a separate bag with fan coil unit (see
Fig. 2.12) and should be cemented together with PVC
pipe cement.
Do not use substitute trap. Do not cut
off or alter trap components.
Screw male adapter (see Fig. 2.12) into unit’s primary
condensate drain connection. Assemble and cement
remaining components together. Then cement assembly
to male adapter. The 45° elbow provides an offset from
beneath unit suction line for access to clean-out plug.
Run a condensate line from the trap to a suitable drain
that’s in accordance with local codes. Make sure the line
is pitched
1
⁄
4
" per foot.
NOTICE: The secondary drain connection requires
field supplied components to complete installation.
Follow local code requirements.
NOTICE: Never connect condensate line to a closed
drain system.
STEP 6: INSTALLING THE CONDENSATE TRAP & LINE
ITEM
1
2
3
4
5
6
MALE ADAPTER, 3/4''
DESCRIPTION
ELBOW 45
????
, 3/4''
1/2'' PLUG
3/4'' X 1/2'' BUSHING
TEE, 3/4''
P-TRAP, 3/4''
3/4'' P-TRAP ASS'Y KIT
WG0127B
NOTE: PIPE SECTIONS ARE FIELD SUPPLIED.
1
2
3
5
4
6
SEE NOTE
SECOND 3/4" MALE ADAPTER SUPPLIED FOR OVERFLOW CONN ECTION
*
*
FIGURE 2.12: CONDENSATE TRAP ASSEMBLY
STEP 7: WIRING THE UNIT
All electrical and control wiring must be installed in
accordance with the codes listed in Section 1 of this
manual. Wiring diagram is provided in Figure 2.13. A
separate 208-230/60/1 power supply is recommended for
the unit. Use standard 15-amp fuse and 16-gauge wire
from power supply to unit.
Connect power supply to Terminals L1 and L2 on the high
voltage terminal block. Connect a ground wire to the
equipment ground terminal located next to the high volt-
age terminal block.
Turn off electrical power supply
before servicing. Contact with live electric compo-
nents can cause shock or death.
The low voltage transformer in the unit has a 208 volt tap
in the primary winding (color coded RED). If unit is to be
operated with 208 volt electrical service, remove the 230
volt ORANGE lead from the L2 terminal and connect the
208 volt RED lead to the L2 terminal. Be sure to insulate
the end of the unused ORANGE lead.
Locate the room thermostat on a wall near the return air
box, between 40" to 48" from the floor. Connect the low-
voltage thermostat wiring from the room thermostat to the
low voltage control block in the unit.
Connect low voltage from air handler to condensing unit
as shown in figure 2.13.
Set DIP switches according to application. See page 14,
SpacePak G Series Control DIP switch settings.
STEP 8: INSTALLING AIR DISTRIBUTION COMPONENTS
All plenum duct and supply tubing runs as well as room
terminator locations must be in accordance with air
distribution system requirements listed in Section 1 of
this manual. Where taping of joints is required, UL181
approved tape is required.
Plenum Duct Installation
All tees, elbows and branch runs must be a minimum of 24"
from the fan coil unit or any other tee, elbow or branch run.
Keep all tees and elbows to a minimum to keep system
pressure drop on larger layouts to a minimum.
NOTICE: Refer to duct installation instructions sup-
plied with fan coil unit or follow manufacturers
instructions supplied with other duct system types.
Summary of Contents for ESP-G SYSTEM
Page 10: ...10 FIGURE 2 9 FIGURE 2 8...
Page 13: ...FIGURE 2 13 WIRING DIAGRAM 13...