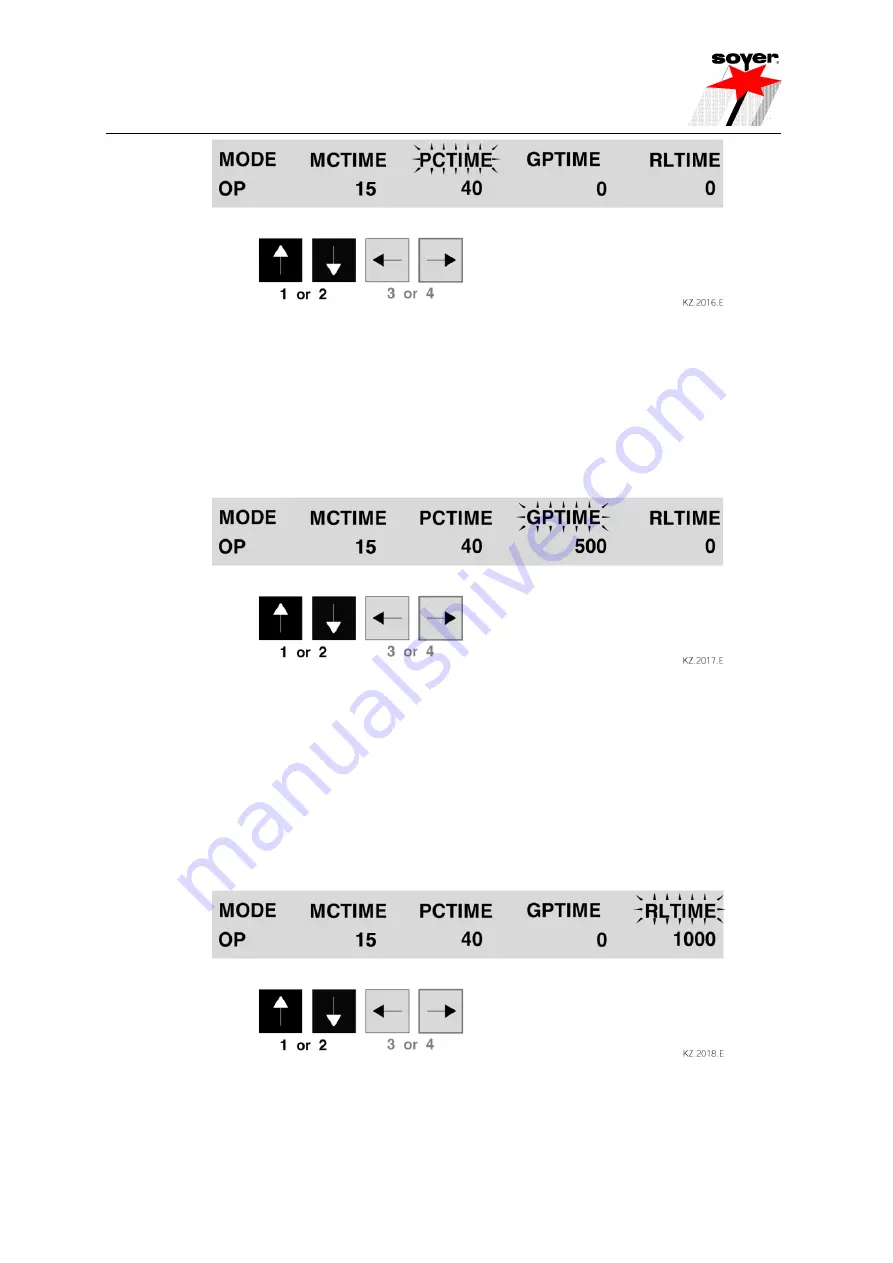
BMK-8 U / BMK-12 W
35
6.1.1.3
GPTIME (Gas preflow time)
The gas preflow time is the period of time, during which the shielding gas valve is open before starting
the welding process and remains open after the welding process has been completed. Set value "0"
when welding without shielding gas.
• Select function "GPTIME" by pressing either function key "arrow left”
(3)
or "arrow right"
(4)
.
• Select the corresponding value for the gas preflow time from 0 - 9900 ms in 100 ms-steps by
pressing function key "arrow up"
(1)
or "arrow down"
(2)
.
6.1.1.4
RLTIME (reload time)
The reload time is the period of time the blast air valve requires for transporting the stud from the
universal feeder to the welding gun or welding head. The longer the blast air hose is, the higher you
have to set the reload time correspondingly. If automatic reload is not required, set value "0". The
reload time can only be used in connection with optional "automatic operation" (feeder connection).
• Select function "RLTIME" by pressing either function key "arrow left"
(3)
or "arrow right"
(4)
.
• Select the corresponding value for the reload time from 0 - 9900 ms in 100 ms-steps by either
pressing function key "arrow up"
(1)
or "arrow down"
(2)
.
• If you are not satisfied with the welding results, you may change the set welding parameters at any
time.