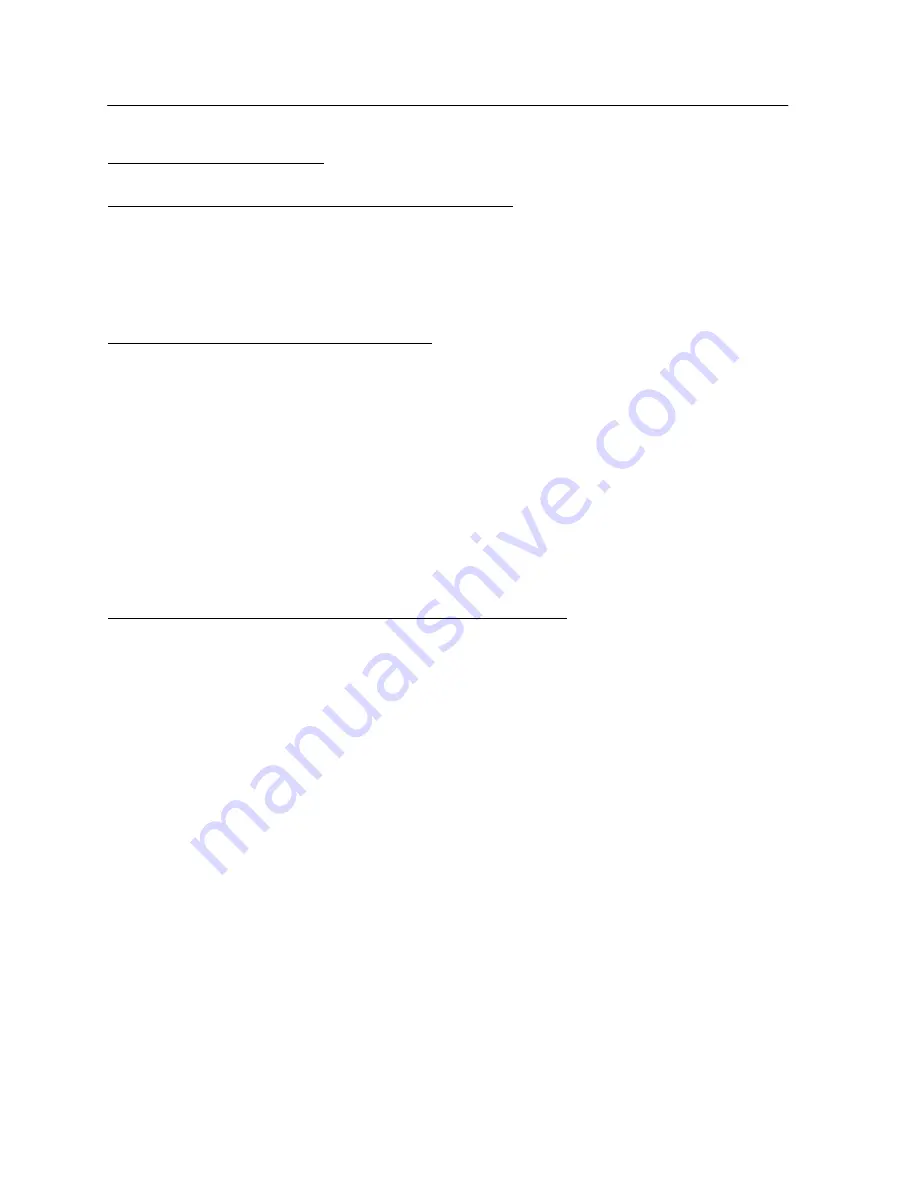
SERVICE INFORMATION
SECTION 6:
MODELS: SC-2 & SC-3
CABINET CONTROL PROBLEMS (cont'd)
Water is not being supplied to Heat Exchanger (cont'd)
This valve is similar in construction to the Exhaust Solenoid Valve mentioned
previously and may malfunction due to sealants lodging in the pocket of the
valve. Refer to page 17 Cooker Problems - "Water accumulation in the bottom
of compartment" - for procedure of cleaning this valve.
Boiler Blowdown Valve does not drain
When the appliance is turned OFF, the Boiler Blowdown Valve is de-energized
and consequently opens and the water contained in the Heat Exchanger being
under pressure, should be blown through this valve and be noticeably visible
exhausting out the appliance Drain. However, if the blowdown operation
appears to function rather sluggishly or not at all, then assume that con-
siderable sealant may be lodged in the drain pipe and/or the valve. Dis-
connect the valve from the drain line and inspect both the valve and the
drain pipe fixed to the Heat Exchanger. If considerable sealants or lime
build up is apparent then not only the valve but also the Heat Exchanger and
Water Level Control must be thoroughly cleansed. Refer to Heat Exchanger on
Removal of Sealants etc. for proper procedure.
Heat Exchanger achieves pressure slower than normal
If the Heat Exchanger requires considerably more time than 25 minutes to
achieve normal operating pressure (9-12 p.s.i.), then assume that heavy build
up of sealant has completely coated the internal copper steam coil and
consequently heat transfer through the, coil is hampered by the insulating
effect of the sealant.
As mentioned in the previous symptom, an inspection of the Boiler Blow-down
Valve should be undertaken to verify presence of sealant.
Disconnect all plumbing to the Heat Exchanger at unions. Remove both
fastening bolts from the Heat Exchanger front Support Bracket. Note that
back Support Bracket has two open ended slots to provide for ease of removal.
If the Heat Exchanger cannot be dislodged easily from back Support Bracket,
then with hammer strike a few sharp blows on back of Support Bracket. Remove
Heat Exchanger completely from Cabinet and lay it along its right side on
floor. Plug or cap all pipe fittings with the exception of the two
projecting the highest.
Prepare a solution of one part Muriatic (Hydrochloric) Acid to seven parts of
water and pour into Heat Exchanger through one of the remaining open pipe
fittings. The other open pipe is to allow air to exhaust from vessel when it
is displaced by the solution.
21
Summary of Contents for CSC-24S
Page 10: ...PERIODIC MAINTENANCE SECTION 4 MODELS SC 2 SC 3 8 FIG 2...
Page 14: ...PERIODIC MAINTENANCE SECTION 4 MODELS SC 2 SC 3 FIG 3 12 EXHAUST TO DRAIN STEAM IN...
Page 25: ...PARTS LIST SECTION 7 COMPARTMENT DOOR ASSEMBLY FIG 4 23...
Page 28: ...PARTS LIST SECTION 7 MODELS SC 2 SC 3 COOKER ASSEMBLY FIG 5 25...
Page 30: ...PARTS LIST SECTION 7 COOKER CONTROLS FIG 6 27...
Page 32: ...PARTS LIST SECTION 7 GENERATOR CONTROL BOX ASSEMBLY FIG 8 29...
Page 34: ...PARTS LIST SECTION 7 GENERATOR ASSEMBLY FIG 5 31...
Page 36: ...PARTS LIST SECTION 7 CABINET FIG 9 33...
Page 38: ...WIRING DIAGRAM MODELS SC 2 SC 3 SECTION 8 35...
Page 39: ...WIRING DIAGRAM MODELS EDA 2 SCDA 2 GDA 2 DDA 2 SUPPLEMENT SECTION 9...